In the era of smart factories, Real-time Monitoring plays a key role in helping businesses manage production lines effectively, safely and cost-effectively. Combined with HMI (Human Machine Interface), Real-time Monitoring allows engineers to monitor all operating parameters instantly, from motor status, tank level, pressure to error warnings, ensuring the system operates stably and is ready to expand when needed.
What is Real-time Monitoring?
Real-time Monitoring is the process of collecting, processing and displaying production data immediately, without significant delay. In the factory, Real-time Monitoring is often deployed by combining PLC, sensors and HMI systems so that all information such as motor status, tank level, temperature, pressure, etc. are continuously updated.
Thanks to the ability to process in real time, operating parameters are always displayed visually, helping operators easily monitor, make decisions and handle errors quickly.
How does Real-time Monitoring work?
Real-time Monitoring operates based on the principle of collecting, processing and displaying data continuously, helping information to be updated immediately without significant delay.
In a typical automation system, the real-time monitoring process usually goes through 3 main steps:
Step 1: Data collection
- Field devices such as sensors, switches, meters, measuring devices collect physical values (temperature, pressure, tank level, motor speed, relay status, etc.).
- This raw data is sent to the PLC (Programmable Logic Controller) or central controller via electrical signals, analog or digital signals.
Step 2: Data processing
- The PLC receives the data, performs calculations, comparisons, and control logic to output the output signal.
- Here, pre-defined Tags will store the data values (for example: ON/OFF status, pressure level, overheat warning, etc.).
Step 3: Display and instant feedback
- HMI (Human Machine Interface) receives data from the PLC via communication protocols such as Modbus, Ethernet, Profibus.
- Tag values are synchronized with graphic objects on the HMI such as gauges, indicator lights, trend graphs.
- Operators can visually observe machine status, easily make decisions and perform control operations if necessary.
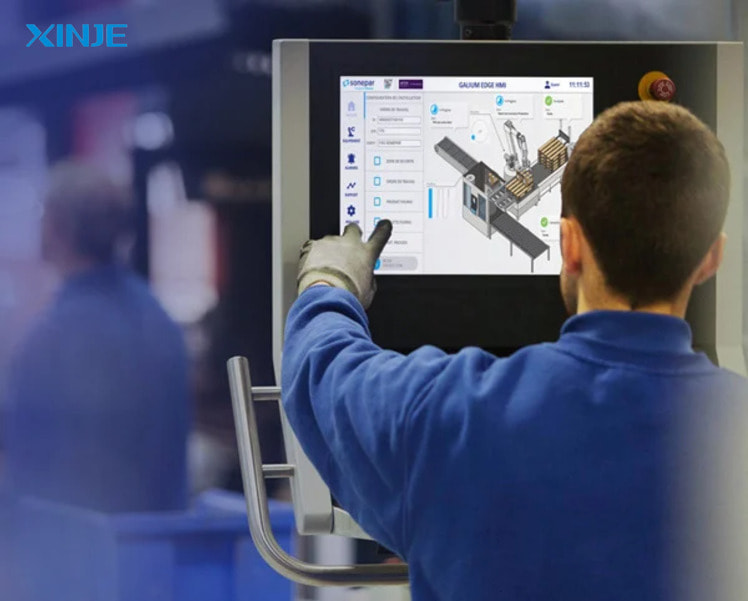
What is the relationship between Real-time Monitoring and HMI?
In automated factories, HMI (Human Machine Interface) is the most intuitive “window” to perform Real-time Monitoring. HMI plays the role of:
- Displaying all real-time monitoring data collected by PLC and sensors.
- Allowing operators to monitor indicators such as tank level, pressure, temperature, motor speed, relay status, etc. immediately.
- Thanks to the HMI Tag system, data from the PLC is quickly transmitted to the HMI and assigned to display objects such as gauges, indicator lights, level gauges, trend graphs.
When there is an abnormality, the HMI will trigger an Alarm or display a warning on the spot, helping the operator take timely action to avoid unwanted machine shutdowns.
In other words, Real-time Monitoring will not be able to maximize its value without HMI, because this is a data visualization tool, turning dry numbers into easy-to-understand, easy-to-operate information.
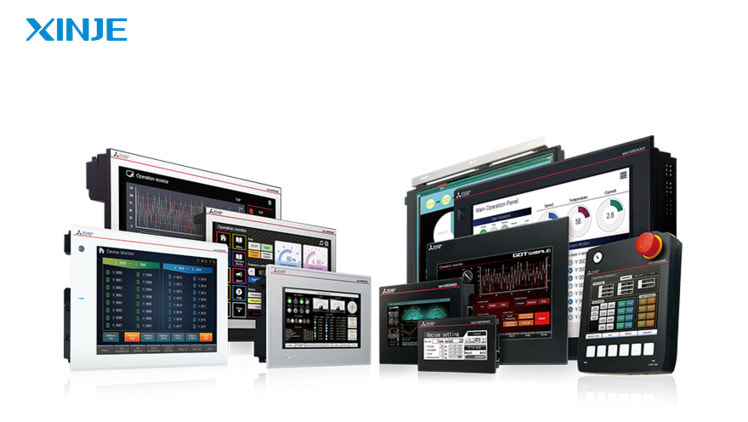
What are the benefits of Real-time Monitoring via HMI?
When deployed well, Real-time Monitoring via HMI brings many practical benefits to the factory:
- Monitor anytime, anywhere: HMI connects to LAN, Internet, allowing engineers to manage and control remotely, without having to be present directly at the machine.
- Detect errors in time, minimize risks: Abnormal warnings are displayed immediately by HMI. This helps prevent problems from spreading, reducing machine downtime and repair costs.
- Optimize operational performance: Real-time data monitoring helps engineers quickly make appropriate adjustments, keeping the production line stable.
- Integrated reporting and tracing: HMI can store historical data in parallel with Real-time display, serving production inspection, productivity analysis and predictive maintenance planning.
- Save manpower & monitoring time: With Real-time Monitoring, businesses do not need to spend labor on continuous manual inspection, reducing the risk of human error.
Notes when designing Real-time Monitoring on HMI?
For the Real-time Monitoring system to operate stably and maximize its value, you need to note some points when designing HMI:
- Identify the correct data to monitor: Not all signals need to be displayed in Real-time. Priority should be given to important variables that directly affect safety and performance.
- Choose the right HMI hardware: HMI needs to have a strong enough processing speed, suitable memory, support stable communication protocols such as Modbus, Ethernet, Profibus, etc.
- Design an intuitive, easy-to-understand interface: Avoid stuffing too much information. Only display what the operator needs to see immediately, clear layout, easy to operate.
- Regular testing & commissioning: Before official commissioning, it is necessary to check the data transmission speed, latency and accuracy of the Tag to avoid parameter deviation.
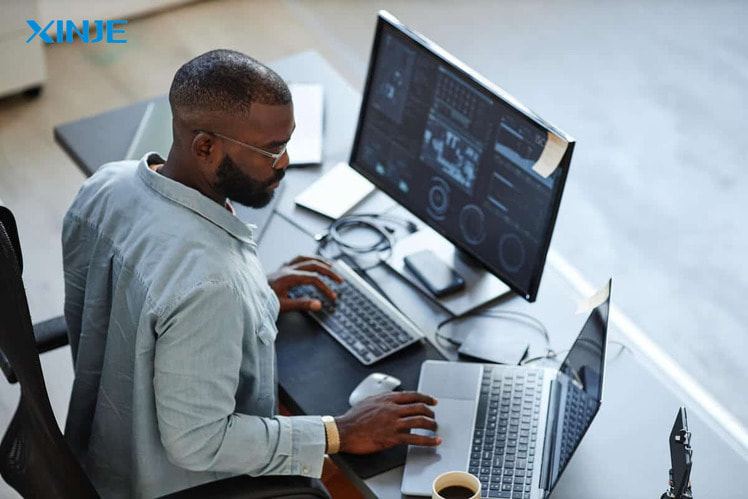
Conclusion
In modern factories and production lines, Real-time Monitoring is no longer a trend but has become a mandatory requirement to ensure continuous, safe and cost-optimized operation.
Thanks to the ability to collect, process and display data instantly through the HMI system, businesses can easily detect problems, make timely adjustments and maintain equipment performance at the highest level.
To effectively deploy Real-time Monitoring, choosing the right HMI, PLC, sensors, along with logical Tag design and intuitive interface plays a key role. This is the foundation that helps businesses minimize risks, save human resources and be ready to expand when production develops.