In industrial automation, Closed-loop Controller is an important solution to maintain the stability and accuracy of the production process. By using feedback from sensors to adjust operations, this system not only helps optimize performance but also minimize errors and improve product quality. So how does Closed-loop Controller work, what are the benefits and differences between Open-loop Controller? Let’s find out the details with XINJE in the article below!
What is a Closed-loop Controller?
A Closed-loop Controller is a control system in which the output of the system is monitored and responded to to automatically adjust the process to achieve a desired value.
This system uses feedback from the sensor to compare with the desired value (setpoint) and adjusts the input to reduce errors, ensuring that the output is always stable and accurate, even when there is noise or change from the environment.
What is the operating principle of a Closed-loop Controller?
The closed-loop control process can be divided into 5 main steps:
Step 1: Set the desired value (Setpoint – SP)
The user or the system sets the desired output value, which is the output value that the system needs to achieve
Step 2: Measure the actual value (Process Variable – PV)
The sensor measures the actual output of the system and sends the data to the controller.
Step 3: Compare and calculate the error (Error – E = SP – PV)
The controller takes the desired value (SP) minus the actual value (PV) to calculate the error. If the error ≠ 0, the controller will adjust the system to reduce the error to 0.
Step 4: Adjust the input (Control Output – CO)
The controller sends a control signal to the actuator to change the system input.
Depending on the type of control, it can increase/decrease the input energy, expand/contract the control valve, or change the open/close state of the system
Step 5: Repeat continuously in real time
The above process is repeated continuously at high speed to ensure the system maintains the desired value. As soon as there is a change from the environment or load, the controller will react immediately to keep the system stable.
Practical example: Automatic air conditioning system
- The user sets the temperature to 25°C (Setpoint).
- The temperature sensor measures 27°C (Process Variable).
- The controller detects errors (+2°C), and increases cooling capacity.
- When the temperature drops to 25°C, the controller maintains a stable state.
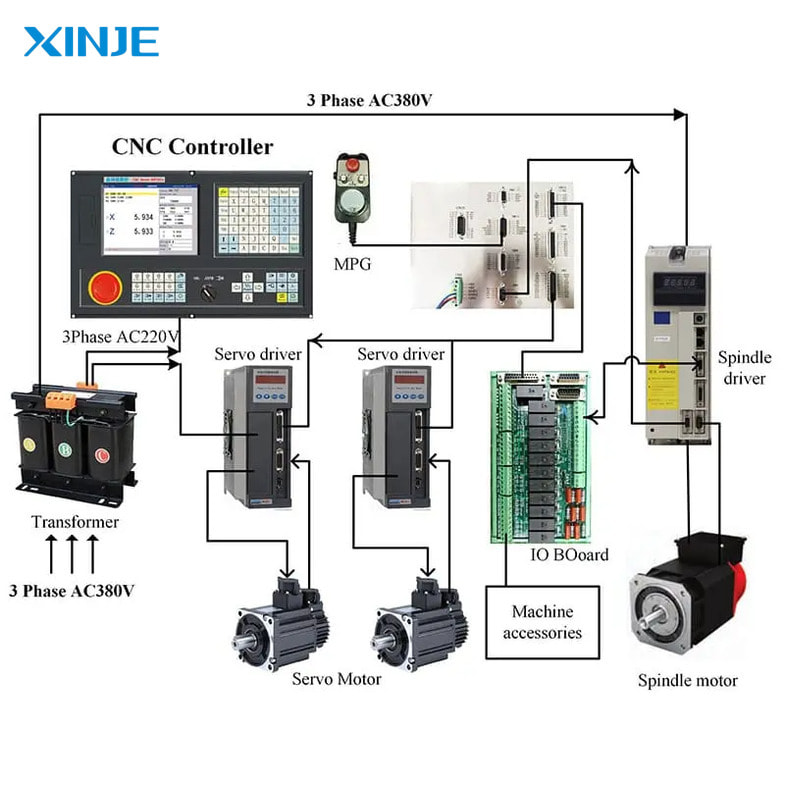
What is the difference between Closed-loop Controller and Open-loop Controller?
Features | Open-loop Controller | Closed-loop Controller |
Control mechanism | No feedback, fixed value control. | With feedback, continuous adjustment to maintain desired value. |
Response to environmental disturbances | No self-adjustment when there is disturbance or change from the environment. | Automatically adjusts to compensate for errors when there is disturbance. |
Accuracy | Low, easily affected by changes in the system. | High, accurately maintains desired value. |
Complexity | Simple, easy to design and operate. | More complex due to additional sensors and feedback controllers. |
Cost | Varies from $500 – $1000. Lower due to no feedback sensors. | Varies from $1000 – $2000. Higher due to additional sensors and signal processors. |
Response speed | No real-time feedback. | With fast feedback, making the system more stable. |
Applications | Electric fans, washing machines, fixed conveyors. | Automatic air conditioning, motor speed control, industrial robots. |
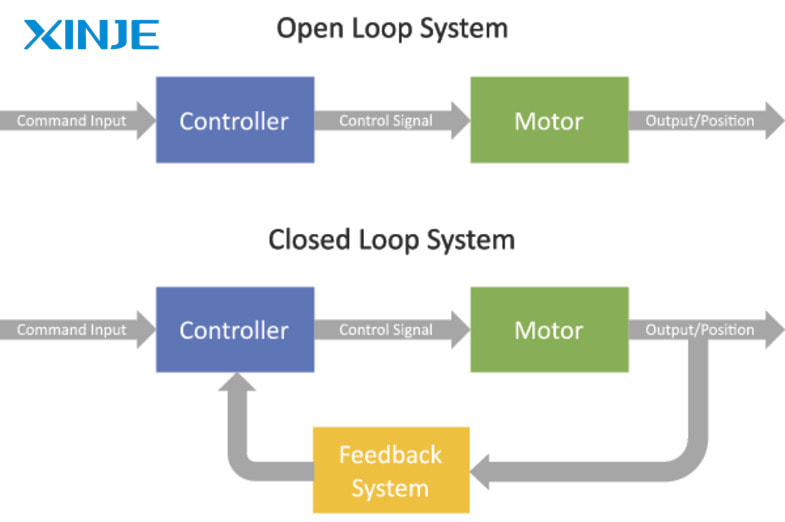
Advantages of Closed-loop Controller
- High accuracy: The Closed-loop system has the ability to automatically adjust to ensure that the output always matches the desired value. Operational errors are significantly reduced thanks to continuous feedback from the sensor.
- Automatically compensate for errors and stabilize the system: When there is an environmental disturbance or load change, the Closed-loop system can adjust the input to maintain a balanced state. This helps to prevent the system from operating unstable or deviating from the desired value.
- Energy saving: The system only consumes energy according to actual needs, not operating excessively like the Open-loop Controller. Helps to optimize operating costs in industries.
- Improved equipment life: Minimizing vibration and harsh operating conditions helps protect machinery, reduce wear and tear, and extend equipment life.
- Flexible applications: Can be used in many industries such as temperature control, motor speed, industrial robots, autonomous cars, etc.
Closed-loop Controller systems are especially important in industries requiring high precision such as electronic component manufacturing, factory automation, robot control and medical applications.
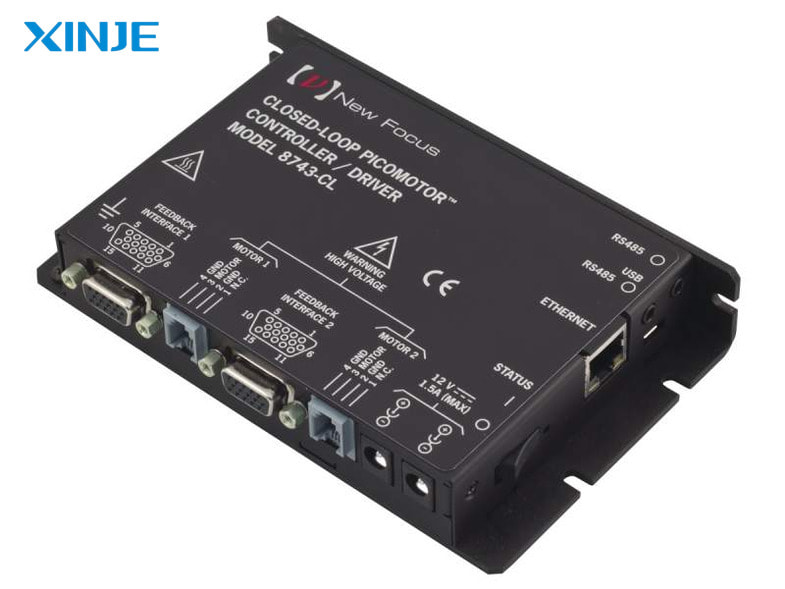
Disadvantages of Closed-loop Controller
- High investment cost: Due to the requirement of additional devices such as feedback sensors, controllers, processing software, Closed-loop systems are more expensive than Open-loop.
- Complex in design, installation and maintenance: The system needs to be programmed in detail to ensure accurate feedback and avoid unwanted fluctuations. Requires highly skilled engineers to install and optimize the control algorithm.
- Requires regular monitoring: To ensure stable system operation, sensors need to be checked and calibrated periodically. In environments with many noise factors (dust, humidity, temperature changes), sensors can be distorted, leading to inaccurate control.
- Response delay may occur: In some systems, the time it takes to process signals and adjust inputs can create lag, reducing performance. If the control algorithm is not properly tuned, the system may oscillate or fail to achieve the desired value.
Closed-loop controllers are ideal for systems that require high precision and self-tuning capabilities. However, investment costs and operational complexity are factors to consider before implementation.
Conclusion
Closed-loop Controller systems play an important role in modern automation, helping to improve accuracy, optimize performance and ensure the stability of production processes.
Thanks to the ability to continuously respond, this system not only improves product quality but also minimizes energy and resource waste.
In the context of increasingly developing industry, the application of Closed-loop Controller will be an inevitable trend, helping businesses improve their competitiveness and optimize operations effectively.