In the era of Industry 4.0, the application of PLC (Programmable Logic Controller) to automation systems has become a standard in most industries. The central processing unit (CPU) plays the role of the “brain” that controls the entire operation of the system. Let’s explore the CPU in detail as well as its role in optimizing the production process.
History of CPU in PLC industry
In the field of PLC, CPUs were developed in parallel with the birth of PLC in 1968 by Modicon (now part of Schneider Electric). Initially, PLC CPUs only performed simple tasks such as replacing mechanical relays. However, with the development of microprocessor technology, CPUs in PLCs have become increasingly powerful, capable of processing data faster, supporting multiple communication protocols, and ensuring high reliability in harsh industrial environments.
The continuous advancement of CPUs has contributed significantly to promoting industrial automation, bringing production lines and factories into the intelligent era.
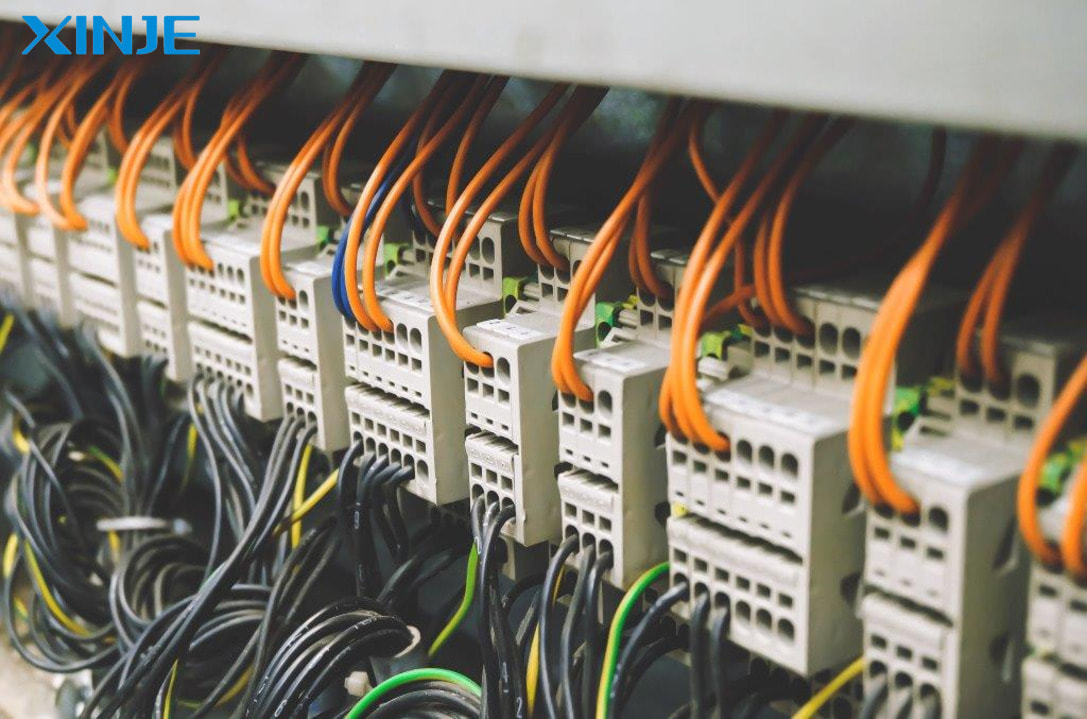
What is CPU?
The CPU is the central component of the PLC, responsible for processing data, performing logic algorithms, and coordinating the operations of other modules in the system. When receiving input signals, the CPU analyzes and processes information according to a pre-programmed program and then sends control signals to the outputs.
The CPU is considered the heart and brain of the PLC because it monitors the entire system, ensuring that all operations take place according to the correct procedure. It not only helps process data but also plays an important role in detecting and handling system errors.
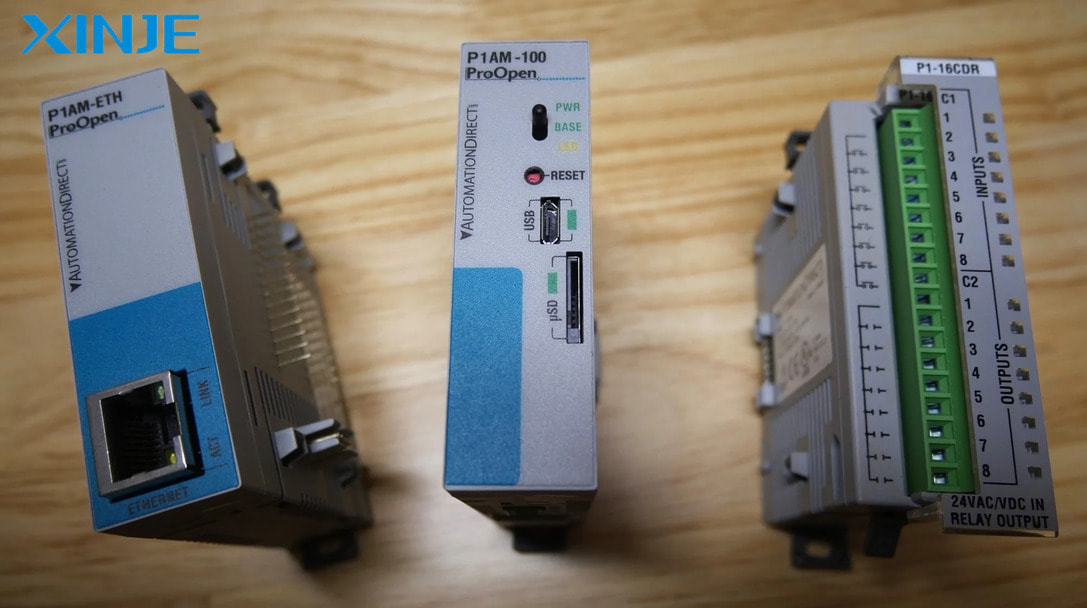
How many parts does a CPU consist of?
The CPU consists of the following 3 main components: Processor, Memory, and Communication Interface:
- Processor: This is where all the calculation and logic processing takes place. The microprocessor performs logical operations, controls the flow of data, and makes decisions based on the programmed program. The speed of the microprocessor determines the performance and response time of the PLC.
- Memory: Memory is an important component of the CPU, where programs, data and system status information are stored. Memory is divided into three main types:
ROM (Read-Only Memory): Stores PLC firmware – core programs needed for the system to operate.
RAM (Random Access Memory): Stores temporary data while the CPU is processing. Data in RAM will be lost when the power is turned off.
EEPROM/Flash Memory: Stores user-programmed programs, helping to protect data even when the power is lost.
- Communication Interface: The CPU needs to communicate with other devices in the system such as SCADA, HMI, or expansion modules through communication ports such as Ethernet, Modbus, Profibus. These interfaces allow the CPU to receive input data and send control information to the output.
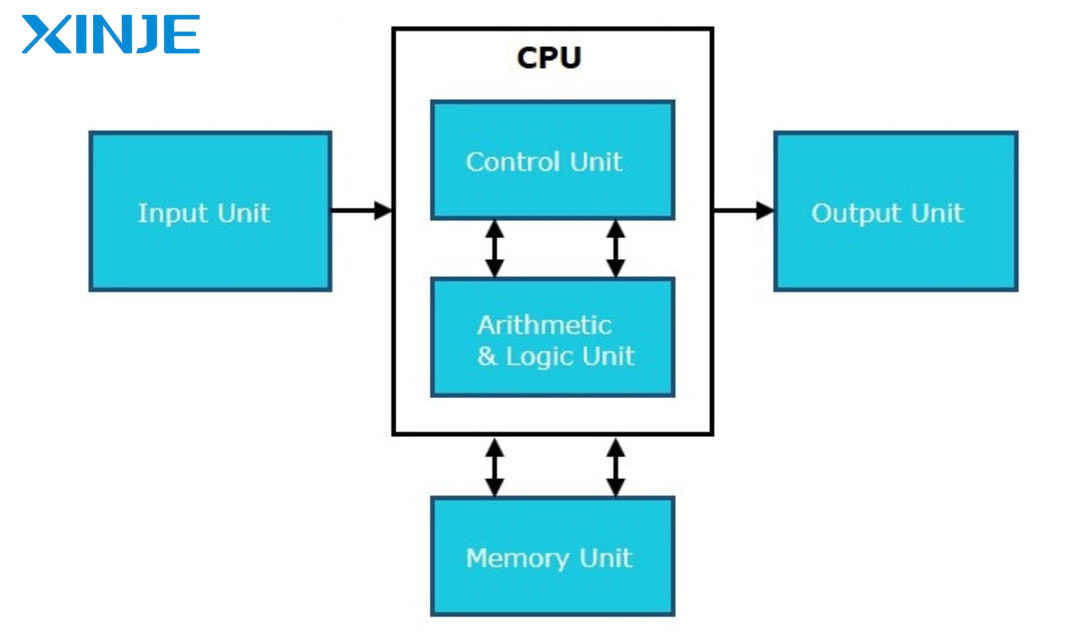
Main functions of CPU in PLC
CPU in PLC plays a central role, ensuring that the entire system operates accurately and efficiently. To perform the task of “running a process”, the CPU must complete a series of closely linked tasks:
- Communicate with the programming machine and download the program connects to the programming machine (laptop or PC) to receive the control program. During this process, the CPU downloads the instructions from the programming machine and stores them in memory for execution.
- Backplane I/O Data Transfer: The CPU manages the data transfer between input/output modules via the backplane. This is an internal connection in the PLC that ensures that data moves quickly and accurately between components.
- Read and update Input Registers: The CPU scans the status of all input signals from sensors or switches and stores them in the input registers. This information is then used to calculate the control logic.
- Logic Execution: The CPU processes each line of code in the program in order, performing arithmetic and logic operations to determine what action to take. This is an important step for the CPU to convert input data into control instructions.
- Updating the Output Registers: After processing the logic, the CPU updates the output register, which contains control instructions to send to devices such as motors, valves, or indicator lights. These instructions are transmitted to the output modules for execution.
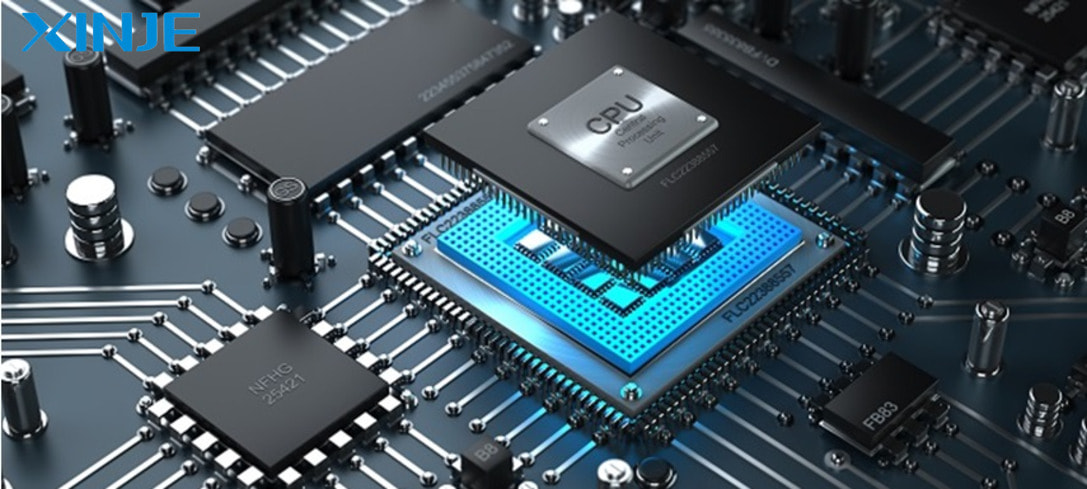
What are the important things to consider when choosing a CPU?
Choosing the right CPU not only ensures the system operates efficiently but also saves costs and increases operational reliability. Here are 5 things you need to consider before choosing a CPU for your PLC system:
- Suitable communication protocol: For systems that use laptops for programming, make sure the CPU is compatible with the communication protocol of the programming device.
- Memory capacity: The CPU’s memory must be large enough to store the entire control program as well as the necessary data. For small production processes, a CPU with less than 100 MB of memory is usually sufficient. However, to be sure, you should discuss directly with the manufacturer or supplier to make the right choice based on the specific requirements of the system.
- Number of Input/Output: Each CPU is designed to support a certain number of I/O points. If the system has more devices than the CPU can support, choose a CPU that supports I/O module expansion.
- Brand: Choose CPUs from reputable manufacturers such as Siemens, Rockwell Automation, Mitsubishi, Schneider Electric.
- Cost: Consider the cost of purchasing the CPU and related costs such as expansion modules, programming software, and maintenance. Prices range from $2000 – $3000.
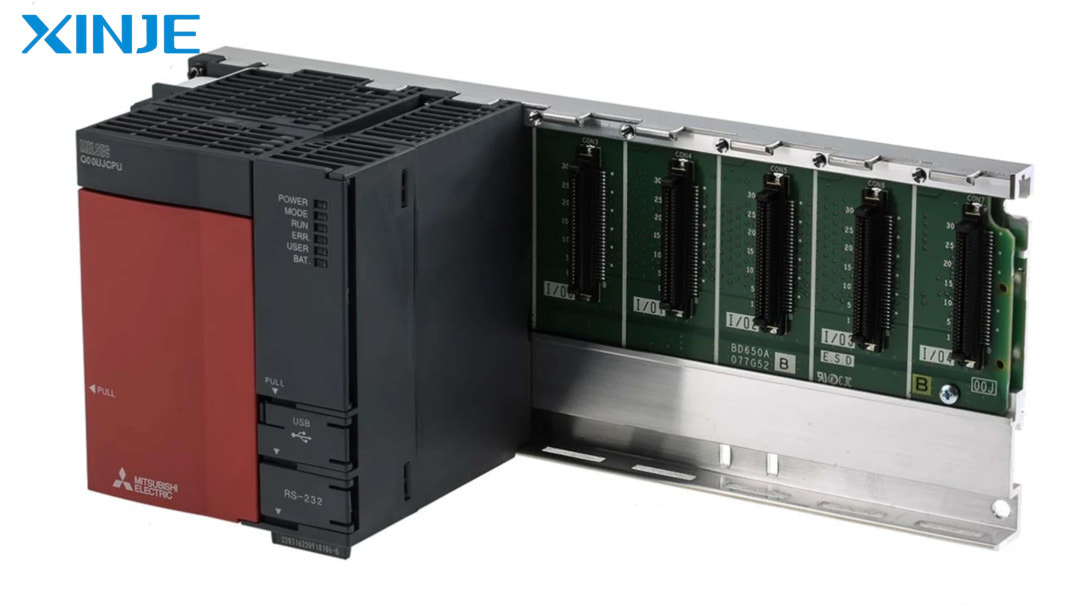
Conclusion
The Central Processing Unit (CPU) plays a key role in every PLC system, ensuring that the control and monitoring of automation processes are accurate and efficient. With the continuous development of technology, CPUs are becoming more intelligent and powerful, bringing many outstanding benefits to industries.