In automation systems, HMI (Human Machine Interface) plays a key role, helping operators monitor and control machines easily. However, after a period of use, dust, vibration or temperature changes can cause the touch screen to deviate from the touch point, directly affecting the accuracy of the operation. So what is Touch Calibration, when to calibrate and why is it so important? Let’s find out the details in this article!
What is Touch Calibration?
Touch Calibration is the process of recalibrating the touch point on the HMI screen so that the touch position matches the display accurately. This process helps the screen receive commands at the correct position of the operator’s finger, avoiding coordinate deviation, ensuring that machine control operations take place accurately and safely.
After a period of operation in the factory environment – often with dust, vibration, and temperature changes – the HMI screen can lose touch point accuracy.
Periodic touch calibration helps prevent operating errors, ensures that all control commands are received correctly, and avoids unnecessary incidents that affect the entire production line.
When is Touch Calibration needed for HMI?
Signs that the HMI needs touch calibration
- During operation, if you see that the touch operations do not match the icon position on the screen or have to press multiple times to receive the command, it is a clear sign that the HMI has deviated from the touch point.
- In addition, if the HMI interface responds slowly, dead zones appear, or the operating coordinates are off, you should perform Touch Calibration immediately to avoid unexpected operating errors.
Impact of the production environment (dust, vibration, temperature) on touch sensitivity
- These factors can cause the sensor position to shift, causing the touch point to no longer match the actual display. Therefore, manufacturing enterprises need to maintain a clean working environment and periodically calibrate the touch to maintain stable HMI performance.
Periodic inspection cycle for HMI
- Experts recommend periodic inspection and Touch Calibration for HMI — usually every 3 to 6 months, depending on the production environment and operating frequency.
- For lines operating 24/7, the inspection schedule should be shortened to promptly detect and correct touch point deviation.
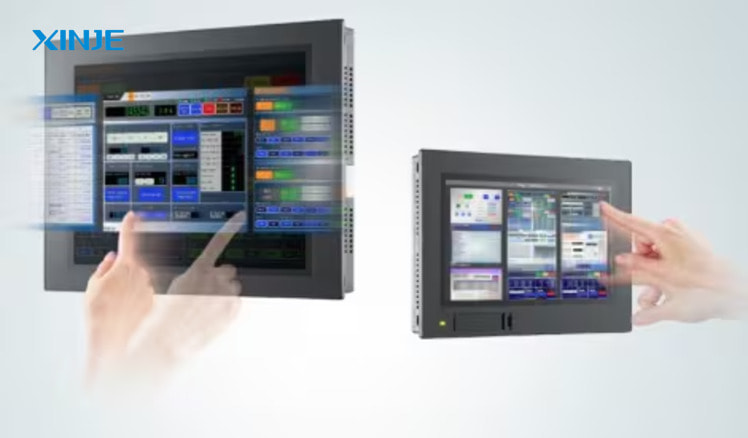
What are the basic steps to calibrate Touch Calibration for HMI?
Touch Calibration is not complicated but must follow the correct procedure:
- Preparation: Turn off the related machinery, clean the screen surface, make sure the screen is dry and free of obstacles.
- Operation: Start Calibration mode according to the HMI manufacturer’s instructions, accurately touch the marking points that appear on the screen.
- Check: After calibration, try to manipulate the icons to make sure the touch points match and are no longer off.
During the calibration process, it is necessary to ensure that the machine is not operating or the automatic functions are paused to avoid the risk of unintended startup. Technicians should wear anti-static gloves and operate gently to avoid scratching or damaging the touch screen.
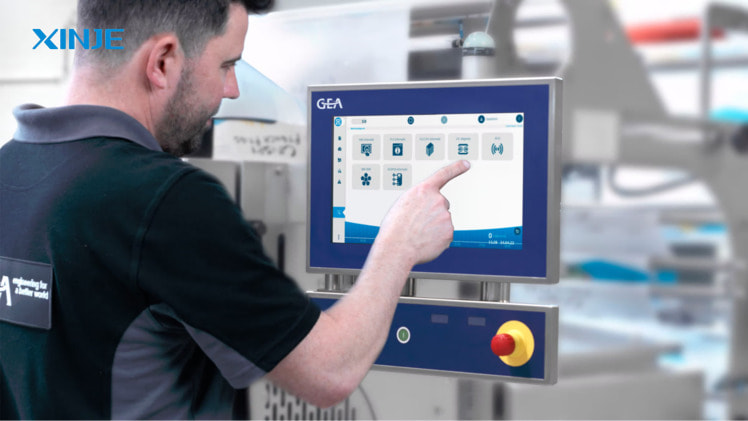
What are the benefits of periodic touch calibration?
Regular Touch Calibration brings many practical values, especially important in automated production environments:
- Ensure operational accuracy: When the touch points are properly aligned, all operations of the technician or worker match the position of the command button, icon or control area on the HMI.
- Increase the life of the HMI screen: A misaligned touch screen will cause the user to touch harder or perform the operation many times to receive the command. Regular calibration helps limit this situation, prolonging the life of the device.
- Maintain stable operating performance: Performing Touch Calibration helps maintain stability, limit production interruptions, and ensure continuous operation of the line – especially important for factories operating 24/7.
- Save maintenance and repair costs: When the HMI is periodically calibrated, touch point misalignment errors or potential damage are detected and corrected early. Thanks to that, businesses avoid the cost of replacing new screens or stopping the line for unexpected repairs.
- Improving labor safety: A precise HMI screen helps operators perform the correct commands and operations. This reduces the risk of starting the wrong device, avoiding the risk of work accidents or machine damage.
What are some common errors when calibrating Touch Calibration in HMI?
Although the Touch Calibration process is quite simple, in actual operation, many businesses still encounter common errors that cause the HMI screen to not operate as stably as desired.
Understanding common errors and how to handle them will help technicians proactively fix them in a timely manner, avoiding interruptions to the production line.
HMI does not receive touch commands
A common error is that the HMI screen does not respond when touching at calibration points. The cause may be due to dust on the screen surface, moisture or damage to the touch layer. In this case, it is necessary to clean the screen thoroughly, check the power cord and touch connection before trying again.
Incorrect touch point after calibration
Sometimes, even after performing Touch Calibration, the touch point is still off. Common causes are incorrect calibration, not touching the correct guide points or the screen being lightly impacted causing the sensor to move.
Quick solution for failed calibration
If calibration fails several times, the technician can try to restart the HMI or perform a hard reset (if the HMI model allows it). In case the error persists, the supplier or technical team should be contacted immediately to check the hardware.
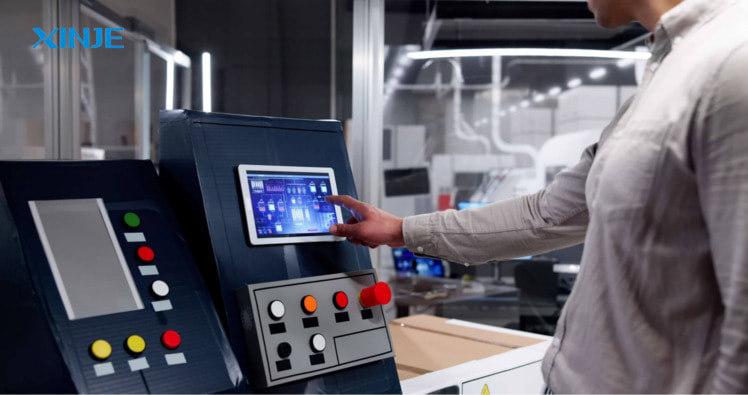
What are the things to note when choosing to buy an HMI that is easy to calibrate?
To limit the risk of sensor errors and optimize the calibration process, right from the first step of investing in equipment, businesses should consider choosing HMIs that are easy to calibrate.
- Prioritize HMIs with automatic calibration features: Some modern HMI lines are integrated with the Auto Touch Calibration feature, helping users to calibrate quickly with just a few simple steps.
- Popular HMI brands, easy to maintain: When investing in HMI, businesses should prioritize reputable brands such as Siemens, Mitsubishi, Delta, Xinje, Omron… because they often come with specialized calibration software, are easy to operate, and have easy-to-replace components.
- Technical support service from the supplier: In addition to quality equipment, technical support service is also very important. Prioritize HMI distributors with periodic maintenance policies, calibration instructions and 24/7 remote support.
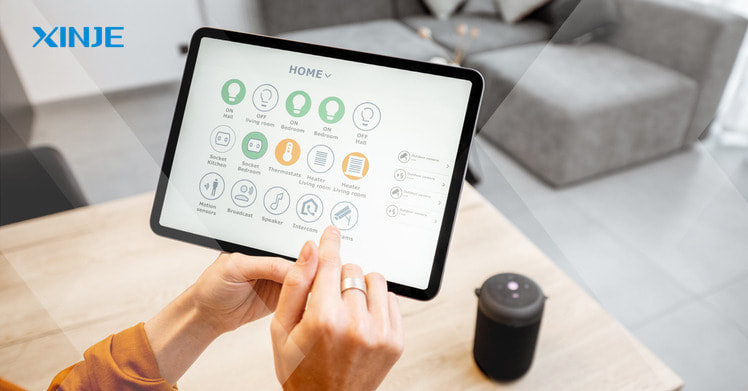
Conclusion
It can be seen that Touch Calibration plays an important role in ensuring that HMI always operates stably, receives accurate commands and maintains production line performance. Periodic touch calibration not only helps to limit operating errors but also prolongs the life of the equipment, saving unwanted repair costs.
To optimize the operation process, businesses should build a periodic inspection process, choose HMI lines that are easy to calibrate and cooperate with reputable suppliers with quick technical support services.