What is the I/O Monitoring? I/O Monitoring, short for Input/Output Monitoring, is the process of observing and tracking the real-time status of signals exchanged between field devices and the control system, typically through an HMI connected to a PLC.
In automation systems, input signals might come from sensors, switches, or buttons, while output signals control devices such as motors, lights, valves, or actuators. I/O monitoring allows users to view these signals in real-time on an HMI screen, helping operators detect faults, verify logic, and maintain optimal operation of industrial processes.
What components does I/O monitoring include?
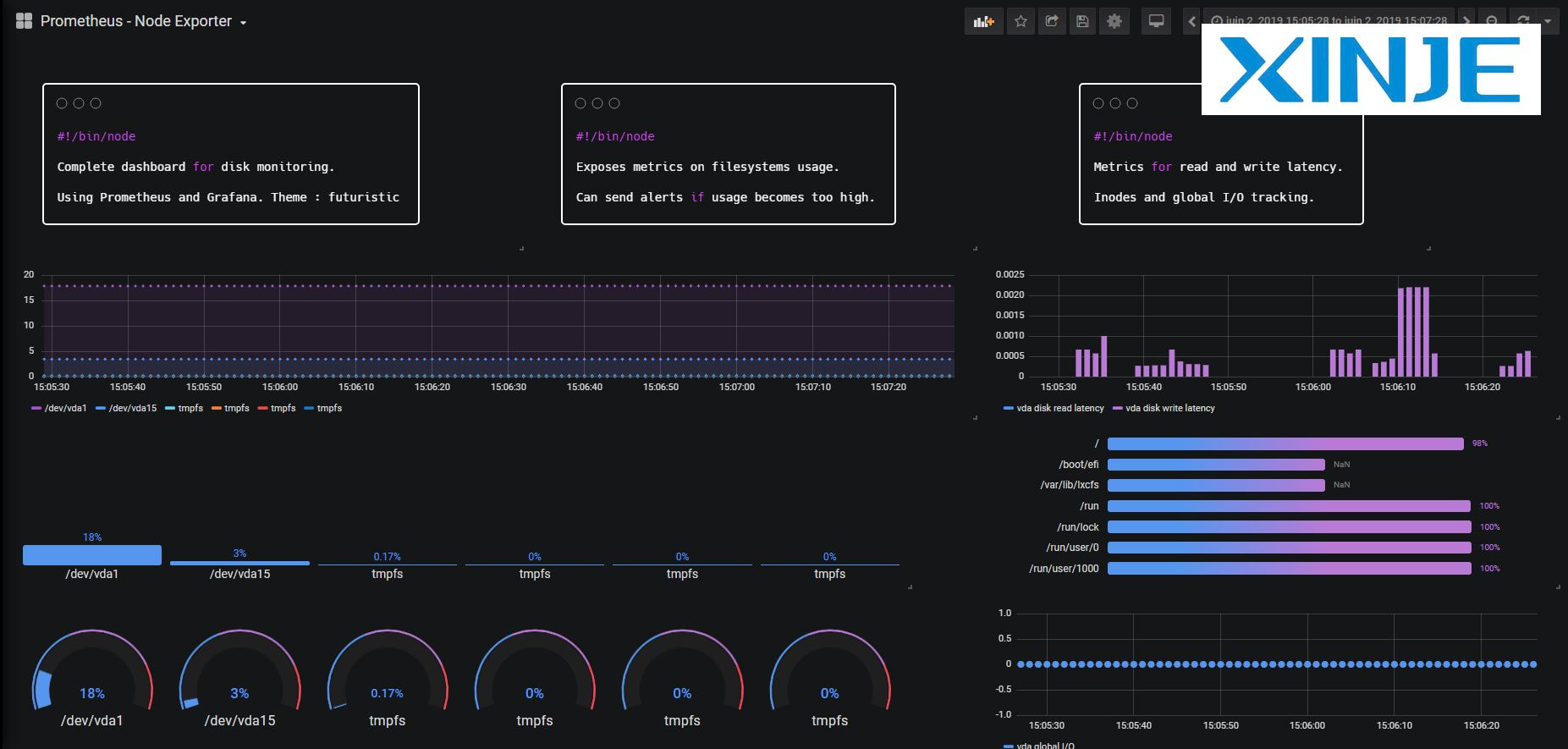
I/O monitoring is not a standalone tool; it consists of a combination of hardware and software components that work seamlessly together. The main components include: PLC, HMI, field devices, communication protocols…
- PLC: This is the brain of the automation system. The PLC reads inputs from the field, performs control logic, and sends corresponding outputs.
- HMI: This is a graphical interface that allows the operator to interact with the PLC. The HMI visualizes the status of inputs and outputs and often includes I/O diagnostic tools.
- Field devices include: Input devices, such as sensors, limit switches, push buttons… Output devices include actuators, solenoids, relays, and indicator lights.
- Communication Protocol: I/O data is transmitted between HMI and PLC via protocols such as Modbus RTU/TCP, Ethernet/IP, Profinet, and OPC UA…
- I/O tags and address mapping: Each I/O point has a specific address or tag name in the PLC program, which is mapped to the HMI for monitoring. The proper configuration ensures accurate data visualization.
How does I/O monitoring work?
I/O Monitoring relies on the continuous exchange of data between the PLC and the HMI. The process takes place through 5 basic steps as follows
- Step 1: Input Detection – Field devices (such as sensors or buttons) generate input signals, which are received by the PLC through physical input terminals.
- Step 2: Logic Execution – The PLC program processes these inputs based on control logic. It can trigger specific actions if conditions are met.
- Step 3: Data Update to the HMI using a communication protocol. The PLC then sends the updated I/O status to the HMI. This data is refreshed in real time.
- Step 4: Visualization – HMI displays I/O status directly on the screen using visual elements such as status indicators, alarms, and real-time diagnostic graphs
- Step 5: Operator interaction – Operators can observe system behavior, troubleshoot abnormalities, and even force or override I/O points during maintenance
Why is I/O monitoring important?
I/O monitoring provides important visibility into what is happening at the ground level of an automation system. But some of its standout features include:
- Fast troubleshooting: If a machine fails, I/O monitoring can immediately tell whether the problem is an input or output signal.
- Downtime prevention: Early detection of abnormal I/O states helps prevent system-wide failures. For example, detecting a stuck sensor or faulty relay before it causes production downtime.
- System optimization: With insight into the signal flow, operators can adjust processes to be more efficient, identifying slow response times, redundant signals, or unnecessary delays.
- Compliance & Logging: Some industries require logging of I/O events for traceability and compliance. The I/O monitoring system can be configured to log these activities.
What should be noted when using I/O monitoring?
While I/O Monitoring is a powerful tool, effective use depends on careful configuration and awareness of best practices. There are a few things to keep in mind when using this tool to ensure optimal operational efficiency.
- Correct Tag Mapping: Ensure that each HMI tag corresponds exactly to the PLC’s memory address. Incorrect mapping can lead to misinterpretation of data.
- Update Rate Configuration: Set the appropriate scan interval for I/O updates. Too fast can overload the system, or too slow can cause a delay in response.
- Security & Permissions: Restrict access to advanced features such as forcing I/O values or ignoring inputs. Only trained personnel should perform such actions.
- Alarm Integration: Combine I/O monitoring with an alarm system. For example, if the motor does not start after the start command, trigger an alarm based on the I/O logic.
- Pre-deployment testing: Always validate the I/O monitoring screen during system testing. Check that the screen displays correct status, responsiveness, and a user-friendly design.
I/O Monitoring is like any other tool to ensure optimal system operation, and operators need to pay close attention to these characteristics to promptly handle problems if they occur.
Conclusion
In short, I/O monitoring is not just a convenience, it is a necessity. By providing real-time visibility into system behavior, it empowers operators, engineers, and maintenance teams to detect problems early, verify logic, ensure safety, and maintain smooth operations.
Whether you are designing a new HMI interface or upgrading an existing system, make sure I/O Monitoring is well-integrated, user-friendly, and secure. When implemented correctly, it becomes a powerful ally in your automation strategy, saving time, preventing errors, and keeping production on track.