Safety PLC or safety programmable logic controller is a device widely used in other industrial automation factories. This device has the same operating principle as other standard PLCs but is updated with additional operating features such as timely and accurate monitoring and error detection.
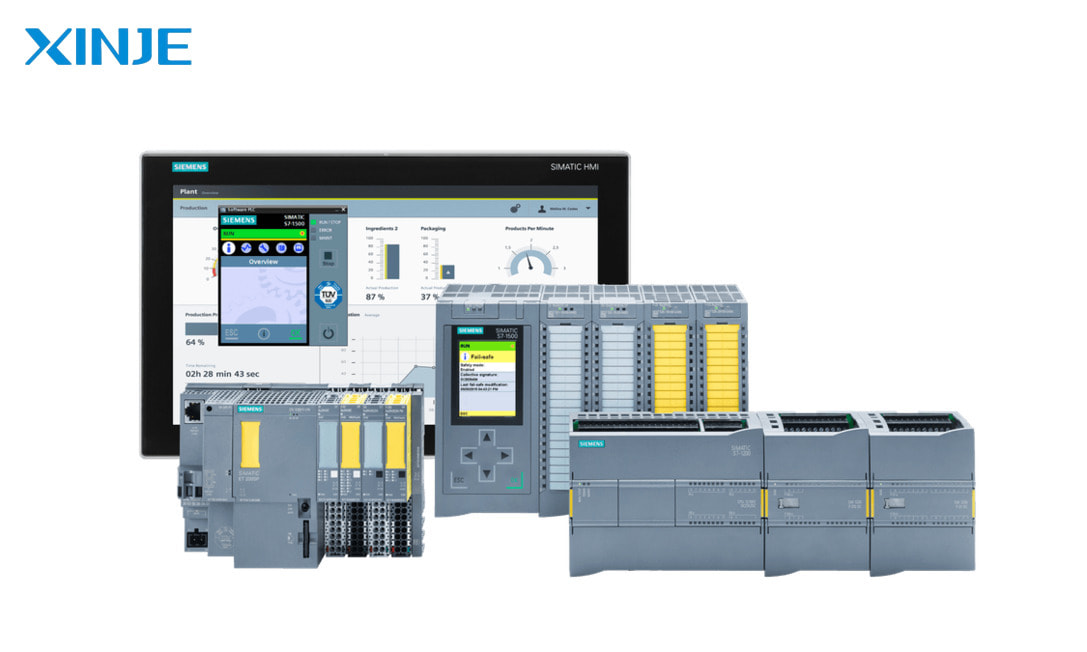
It is possible to say that safety PLC is a more advanced version than conventional PLCs. Although the initial investment cost of the device is higher, with the benefits it brings, this is still a potential control device that many people want to own.
How much does the safety PLC cost?
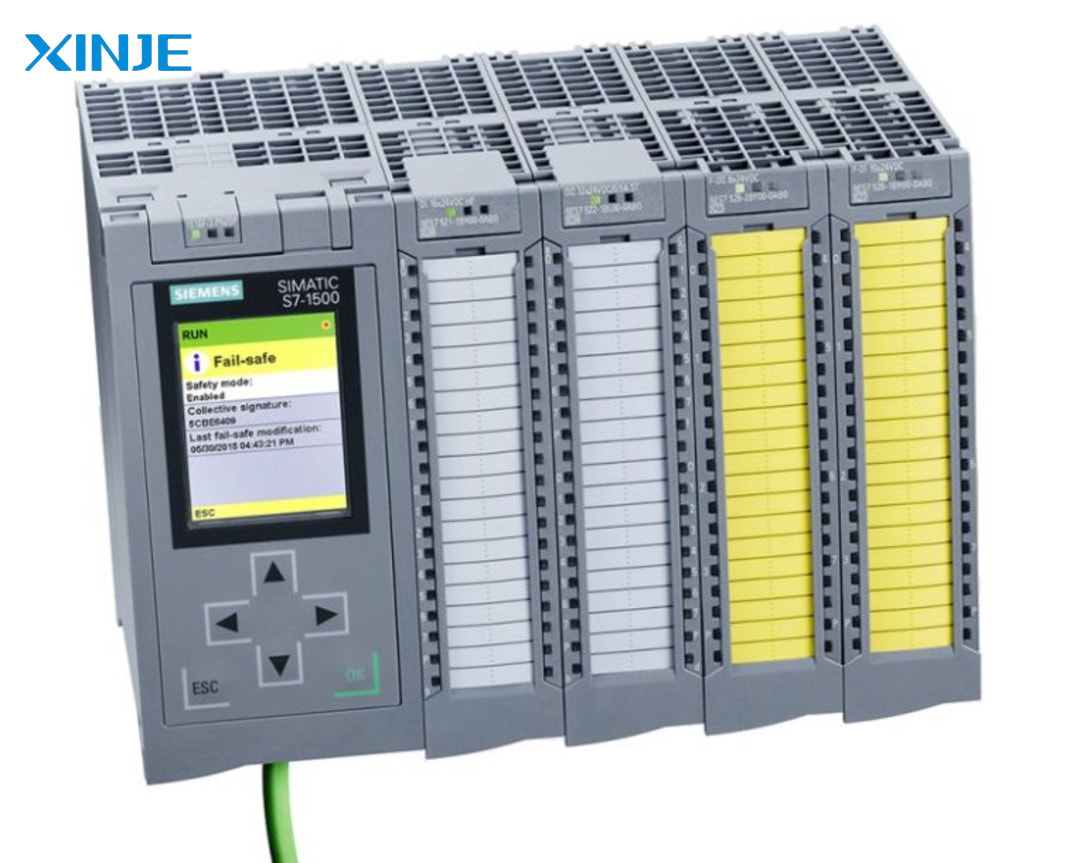
Safety PLC is a highly reliable and safe device, so the cost of the device is also a top concern for many users. And the common question is whether the cost of installing a safety PLC is expensive or cheap. However, the price of a PLC device also depends on many other factors such as configuration, model, brand, and operating capacity… Many factors affect the price of a safety PLC device. According to the current average price, the price of a safety PLC controller usually ranges from $500 to $5000.
What is the difference between safety PLC and regular PLC?
Safety PLC | Regular PLC |
Specialized design, performing related tasks such as control and monitoring, meeting international standards, and maximum protection in emergencies. | Not the optimal safety solution, it is only suitable for applications that do not require a high level of safety. |
Equipped with redundant processors and communication channels to ensure continuous operation even in the event of a failure | Lacking these redundancy features, it is only suitable for applications that do not require high reliability. |
Programming is more complex and time-consuming, requiring additional steps to meet safety standards and test protection functions | Programming is simpler, requiring fewer additional steps to ensure special safety |
More expensive | Cheaper |
How does the safety PLC work?
The way safety PLCs operate is not much different from other conventional PLCs, but they are upgraded in terms of safety through the following principles:
- Redundancy: Safety PLCs are equipped with a backup processor and circuit in the system in case a component fails, it will be replaced immediately without interrupting the efficiency of the process.
- Self-testing mechanism: This device has the ability to self-test and detect potential errors early, preventing incidents and maintaining safety.
- Comply with safety protocols: Safety PLCs always comply with strict safety standards such as ISO 13849 and IEC 61508, ensuring that all functions are deployed and tested according to the highest safety requirements.
What are the benefits of using the safety PLC?
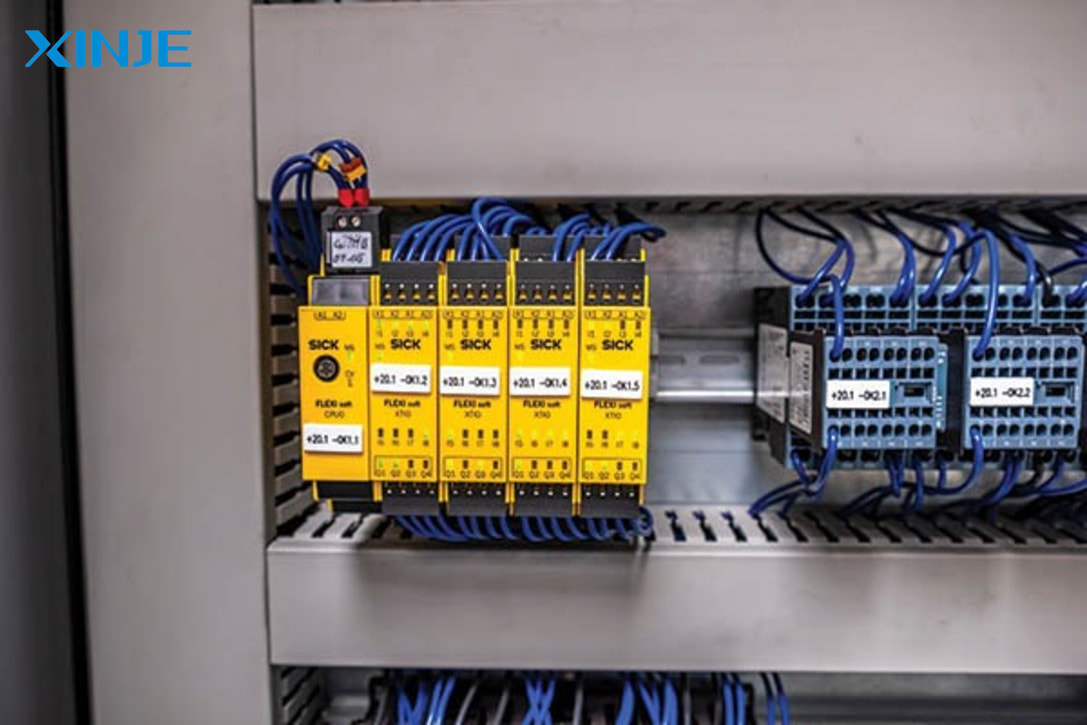
Safety PLC is a popular device in the automation manufacturing industry with many outstanding advantages such as:
- Increased reliability and safety: the safety PLCs are much more reliable and safe than other standard PLCs due to their ability to detect and warn of faults quickly.
- Space optimization: by reducing the number of components and wires, safety PLCs have helped save panel space during process control in many production lines.
- Fast installation speed: the device has facilitated easy installation, limited wiring errors, and minimized risks during operation.
- Cost-effective: although the initial investment cost is higher than other standard PLCs, in terms of long-term benefits, this device makes it easy to reuse programming code and saves costs in large applications.
What are the challenges when using safety PLC?
Along with the outstanding benefits, there are also certain challenges in the process of using the device that users need to pay attention to such as:
- Investment cost: high initial investment cost will be a big challenge for many production facilities with limited budgets.
- Familiarity: Safety PLC is a device that applies many new technologies, so it takes time for technicians to get used to how to use this device.
- Reliability: This is a fairly new device, so many people are still hesitant about the reliability of the device despite having gone through many certification processes.
What are the steps to design a safety PLC program?
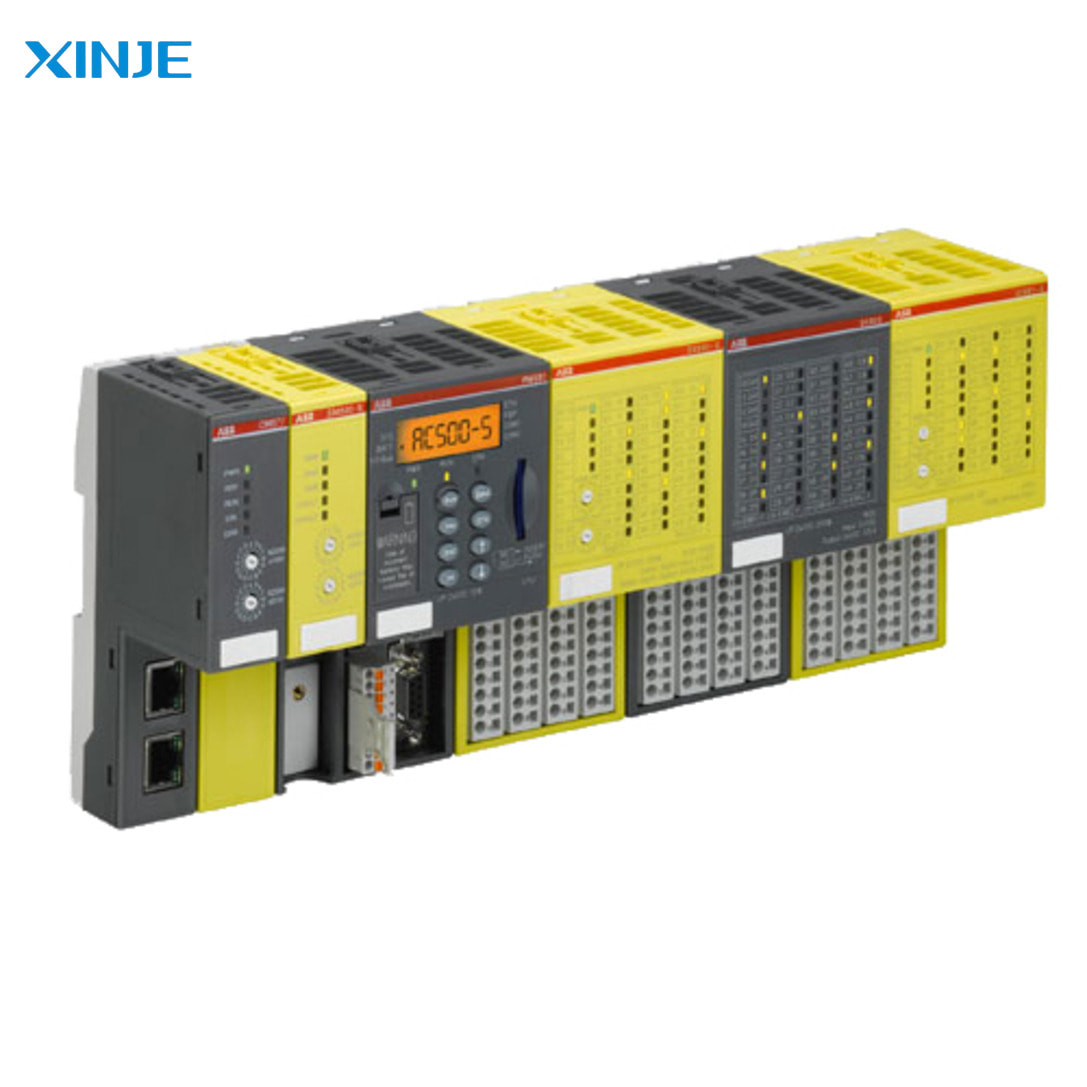
Designing a safety PLC requires completing the following 5 steps:
- Identify safety requirements: Identify necessary safety functions such as emergency stop, and interlock. Evaluate the level of risk carefully to ensure that the PLC meets the above requirements well.
- Choose the right safety PLC: Choose a safety PLC that suits your needs, budget, and performance to meet the criteria that users want, from which you will choose a comprehensive safety PLC solution.
- Develop a safety program: Safety PLCs are often programmed using ladder logic or block diagrams, ensuring that each function is thoroughly tested and easily detected when errors occur.
- Authentication and locking the program: Operators should thoroughly test the safety functions of the device, and then lock the code to prevent modification to ensure the integrity of the device.
- Deployment and monitoring: After installing the device, users should regularly monitor and track the PLC periodically to maintain its operating performance and accuracy.