Communication ports in PLC play an important role as a bridge, helping devices in industrial automation systems communicate and exchange data effectively. Choosing the right communication port with the required data transmission speed is extremely important. This article will provide an overview of common types of communication ports, how to choose and note when using to optimize system performance.
What is Communication Ports?
Communication Ports in PLC are communication ports that allow PLC to connect to peripheral devices or other systems to exchange data. Communication ports in PLC play an important role in connecting PLC with other devices such as HMI, sensors, and actuators to form a complete automation system.
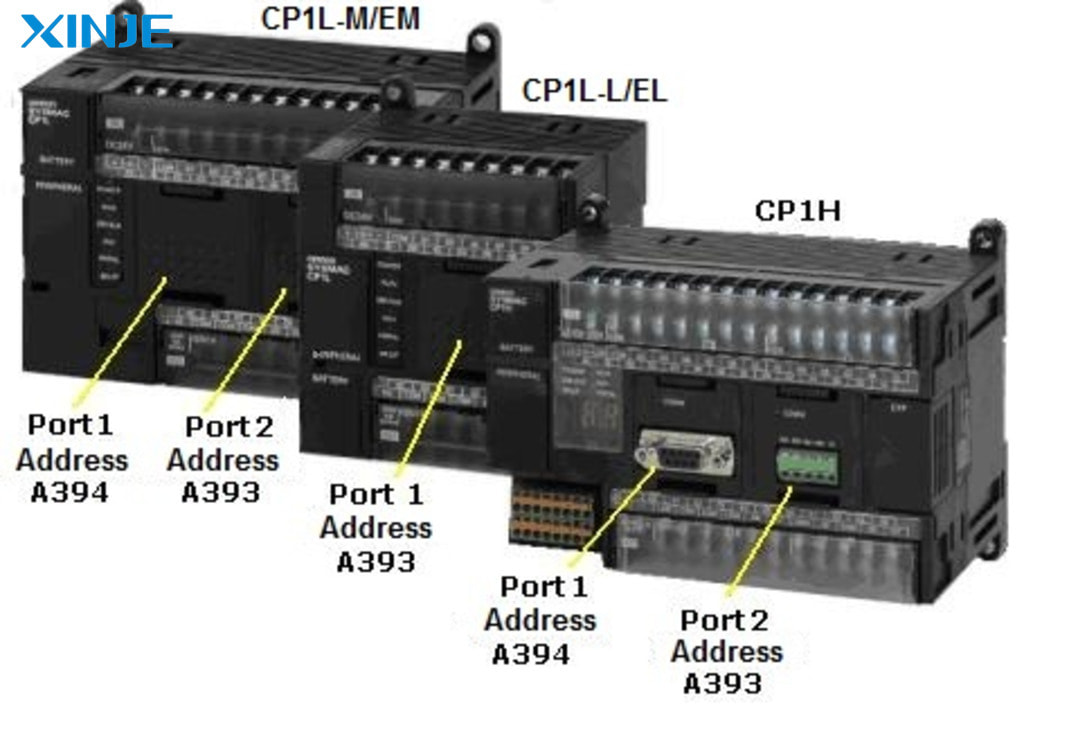
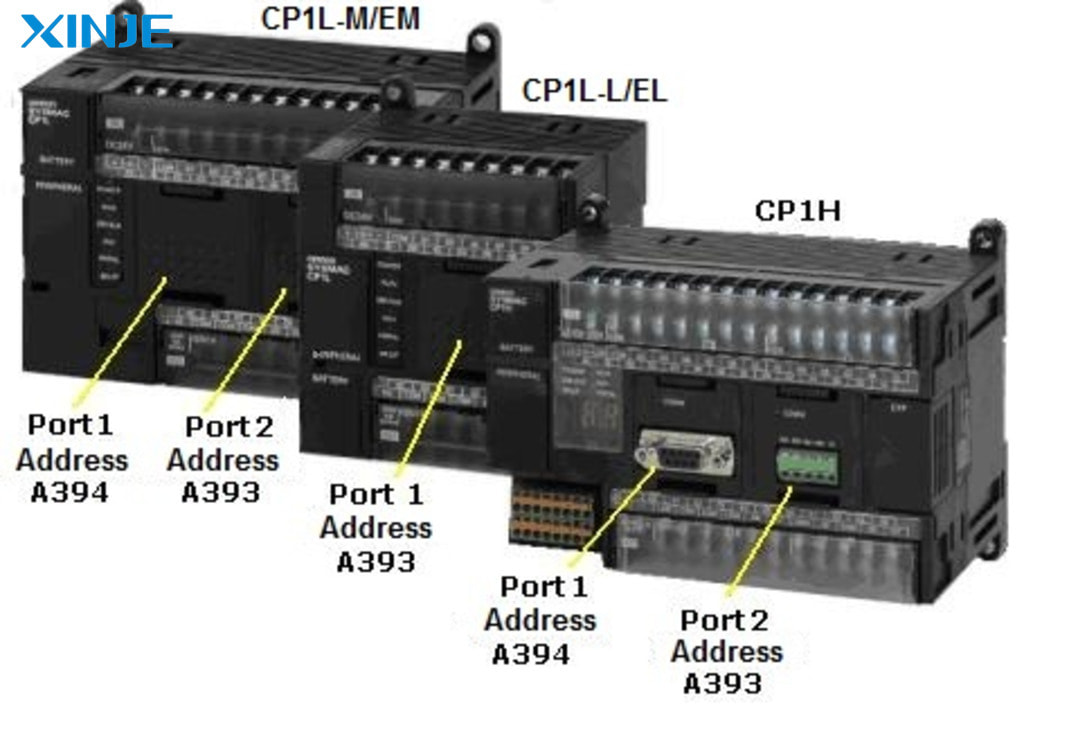
How many types of communication ports are there?
Popular communication ports today include RS-232, RS-485, Ethernet, USB, CANbus, PROFIBUS, and PROFINET. Each type of port has its own advantages and disadvantages, so businesses need to pay attention to choosing the communication port that suits their needs.
Serial communication port
- RS-232 is a serial communication standard that uses point-to-point data transmission between two devices, such as a PLC and a computer or sensor. This is one of the first communication standards widely used in industry.
- RS-485 is an upgraded version of RS-232, allowing multipoint communication (allowing up to 32 devices to be connected), meaning that a PLC can connect to multiple devices on the same transmission line. RS-485 supports data transmission over longer distances and works well in noisy industrial environments.
Compare the differences between RS-232 and RS-485
RS-232 | RS-485 | |
Communication style | Point-to-point | Multi-point, support multiple device connection |
Number of connected devices | 2 devices (1 master, 1 slave) | Maximum 32 devices |
Transmission Distance | Max. 15m | Max. 1.2km |
Data Transmission Rate | 3 Mbps | 40 Mbps |
Transfer type | Full duplex | Half duplex (2 wires), full duplex (4 wires) |
Contacts in use | TxD, RxD, RTS, CTS, DTR, DSR, DCD, GND* | DataA, DataB, GND |
Max. Driver Output Voltage | +/-25V | -7V to +12V |
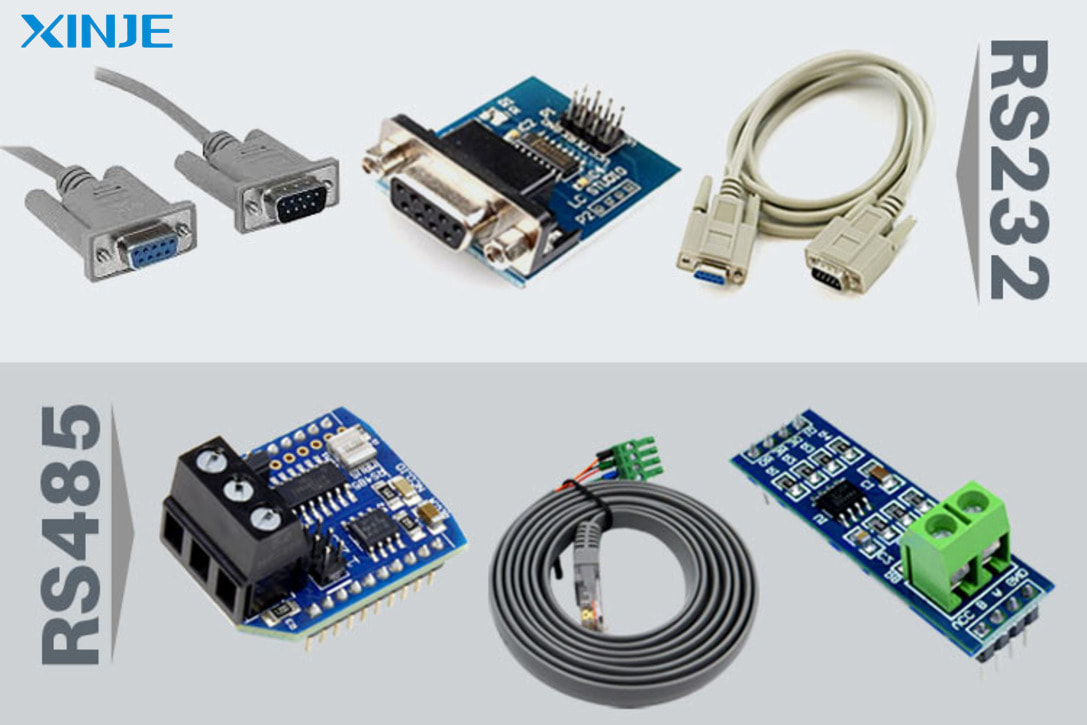
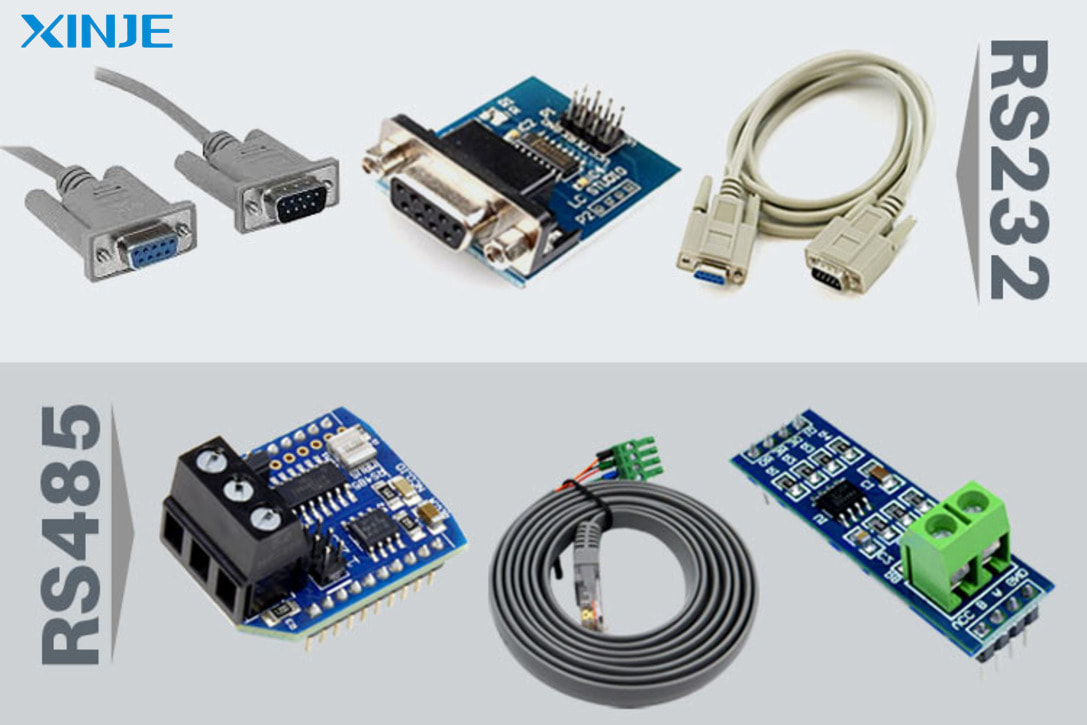
Ethernet Ports
- Ethernet Ports – also known as Ethernet jacks or sockets are network communication interfaces that use the Ethernet protocol to transmit data at high speeds. The primary function of an Ethernet port is to establish a direct Internet connection from your computer to network devices. This is a common type of communication port in modern PLC systems, allowing the PLC to connect to other devices over a local area network (LAN) or wide area network (WAN).
- Ethernet ports support many industrial protocols such as Modbus TCP/IP, Profinet, EtherNet/IP, making the PLC compatible with a wide range of devices and systems.
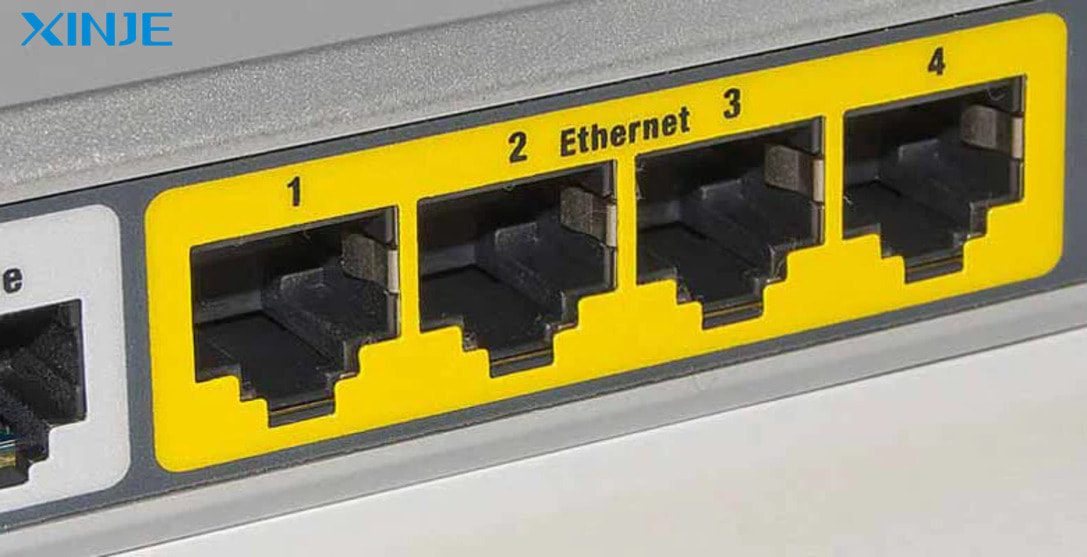
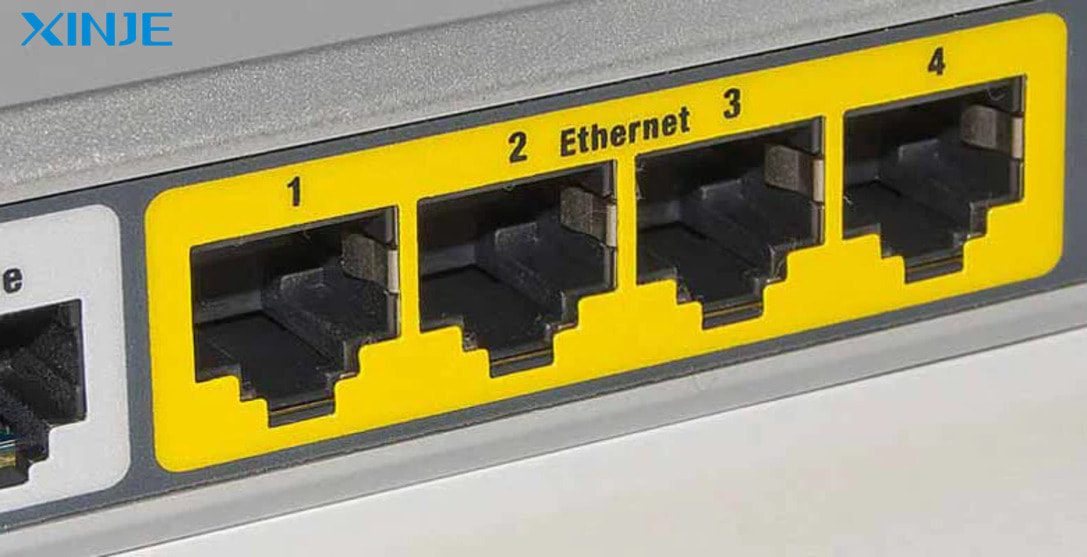
USB Ports
- USB (Universal Serial Bus) Ports are standard communication ports designed to connect PLCs to devices such as computers, USB drives, or programming devices. This port is primarily used for data backup, firmware updates, and quick programming.
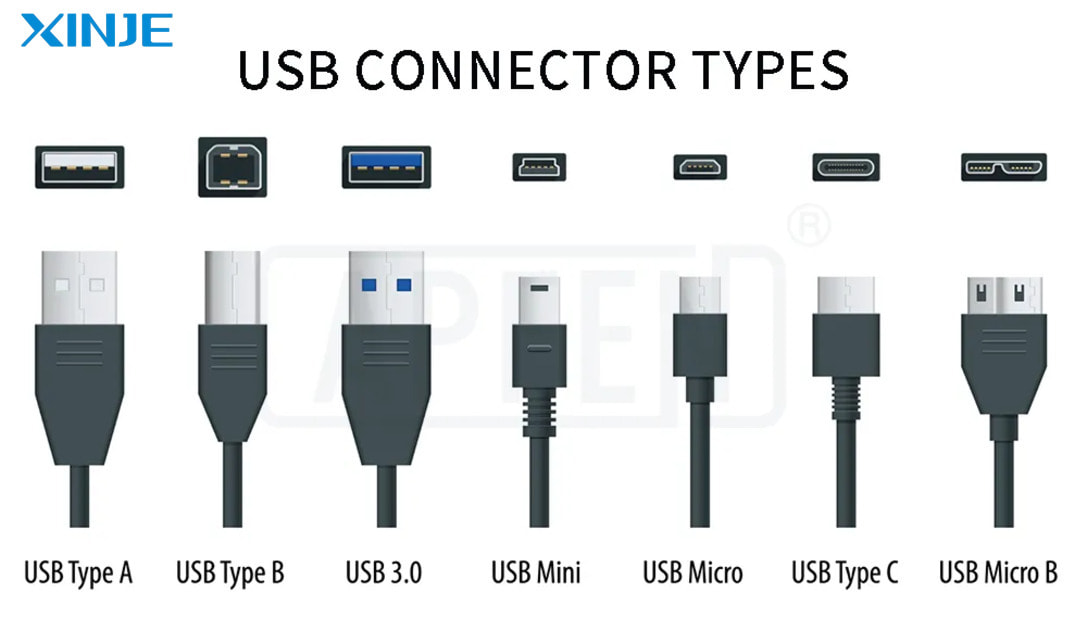
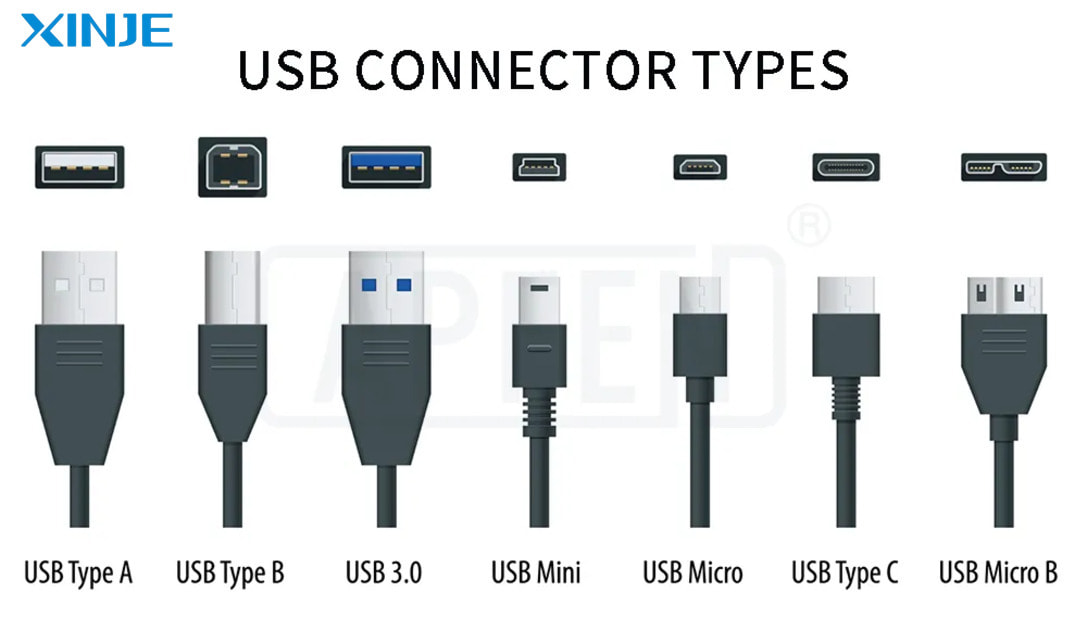
Wireless Communication
Wireless Communication is a method of wireless communication between PLCs and other devices, using technologies such as Wi-Fi, Bluetooth, or Zigbee. It eliminates the need for physical wiring, allowing flexible connections in automation systems.
- PROFINET is a communication protocol based on industrial Ethernet technology, developed to replace and improve PROFIBUS. PROFINET allows high-speed connection of automation devices and good integration in Industry 4.0 environments.
- PROFIBUS is an industrial standard communication protocol based on serial communication technology developed by Siemens in 1989. It allows automation devices such as PLCs, sensors, and actuators to communicate with each other over a field.
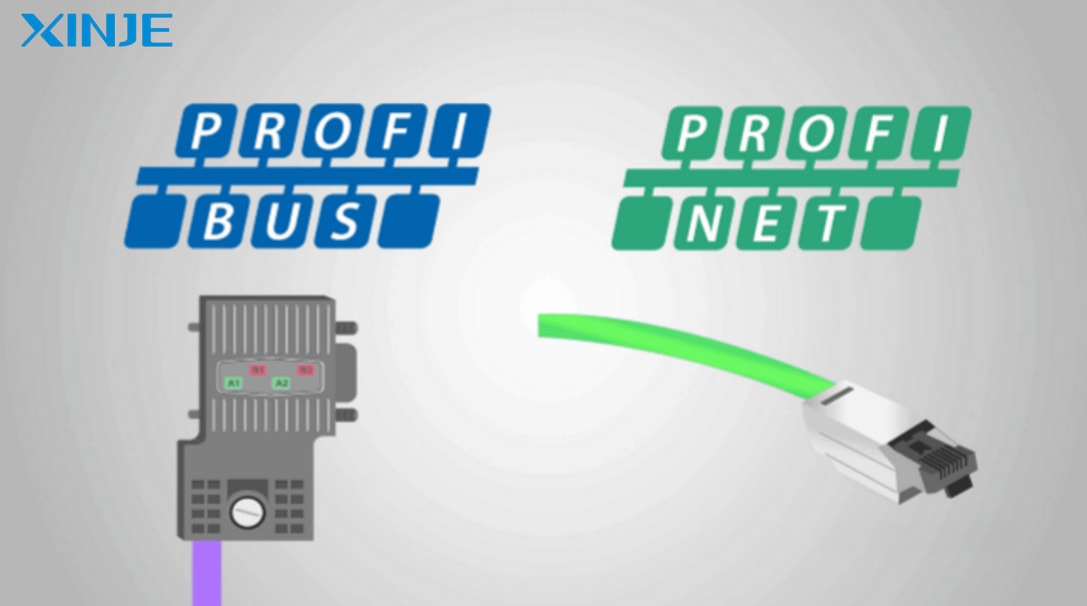
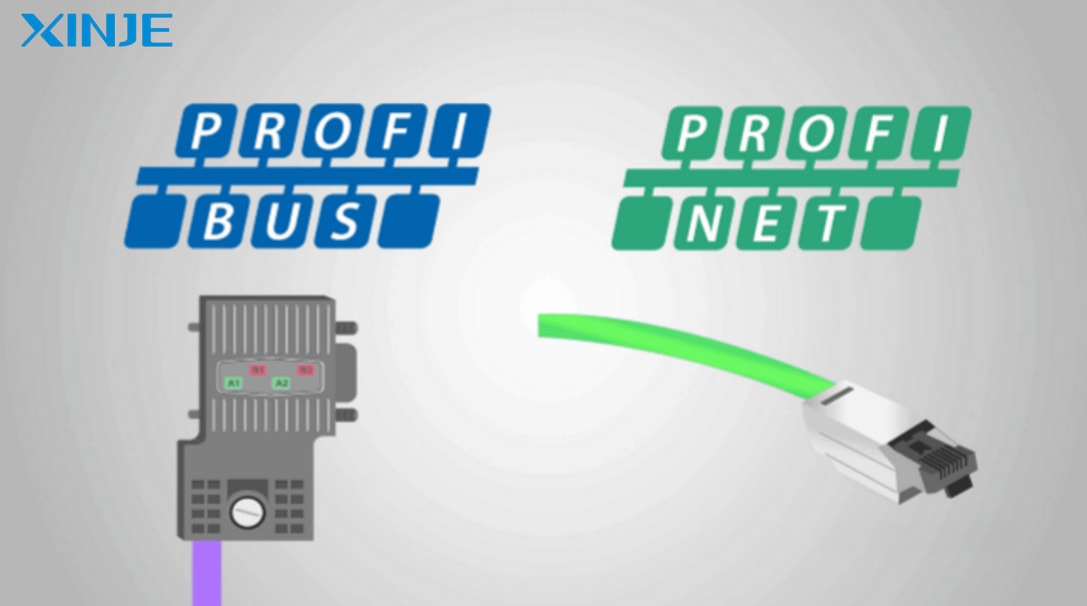
What are the considerations when selecting and using Communication Ports?
Choosing and using the right type of communication ports (Communication Ports) in PLC is a decisive factor for the performance and stability of the automation system. Here are some important considerations that you need to consider:
- Number of connected devices: If you need to connect many devices, scalable ports such as Ethernet or Fieldbus buses are a good choice.
- Data transmission speed: Depending on the scale of the enterprise system. For example, Ethernet is suitable for real-time communication and large data, while low speeds such as RS-232 or RS-485 are enough for simple systems. Choosing the wrong speed can cause delays or waste resources.
- Scalability and integration: Choose a communication port that supports easy expansion for future projects.
- Operating environment: If the working environment has high electromagnetic interference, choose ports with good anti-interference capabilities.
- Reputable supplier: Currently, many units are selling Communication Ports on the market, so businesses need to be wise in choosing.
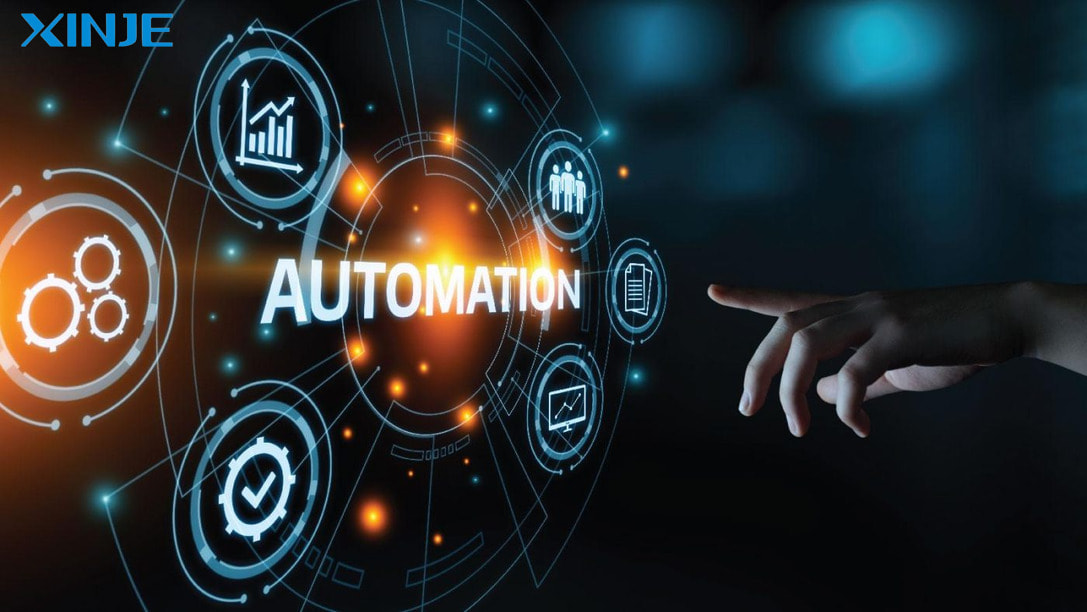
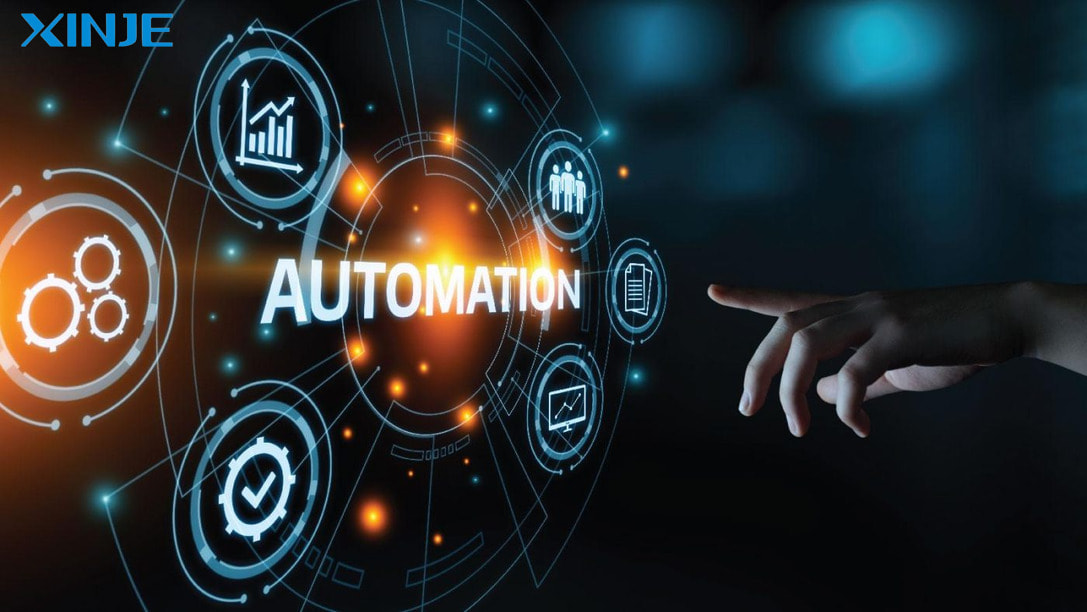
Conclusion
Communication ports in PLCs are the core element that helps connect and exchange data between devices in industrial automation systems. Each type of port, from traditional standards such as RS-232, RS-485 to modern technologies such as Ethernet and PROFINET, has its own advantages, disadvantages and applications. Choosing the right communication port should be based on factors such as data transmission speed, connection distance, environmental conditions and system scalability.
In the context of Industry 4.0, modern ports such as Ethernet and PROFINET not only support high speed and real-time communication capabilities, but also integrate easily with IoT and cloud solutions, contributing to improving production efficiency and optimizing operating processes. However, traditional standards such as RS-485 still play an important role in applications that require low cost and high stability.
Understanding the characteristics of each type of communication port and applying them appropriately not only helps the system operate effectively, but also increases security, reduces operating costs and flexibly meets the future development needs of the business.