In the industrial automation industry, understanding technical terms is key to optimizing production processes and improving work efficiency. Grasping basic concepts will help you work more effectively in a high-tech environment where change and improvement are constant. In this article, XINJE will introduce 10 important terms you need to know in industrial automation.
Automation
Automation is the process of using technology, equipment and systems to automatically perform tasks that previously required human intervention.
Industrial automation helps reduce errors, increase productivity and reduce production costs. Common applications of automation include automated production lines, industrial robots and intelligent control systems.
The benefits of automation go beyond improving work efficiency, to also improving accuracy and flexibility in production.
Programmable Logic Controller – PLC
PLC (Programmable Logic Controller) is an important device in industrial automation, used to control and monitor manufacturing processes. PLCs can be programmed to perform logic tasks, such as turning equipment on and off, controlling motors, and processing signals from sensors.
PLCs are especially useful in manufacturing plants, where processes need to be controlled continuously and automatically. Using PLCs reduces human dependence and increases stability in production.
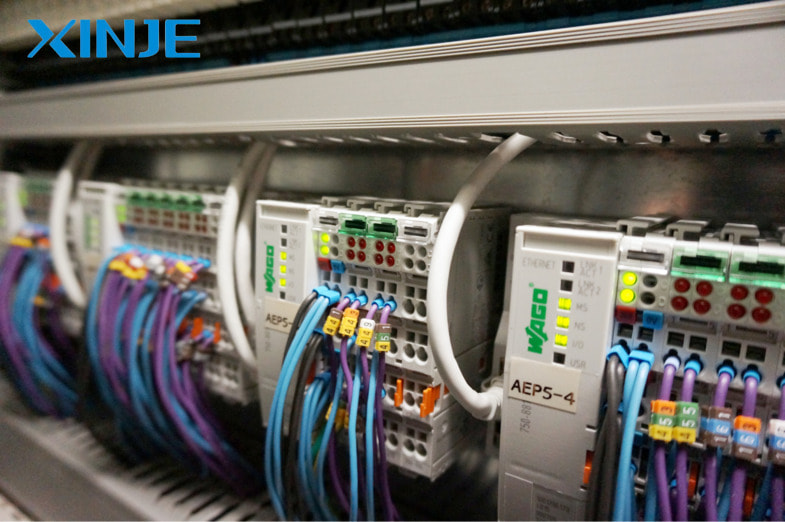
Distributed Control System – DCS
A DCS system is a distributed control system, used to manage and monitor complex industrial processes. DCS differs from PLCs in that it is designed to control large-scale systems, such as chemical plants, power plants, or large-scale manufacturing systems.
DCS helps divide the control and monitoring work into small parts, each part can operate independently, but all are connected together through a network system. This helps reduce the load on the central controller and improve the stability of the entire system.
Supervisory Control and Data Acquisition – SCADA
SCADA is a supervisory control and data acquisition system, used to monitor and control processes remotely. SCADA allows managers to monitor the status of systems, detect problems, and adjust automated equipment without having to be physically present on site.
With SCADA, large manufacturing and infrastructure systems such as power plants, water systems, or distribution networks can be managed more efficiently, minimizing risks and optimizing performance.
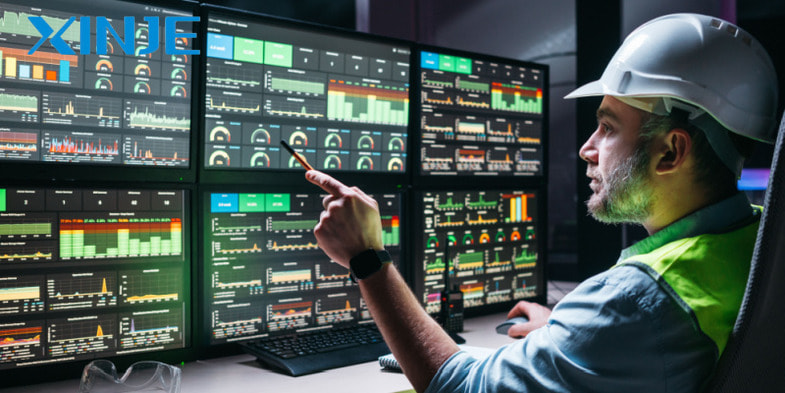
Industrial Robots
Industrial robots are automated devices that can perform tasks such as welding, assembling, or quality control in a manufacturing environment. These robots can operate independently or in coordination with other devices in an automation system.
Thanks to their ability to work accurately and continuously, industrial robots help increase productivity, reduce errors, and improve safety in the work environment. Common applications of robots in manufacturing include automating assembly, product inspection, and packaging.
Automation Control Systems
Automated control systems are the brains of automated manufacturing processes. These systems can use simple logic controllers (ON/OFF) or more complex control systems such as PID (Proportional-Integral-Derivative) to regulate factors such as temperature, pressure, and flow rate during the manufacturing process.
Automated control systems help minimize human intervention, improving accuracy and consistency in the final product.
Industrial Internet of Things -IIoT
IIoT (Industrial Internet of Things) is a concept that describes the connection of devices, sensors, and machines in a network to collect, analyze, and share data. IIoT provides remote monitoring and control capabilities, helping to improve efficiency and reduce downtime in the manufacturing process.
For example, IIoT sensors can help monitor the health of machinery and alert technicians when problems arise, allowing technicians to intervene in a timely manner and prevent catastrophic failure.
Variable Frequency Drive – VFD
A VFD (Variable Frequency Drive) is a device that controls the speed of an electric motor by adjusting the frequency of the electrical current supplied to the motor. VFDs save energy and improve motor efficiency in variable speed applications, such as pumps, fans, and compressors.
By using VFDs, plants can reduce energy consumption, extend motor life, and improve overall system efficiency.
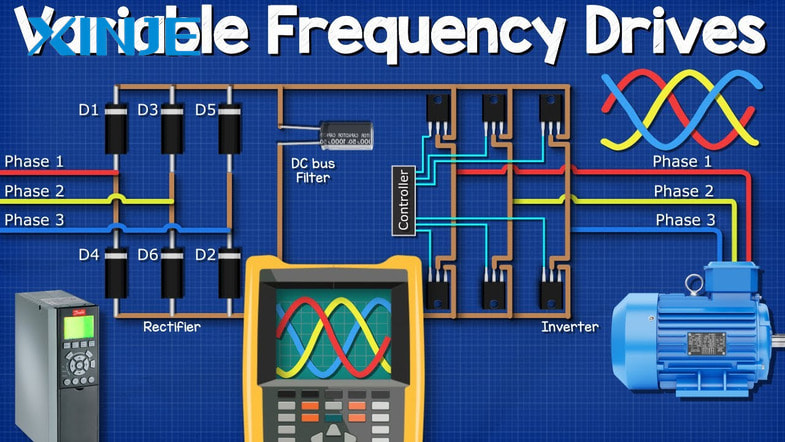
Human-Machine Interface – HMI
HMI (Human-Machine Interface) is a tool that helps humans interact with automation systems. This interface provides an intuitive way for operators to monitor and control equipment and machines in the production line.
HMI helps improve operational capabilities, reduce human error, and provide important information about the status of equipment in real time. HMI devices can be touch screens, control panels, or software interfaces on computers.
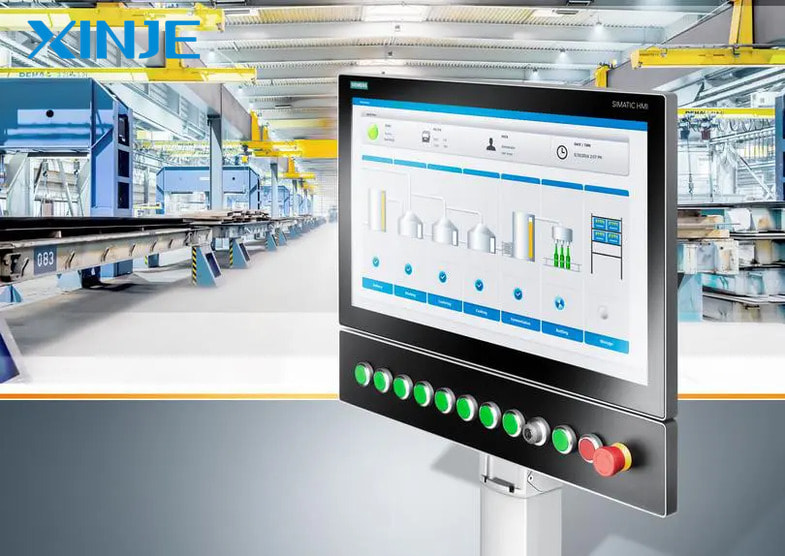
Transducer
A transducer is a device that converts signals from one form to another, such as converting temperature to an electrical signal or converting pressure to an electrical signal. Transducers play an important role in measuring and controlling parameters in the manufacturing process.
For example, a temperature transducer can convert the temperature measured from a sensor into an electrical signal that the control system can understand and process.
Conclusion
Understanding and correctly applying industrial automation terminology is an important factor in improving work efficiency and enhancing the ability to control complex production processes. Hopefully, this article has helped you gain a clearer view of the basic terminology in the automation industry. Continue to learn and update new technologies so as not to fall behind in Industry 4.0.