The PID (Proportional, Integral, Derivative) controller is a popular control algorithm that plays an important role in industrial control systems. They are widely used and applied to maintain variables in the system such as temperature, pressure, flow or speed at a stable and accurate level.
What is the PID Controller?PID operates based on three main components: proportional, integral, and derivative. These help adjust the output to keep the system as close to the desired value as possible. With its simplicity and high performance, PID is widely used in many automation control systems.
In this article, we will help you get the most general overview of PID, how it works, its advantages/disadvantages, and the typical differences between the two PLC and PID controllers.
H2 What is the PID (Proportional-Integral-Derivative) Controller?
The PID controller is considered a basic component in industrial control systems, where P is Proportional, I is Integral and D is Derivative. It is an essential component to achieve precise control of temperature, pressure, and speed in the production line.
In PLC (Programmable Logic Controller), the PID controller plays an important role, as it is capable of maintaining the stability and accuracy of the process, adjusting the output based on real-time error values. Therefore, it can be ensured that the process is always under control with high accuracy.
How does a PID Controller operate?
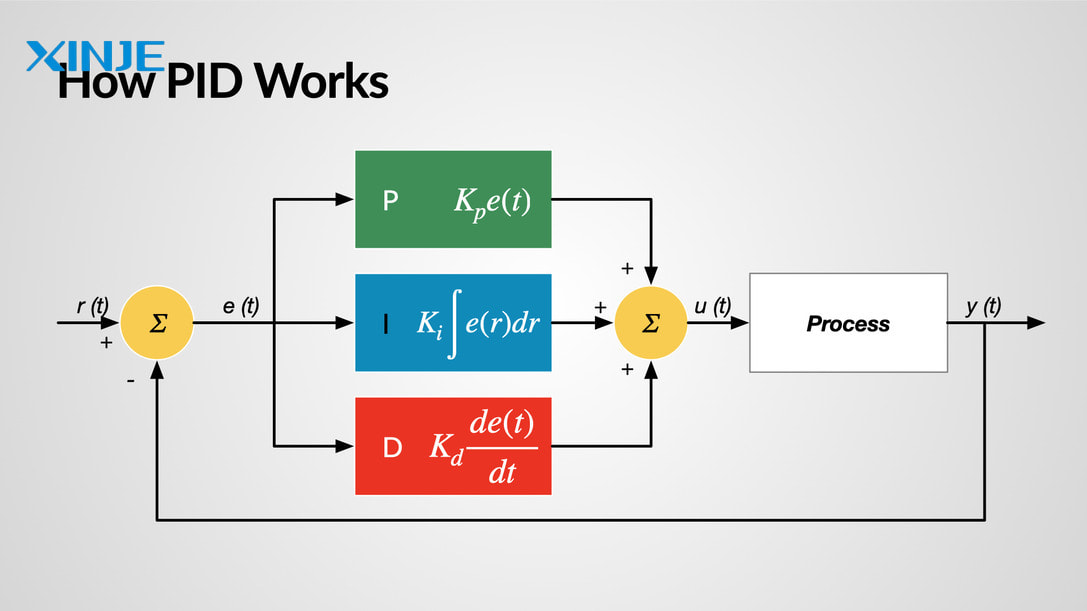
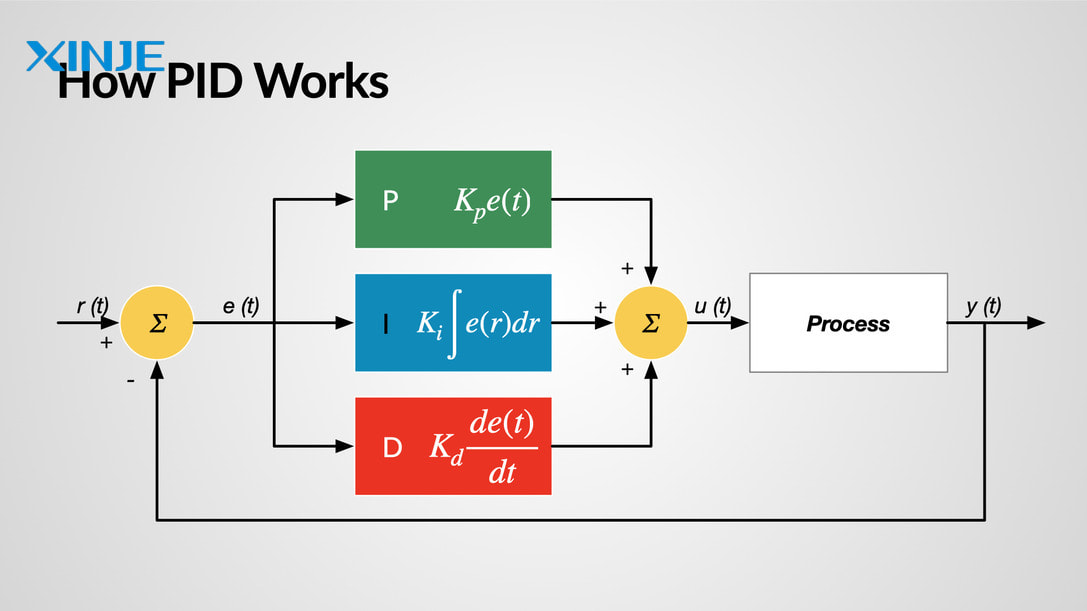
How does a PID controller work? A PID (Proportional, Integral, Derivative) controller works to strike a delicate balance of responsiveness and stability to ensure seamless system performance.
Each component has a different role: for example, the Proportional component monitors and immediately corrects any deviations from the desired set point. Next comes the Integral component, which nurtures and ensures the system returns to equilibrium. Finally, the Derivative component anticipates potential changes to maintain stability and minimize potential disruptions.
These three elements working together efficiently contribute to a smoother process
How to troubleshoot PID controller issues?
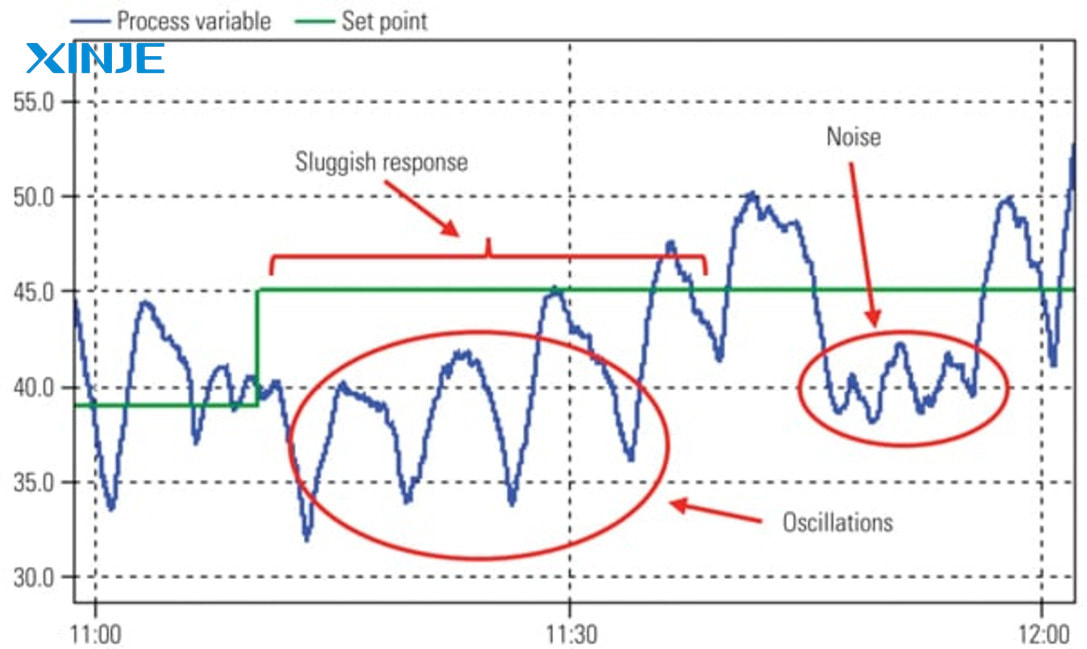
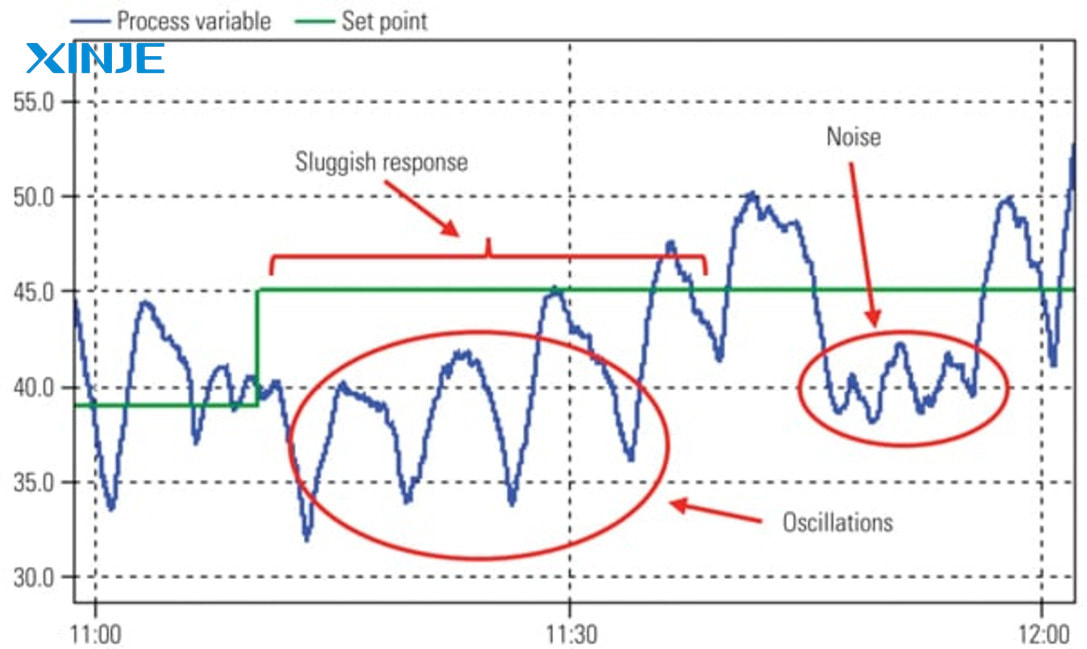
To solve the problem of the PID controller, it is necessary to go through 3 steps: Identify the problem, adjust the parameters, test, and confirm.
- Identify the problem: You need to identify the problem with your PID controller. What is it like? Is it over-tuned, slow, or inaccurate? You need to apply several methods to recognize the core of the problem, from there you will determine where the problem lies and start to deal with it.
- Adjust the parameters: The second step is important in optimizing the system performance which is throughput tuning. There are various tuning methods you can refer to such as Ziegler-Nichols, Cohen-Coon, and other optimization algorithms. It is important to balance between performance, as well as process stability to ensure that your system operates efficiently.
- Test and confirm: Finally, test and validate, monitor performance metrics such as error rates, control signals, frequencies, and stability margins, and compare them to initial expectations, which is critical to achieving efficiency in your system.
What are the advantages and disadvantages of PID Controllers?
Like other controllers, the PID controller also has certain advantages and disadvantages as follows:
Advantages |
Disadvantages |
Simplicity, broad applicability | Taking a long time to adjust |
Energy-saving | Prone to noise and measurement errors |
Affordable, and cost-effective. | Difficulties with nonlinear system calculations |
Significantly extends the life of communication equipment | Failure to properly tune the algorithm may cause system failure. |
What are the key differences between PLC and PID controllers?
Similar
The only similarity between PLCs and PID controllers is that both can be integrated into a larger control system to create a comprehensive and efficient manufacturing process. Both can also interact with other devices and systems through sensors, actuators, and human-machine interfaces, with the sole purpose of optimizing the manufacturing process.
Different
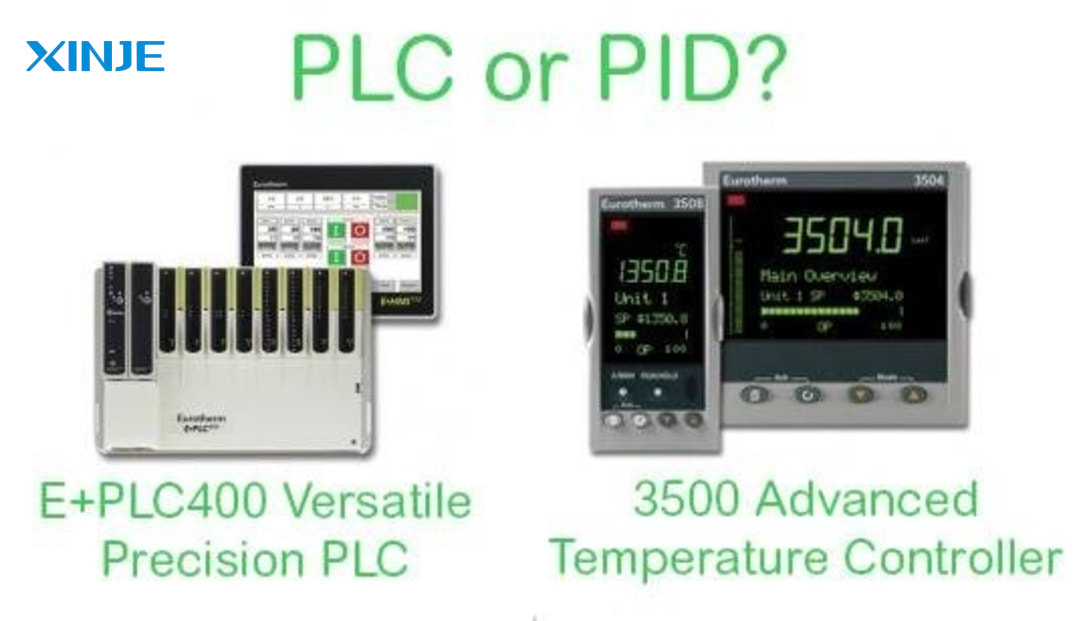
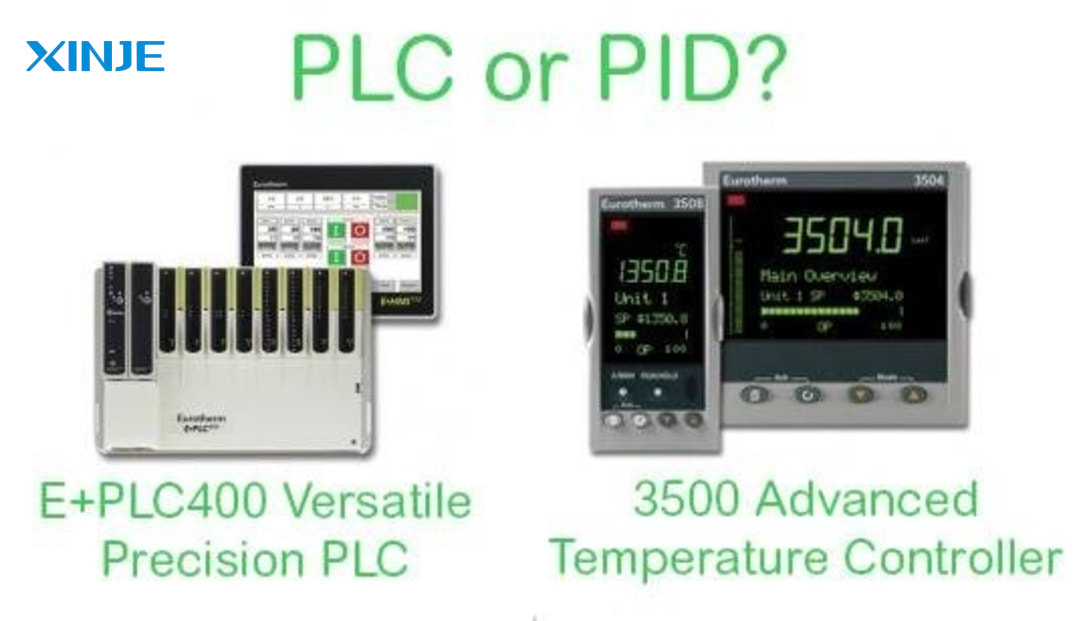
PLC | PID |
PLCs are appropriate for discrete process control | PID controllers are proper for controlling continuous variables |
Adaptable and used in many variety of applications | Designed for specific control tasks. |
Suitable for high-speed operating applications such as production lines, assembly lines, and material handling systems | Provides precise and stable control of continuous variables, suitable for heating, cooling, and mixing applications |
PLCs have fast response times and high accuracy, which are very suitable for industrial processes | PIDs are accurate and stable, suitable for processes where variables can have a significant impact on the quality of the completed item. |