In modern automated factories, HMI screens play an important role as a bridge between humans and machine systems. However, during continuous operation, HMIs are prone to problems, causing disruptions to the production line if not handled promptly. The following article will help you understand what HMI troubleshooting is, common errors, standard technical troubleshooting procedures, and how to prevent problems to maintain stable and safe production operations.
What is HMI troubleshooting?
HMI troubleshooting is the process of detecting, analyzing and handling problems that occur on the human-machine interface (HMI) screen. This is an important device that connects humans and the automatic control system, so any errors that arise can directly affect the production line.
In modern automation lines, HMI plays a role in monitoring and controlling the entire process. If the HMI encounters an error and is not handled promptly, the system is easily interrupted, leading to errors, machine downtime and cost losses.
Implementing HMI troubleshooting effectively helps ensure continuous production, limit risks and maintain optimal productivity for the factory.
What are common HMI problems?
During the operation of the automation line, the HMI screen can encounter many different problems, directly affecting the ability to monitor and control the entire system. Early identification of common errors helps technicians quickly localize the cause and handle it promptly, limiting production interruptions.
- HMI screen does not display: This is the most common error, usually due to power loss, loose connection cable or frozen control software. When encountering this situation, technicians need to check the power supply, signal wire and operating status of the screen.
- Connection error between HMI and PLC: HMI and PLC are closely connected to transmit data. If the signal cable is faulty, the communication address is incorrect or the configuration is incorrect, the data is out of sync, causing the system to stop responding.
- Communication port communication error (COM, Ethernet): Ports such as RS232, RS485 or Ethernet play a role in data transmission. When the communication port is faulty, the signal is interrupted, the HMI cannot update the machine status. The cause is often due to port failure, signal interference or incorrect communication parameters.
- HMI hangs or responds slowly: HMI running continuously can lead to screen hangs, slow response. This error often comes from heavy programs, full memory or outdated control software.
- Power source, cable errors: Unstable power source, loose or broken cables can also easily cause HMI to operate unstable, suddenly shut down or not transmit data accurately.
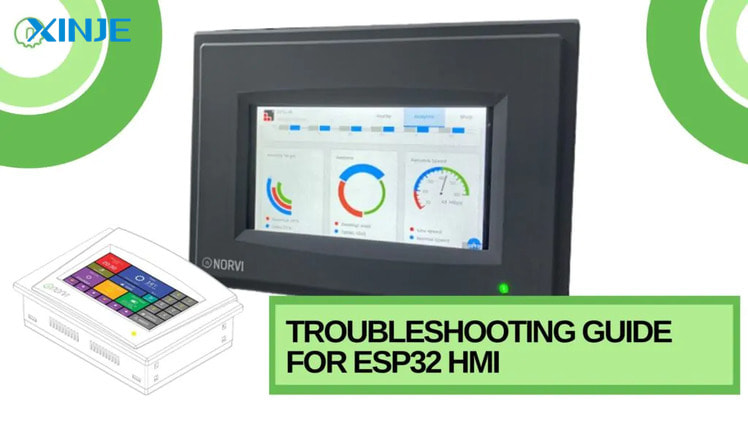
How many steps does the HMI troubleshooting process include?
To effectively handle HMI problems, technicians should follow a step-by-step process to avoid missing the cause and ensure safety during operation.
Step 1: Identify and describe the error
Record abnormal signs such as dark screen, hang, display incorrect data or lost connection. Describing the error clearly will help shorten the time to find the cause.
Step 2: Check the hardware (cable, power source, peripherals)
First, check the power supply, connection cables and related peripherals. Make sure the cable is not broken, the power supply is stable and the device is properly connected.
Step 3: Check the software (configuration, firmware, HMI program)
Next, verify the configuration settings, software version, firmware and control program. Errors caused by incorrect programming, incorrect address configuration or outdated firmware are often overlooked.
Step 4: Test system recovery
Perform an HMI reboot or restore to default settings if necessary. This is a simple way to eliminate temporary errors caused by software conflicts.
Step 5: Log, report and resolve
Finally, save the error log, the steps taken and the results of the resolution. Full logging makes it easy to handle if the problem recurs and supports long-term analysis.
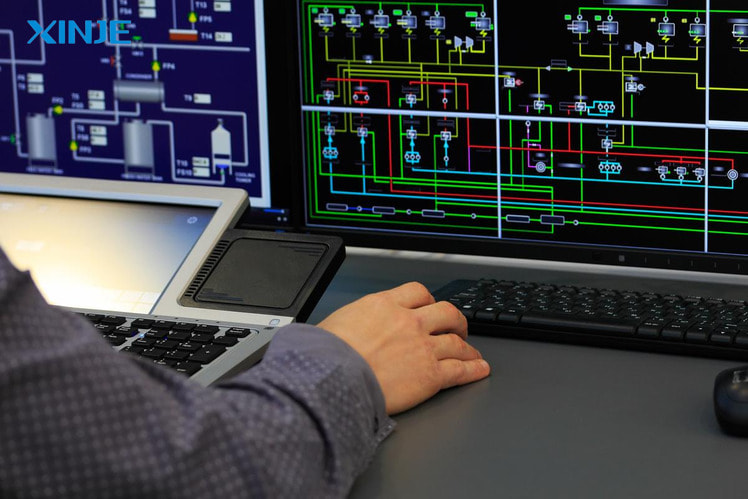
What are the notes to limit HMI incidents for businesses?
To keep the HMI system running stably and minimize the risk of interruption, businesses should apply some of the following important notes:
- Periodic maintenance: Regularly checking, cleaning and maintaining HMI equipment helps detect early signs of damage and promptly fix them before serious errors occur.
- Use quality, genuine equipment: Prioritize choosing HMI screens and accessories from reputable brands. Genuine equipment ensures durability and limits errors that may arise during operation.
- Training of operation and maintenance staff: Operators need to be fully trained in how to use, monitor and handle basic problems. The maintenance team must also have a good understanding of the system structure to be ready to respond when necessary.
- Plan HMI data backup: Periodically backing up HMI programs and data helps to quickly recover when software errors occur or replace new equipment, avoiding the time consuming task of reconfiguring from scratch.
Frequently Asked Questions (FAQ) about HMI Troubleshooting
- How often should HMI be maintained?
Depending on the level of operation of the line, HMI should be checked and maintained periodically at least every 3–6 months to detect potential errors early and ensure the life of the equipment.
- When HMI freezes, should it be handled by yourself?
For simple errors such as restarting, checking the power source, the operator can handle it himself. However, if the error repeats or is related to the internal software or hardware, it is recommended to contact a professional technician to avoid more serious damage.
- How do I know if the HMI needs to be replaced instead of repaired?
If the HMI screen is seriously damaged, the components are difficult to replace or the repair cost is more than 50% of the value of the new equipment, the business should consider replacing it to ensure long-term operating performance.
- Should HMI data be backed up?
It is recommended to periodically back up the entire configuration and control program of the HMI. This helps to recover quickly when the device has a problem, minimizing the time to reinstall from the beginning.
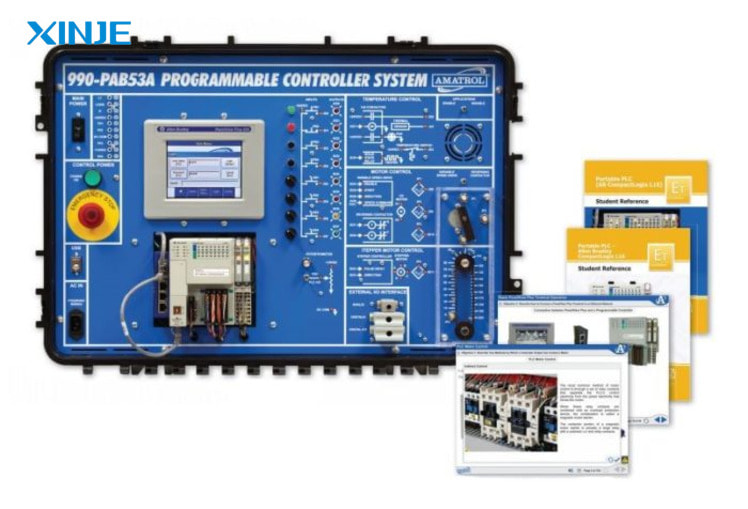
Conclusion
HMI troubleshooting plays an important role in ensuring that the automation line operates continuously, safely and efficiently. Timely detection and handling of problems not only helps to minimize downtime but also saves repair costs and maintains stable productivity.
To avoid risks and optimize performance, businesses should invest in quality equipment, perform periodic maintenance and choose a reputable technical support partner who is ready to accompany when the system has a problem.
If the business has difficulty in handling HMI problems, consider using XINJE’s professional technical support service for quick and safe diagnosis and repair, thereby maintaining the production line’s performance at the highest level.