What is the SCADA Integration? In the rapidly evolving world of industrial automation, SCADA integration has become the cornerstone of smart manufacturing and efficient operations. SCADA (Supervisory Control and Data Acquisition) is a control system architecture that uses computers, network data communications, and graphical user interfaces (GUIs) to monitor and control industrial processes. When SCADA systems are successfully integrated with HMIs, they provide real-time insights, enhanced control, and data-driven decision-making in industrial environments.
In this article, we will explore the core functions of SCADA, the different types of SCADA systems, how they work, how to integrate SCADA with HMIs, and what makes SCADA different from OT.
What is the function of SCADA?
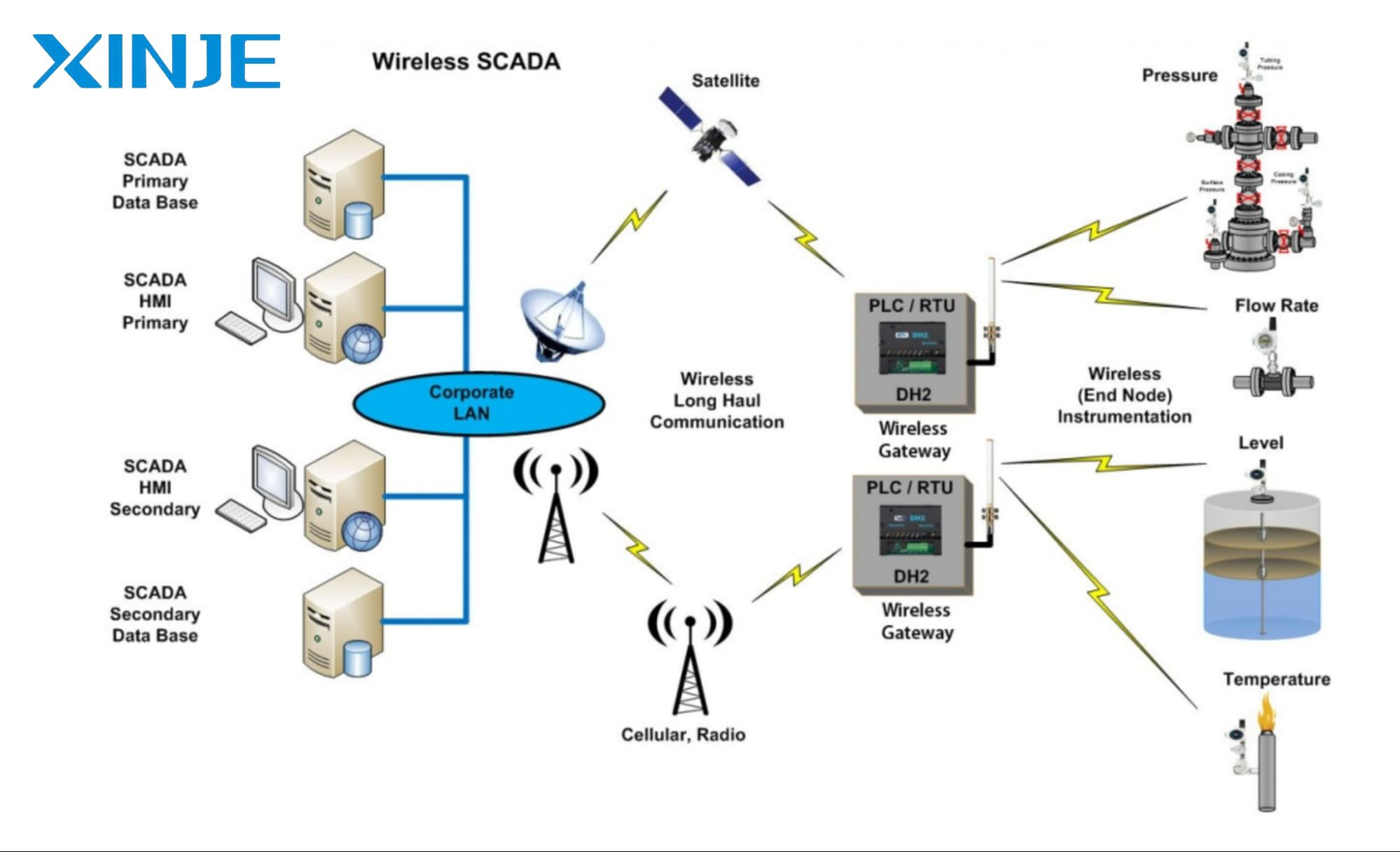
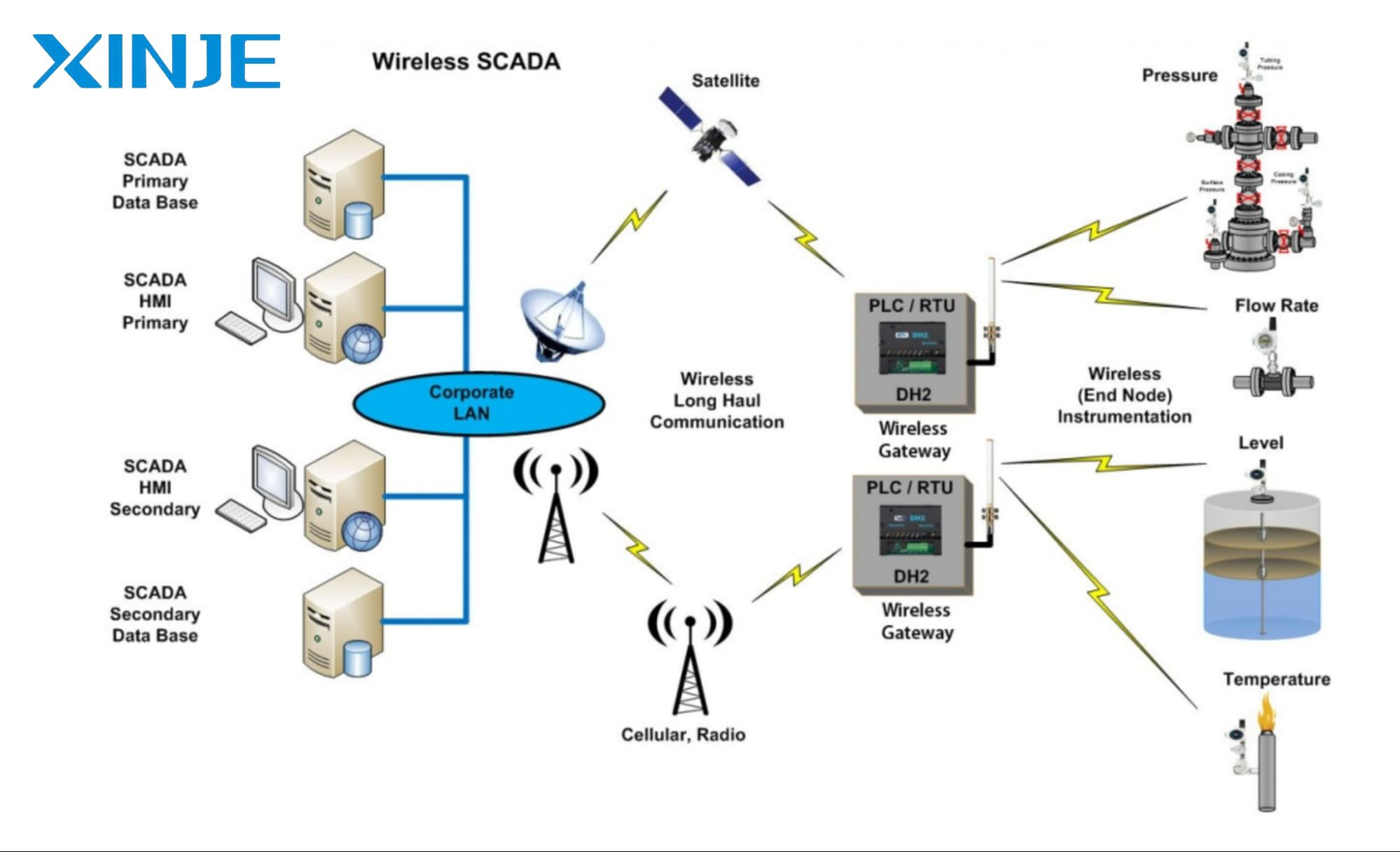
The primary function of SCADA is to provide centralized control and monitoring of distributed industrial equipment and processes. Whether in water treatment plants, manufacturing lines, or energy distribution networks, SCADA ensures:
- Real-time data collection from sensors, PLCs, and field devices
- Data visualization via operator-facing HMIs
- Remote control and automation of industrial equipment
- Alarming and event logging for system failures or threshold violations
- Data logging and historical trend analysis to optimize performance
SCADA transforms complex, distributed operations into intuitive, easy-to-manage systems, allowing operators to monitor everything from a centralized interface.
What types of SCADA are there?
Over the years, SCADA systems have evolved to match the growing complexity and scale of industrial applications. There are three main types of SCADA systems:
Monolithic
Also known as a standalone SCADA, this was the earliest form of SCADA developed in the 1960s and 1970s. These systems used mainframe computers and had no networking capabilities. Key features of monolithic SCADA include:
- Standalone operation
- No external connectivity
- High security but limited scalability
Distributed
As networking technology advanced, distributed SCADA systems emerged. They were built with multiple interconnected stations, each handling specific tasks. Features of distributed SCADA include:
- Connection over LAN (Local Area Network)
- Use of multiple servers and remote terminals
- More flexible and redundant
- Easier to maintain and expand
Distributed SCADA became popular in the 1980s and 1990s and is still common in many plants today.
Networked
The latest generation of SCADA, SCADA Network, leverages the internet, cloud computing, and wireless communications to enable real-time monitoring and control from anywhere. Key features include:
- Remote access via web or mobile devices
- Integration with IoT, MES, and ERP systems
- Cloud-based storage and analytics
- Advanced cybersecurity features
Modern SCADA is ideal for multi-site operations and supports data-driven automation on a global scale.
How does SCADA work?
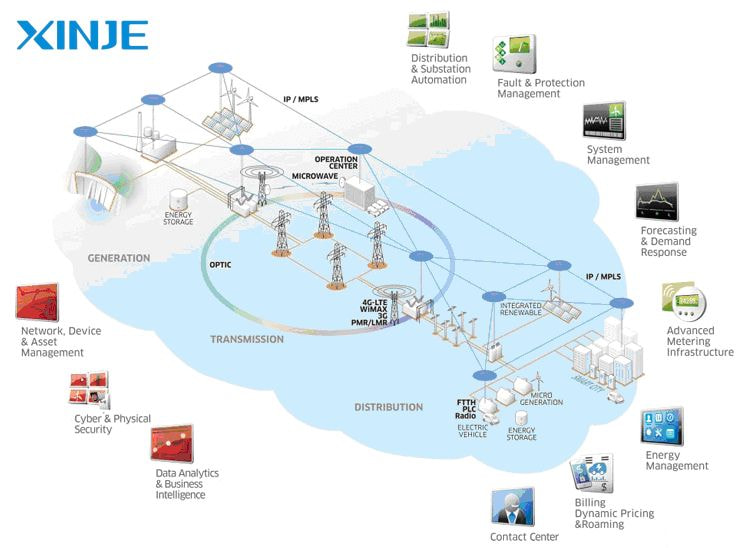
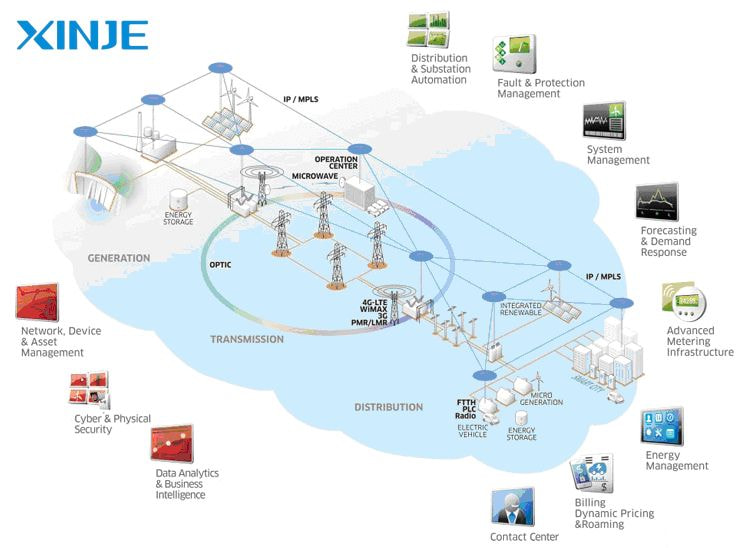
Understanding how SCADA works helps illustrate its role in automation. A typical SCADA system consists of four core components:
- Field Devices (Sensors & Actuators): These devices collect real-time data such as temperature, pressure, flow, etc., and execute commands such as opening a valve or starting a motor.
- Remote Terminal Units (RTUs) or PLCs: These are connected to the field devices and transmit data to central SCADA servers. PLCs (Programmable Logic Controllers) are widely used for local control tasks.
- HMI – Human Machine Interface: This is the user interface where operators monitor processes, receive alarms, and interact with the system.
- SCADA Master Station: This server gathers all the field data, processes it, stores it, and displays it to operators via HMI interfaces.
Through this architecture, SCADA provides visibility, control, and historical analysis in a cohesive system. Operators can detect anomalies, respond quickly to alerts, and fine-tune processes for efficiency.
How to integrate SCADA and HMI?
Integrating SCADA with HMI creates a seamless control environment for industrial operators. Here’s how the integration process typically works:
- Define System Requirements: Start by mapping your industrial process, and identifying which sensors, machines, or PLCs need to be monitored or controlled.
- Choose a Compatible SCADA and HMI Platform: Make sure your SCADA software is compatible with the PLC protocols in use and that the HMI can communicate effectively with both the SCADA server and field devices.
- Set up Communication Protocols: Set up communication using industrial protocols. OPC UA (Open Platform Communications Unified Architecture) is commonly used for secure, standardized data exchange between SCADA and HMI systems.
- Configuring HMI Displays and Controls: Design intuitive HMI displays that reflect the actual physical process. This includes real-time graphics, control buttons, alarm windows, and trend charts.
- Integration Testing and Validation: Conduct rigorous system tests to ensure that the HMI accurately reflects real-time data and that SCADA commands are correctly executed by field devices.
Successful integration allows operators to monitor live processes, control operations, and respond to problems from a single screen, improving safety, productivity, and response times.
What is the difference between OT and SCADA?
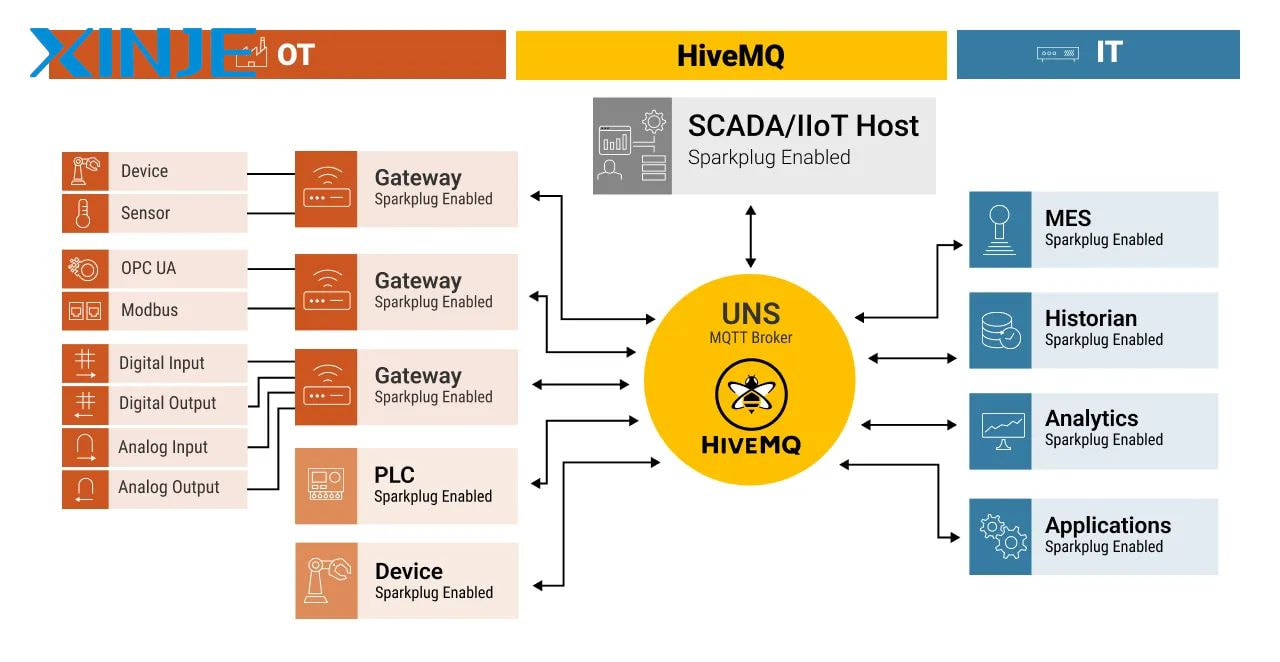
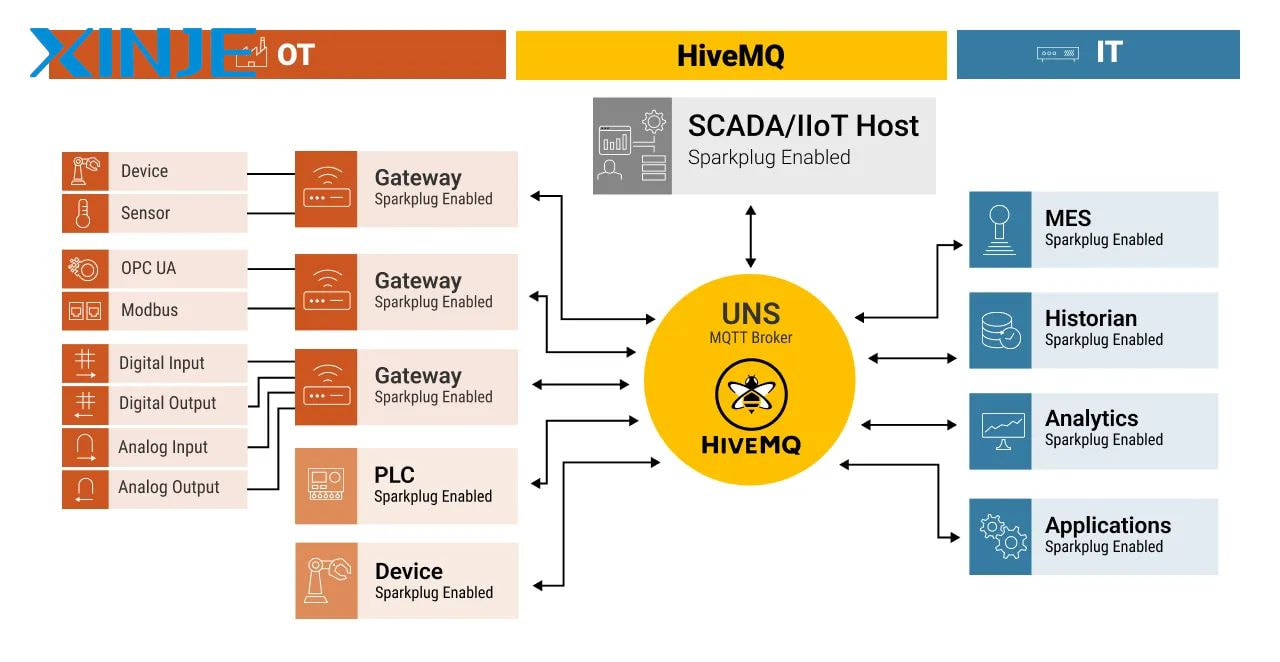
Operational Technology (OT) is often confused with SCADA, but they represent different areas of industrial systems. Some typical characteristics of these two types of systems that users should pay attention to are as follows:
SCADA | OT | |
Definition | Software system for monitoring and control | Hardware and software used to detect, monitor, and control physical devices |
Function | Supervisory control, data acquisition, and visualization | Includes SCADA, PLCs, HMIs, sensors, etc. |
Focus | Centralized monitoring and control | Entire operational ecosystem |
Example | SCADA software visualizing plant operations | Network of PLCs, drives, and HMIs managing a factory |
In essence, SCADA is a subset of OT. OT encompasses all the components used to run industrial operations, including SCADA, HMI, robotics, and more. Understanding this distinction is critical to convergence, combining enterprise systems with real-time operations to make smarter decisions.
Conclusion
SCADA Integration is no longer optional. It’s a necessity for industries aiming to stay competitive, efficient, and safe. From legacy monolithic systems to modern cloud-based architectures, SCADA systems are at the heart of industrial digital transformation.
By integrating SCADA with HMI platforms, operators gain centralized visibility, remote control, real-time analytics, and faster response to process anomalies. As industries evolve towards Industry 4.0, the combination of SCADA and HMI becomes a powerful tool to improve operational efficiency and reduce downtime.