What are the HMI Protocols? Human-machine interfaces (HMIs) play a vital role in modern industrial automation systems. But for an HMI to function effectively, it must communicate seamlessly with Programmable Logic Controllers (PLCs), sensors, and other devices. This communication occurs through HMI protocols, standardized communication rules that define how data is exchanged between devices.
Among the most widely used HMI protocols are Modbus, OPC UA, and Profibus. Each protocol has its architecture, strengths, and weaknesses, making it suitable for specific applications. This article will explore these protocols in more detail and help you understand which protocol is best suited for your automation needs.
Modbus Protocol
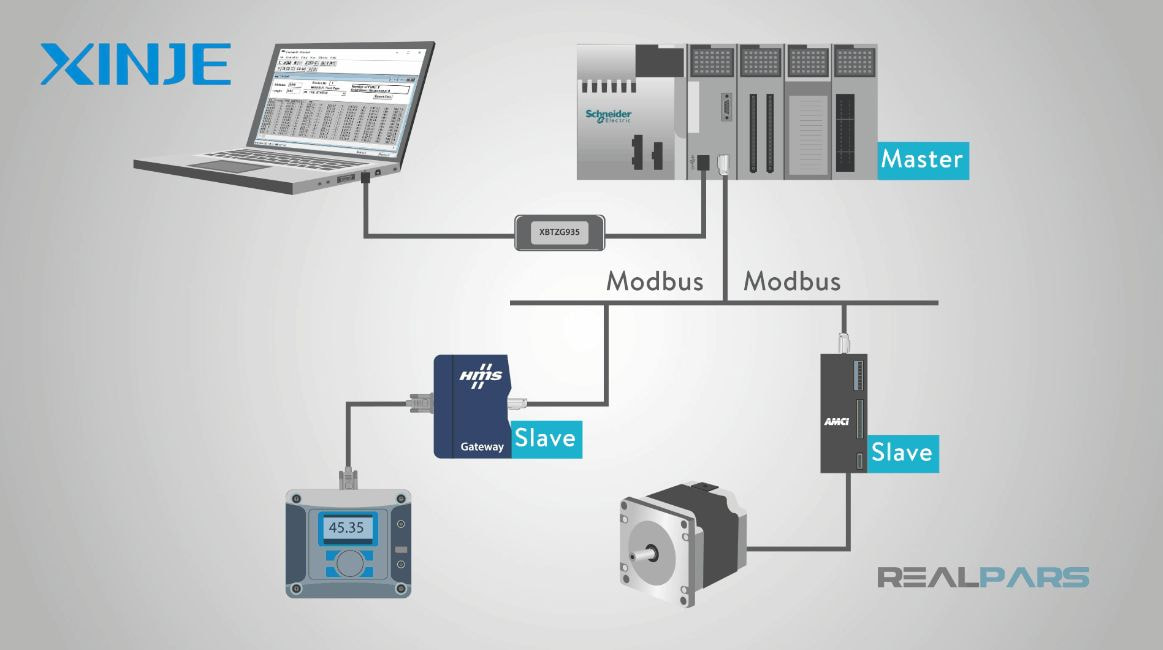
Modbus is one of the oldest industrial communication protocols introduced by Modicon in 1979. This protocol establishes communication between client/server and industrial electronic devices, mainly in automation systems.
Advantages of Modbus
- Simple configuration and easy practical implementation.
- An open standard is freely available and non-proprietary, encouraging wide and large-scale adoption.
- Flexibility: supports serial communication (Modbus RTU, Modbus ASCII) and Ethernet (Modbus TCP/IP).
- Wide compatibility: Compatible with many PLCs, HMIs, SCADA systems, and field devices.
How does the Modbus protocol work?
Modbus operates on a Master-Slave architecture. The master initiates communication by sending requests to slave devices (PLCs or sensors). Each slave responds with the requested data or an acknowledgement.
For Modbus TCP/IP, communication takes place over Ethernet, eliminating the need for dedicated serial ports and increasing communication speed and distance.
Disadvantages of Modbus
Although Modbus is very popular, it also has some limitations:
- Lack of security: It lacks built-in encryption and authentication.
- Limited data structure: Data is transmitted in simple formats, making complex data difficult to process.
- Limitation of a single Master: Traditional Modbus networks only allow for one Master device.
Profibus Protocol
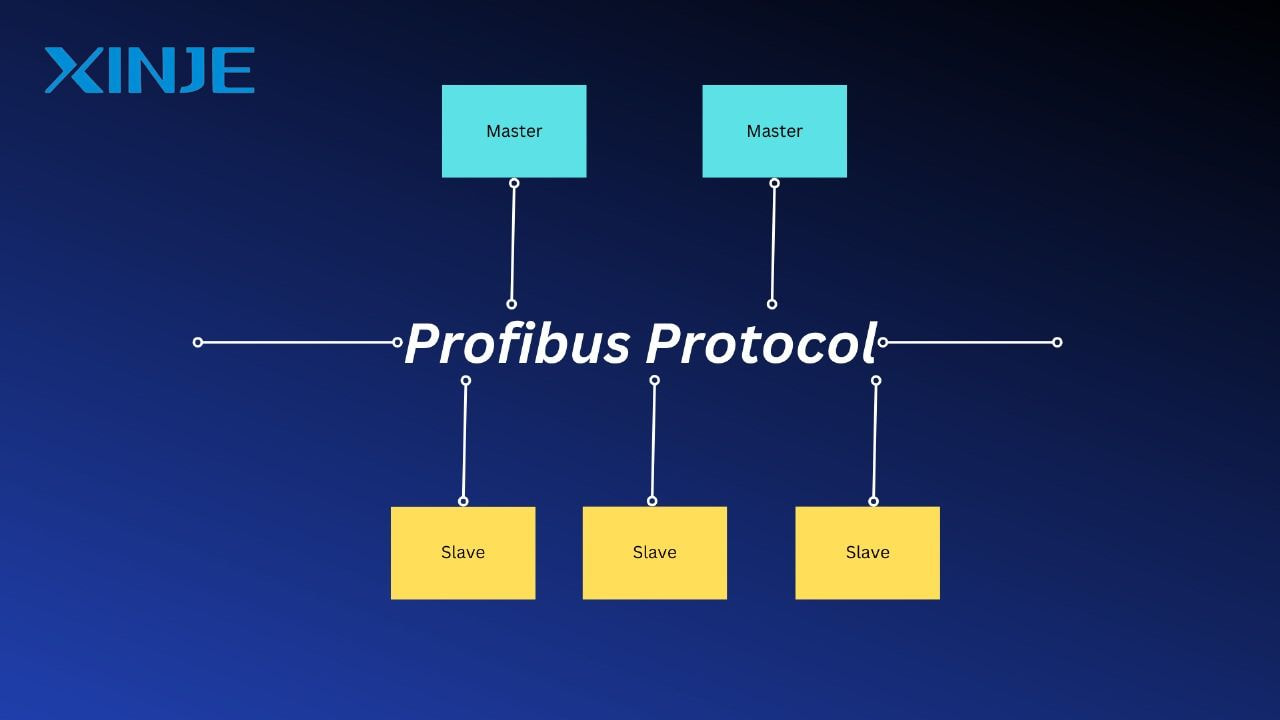
Profibus (Process Field Bus) was developed by Siemens and is widely used in Europe and Asia. This protocol provides robust performance in many industrial and automated manufacturing environments today.
Advantages of Profibus
- High speed: Supports up to 12 Mbps in Profibus DP mode
- Deterministic communication: Provides time-critical data exchange for real-time systems.
- Extensive diagnostics: Enables detailed monitoring and fault detection.
- Multi-vendor support: Supported by many manufacturers and certified through PROFIBUS & PROFINET International (PI).
How does the Profibus protocol work?
Profibus operates in a master-slave or token-passing system. There are two main types:
- Profibus DP: Used for fast data exchange with sensors and actuators.
- Profibus PA: Designed for process automation, compatible with explosion-proof environments.
In Profibus DP, the master sends cyclic data to the slave devices, while also allowing acyclic communication for diagnostics or parameterization. The protocol supports up to 126 devices on a single bus.
Disadvantages of Profibus
Despite its industrial strength, Profibus still has some disadvantages:
- Complex installation: Requires specialized cables and connectors.
- Limited flexibility: Compared to Ethernet-based protocols.
- Obsolescence risk: Increasingly replaced by Ethernet-based alternatives such as Profinet and OPC UA.
OPC UA Protocol
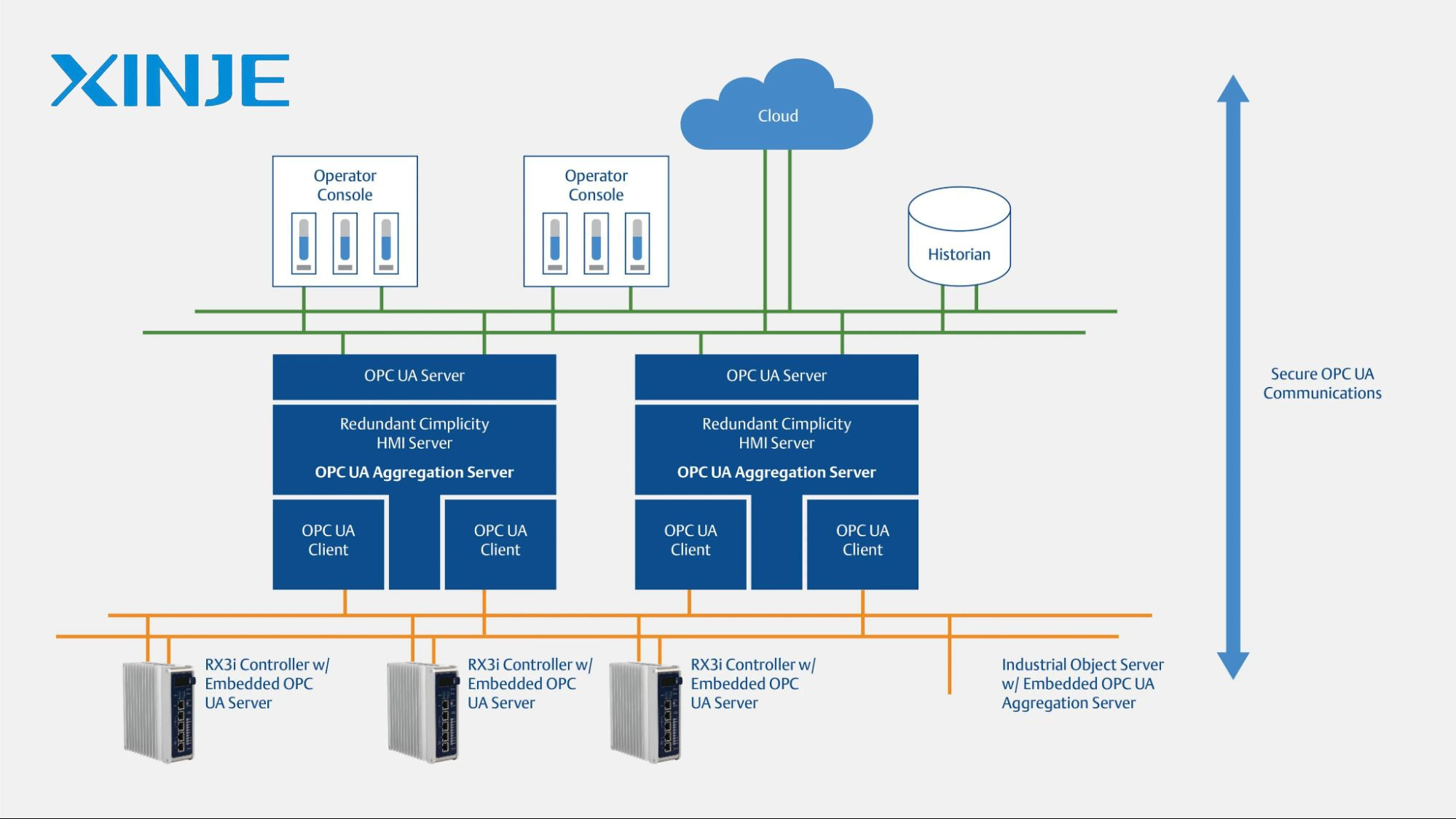
OPC UA is the next-generation protocol developed by the OPC Foundation to replace the original OPC. This can be considered as the protocol that brings many of the most modern features:
Advantages of the OPC UA protocol
- Platform independence: Works on Windows, Linux, and embedded systems.
- Strong security: Includes encryption, authentication, and user access control.
- Rich data modeling: Supports complex data types and hierarchies.
- Scalability: Suitable for small devices and large enterprise systems.
- Cloud and IIoT friendly: Ideal for modern smart factories and Industry 4.0 environments.
How does the OPC UA protocol work?
OPC UA uses a client-server architecture. The server (PLC or device) displays its data model, while the client (HMI or SCADA) browses, subscribes to, or reads the data in real time.
OPC UA communicates over:
- Binary TCP: Optimized for performance.
- HTTP/HTTPS: For firewall-friendly cloud connections.
- MQTT: For subscribe-subscribe messaging in IoT systems.
OPC UA supports both real-time data exchange and historical data logging, alarms, and events, making it an all-in-one solution for modern automation.
Disadvantages of OPC UA
Like other protocols, however superior and convenient, OPC UA can pose certain challenges that operators should be aware of:
- Higher learning curve: More complex to implement than Modbus.
- Resource-intensive: May require more CPU and memory on smaller devices.
- Network-dependent: Highly dependent on appropriate network configuration and bandwidth.
Conclusion
In short, there are many more protocols on the market than just these three, so you need to consider carefully before choosing the right HMI protocol for your automation system.
- Modbus: Best for simple, legacy systems with basic communication needs.
- Profibus: Provides high-speed, deterministic communication for factory automation, although increasingly being replaced by Ethernet-based systems.
- OPC UA: The most advanced, secure, and scalable protocol for modern smart factories and IIoT integration.
Each protocol has a specific role, and understanding its strengths and limitations can help you make informed choices. Whether you are upgrading an existing system or designing a new one, aligning your HMI protocol with your operational goals and technology stack is essential for long-term success.