For HMI to communicate stably with PLC, SCADA or other control devices, setting up the correct IP address is a step that cannot be skipped. If the IP address is set incorrectly or duplicated, the system is likely to encounter connection loss errors, interrupting the entire production line. This article will help you understand how to set up an IP address for HMI, important notes and how to handle common errors.
What is IP Address in HMI?
IP Address (Internet Protocol Address) in HMI is a unique identifier that helps HMI to “communicate” with other devices in the industrial network, such as PLC, SCADA or monitoring computer. Through IP address, devices “know” exactly where to send and receive data — ensuring control and monitoring information is transmitted correctly and promptly.
If HMI is not assigned the correct IP address, it will not be able to connect to PLC, inverter, SCADA or other network devices. Correct IP configuration helps the automation system operate stably, avoid network conflicts, and allows engineers to monitor and control remotely via computer, laptop or SCADA software.
When to set IP address for HMI?
Setting IP address for HMI is not always the same but will depend on the purpose of connection and system scale. Below are common situations where engineers need to install or adjust IP for HMI to ensure stable operation of the device.
- Connect HMI to PLC via LAN: In most automation systems, HMI and PLC are often connected to each other via industrial LAN. At this time, assigning an IP address to HMI is required for PLC to “identify” the correct device that needs to send or receive data.
- Connect HMI to SCADA or remote monitoring system: When a business deploys SCADA or remote monitoring software, HMI needs a fixed IP address so that the host computer or SCADA server can easily collect data.
- When expanding the system or changing equipment: In fact, when adding a new HMI, replacing an old HMI or expanding the production line, engineers need to reassign the IP address to ensure that all devices have separate IPs, without conflicts.
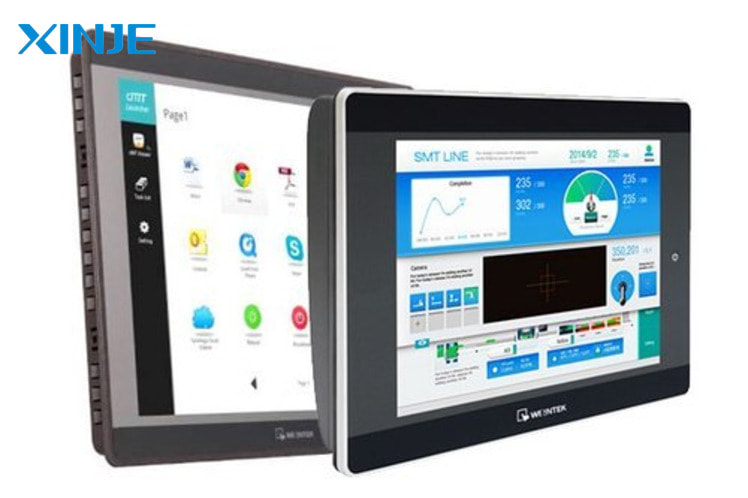
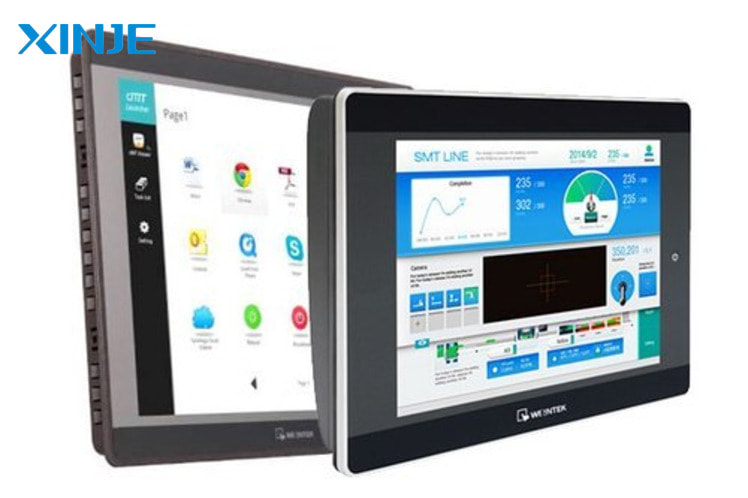
How to set up an IP address for HMI?
For HMI to be able to connect stably with PLC or SCADA, IP address setting must be done correctly. Below are 4 basic steps to set up IP for HMI quickly and accurately.
Step 1: Determine the IP address of PLC/control device
Before setting IP for HMI, you need to check the IP address of PLC, inverter or related control device. This helps ensure that HMI and PLC are in the same network range, avoiding address conflicts.
Step 2: Access HMI settings screen
Use hard keys, administrator password or configuration software to access HMI’s Network Settings. Depending on the HMI line, this item can be located directly in the System Menu or through HMI programming software on the computer.
Step 3: Enter IP address, Subnet Mask, Gateway
Enter the desired IP address for HMI, making sure it does not overlap with another device’s IP. At the same time, enter Subnet Mask and Gateway if you need to connect via router or switch. For example: PLC IP is 192.168.1.10 → HMI IP can be set to 192.168.1.20, with Subnet Mask 255.255.255.0.
Step 4: Save and check connection
After installation, save the configuration and restart HMI (if necessary). Execute the Ping command or check the connection status with the PLC to make sure the HMI has received the correct IP address and stable communication.
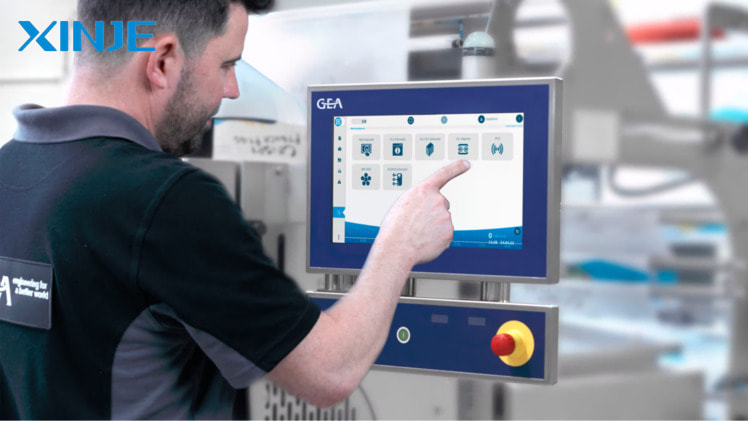
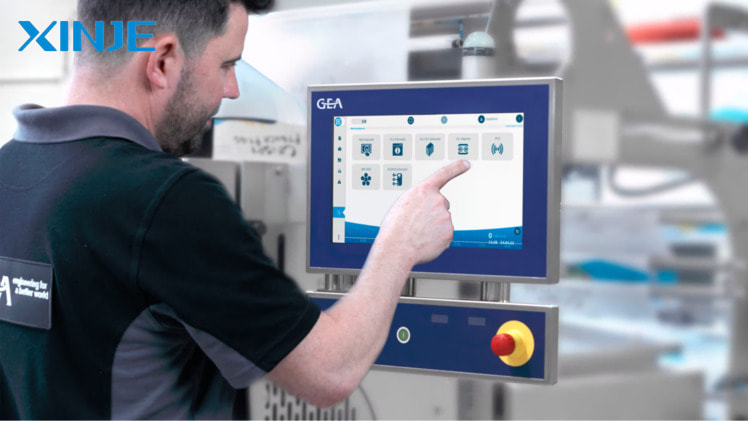
What are the important notes when setting IP for HMI?
Setting up an IP address for HMI seems simple, but if not done correctly, it can easily cause connection loss or system conflicts. Therefore, engineers need to note the important points below to ensure that HMI operates stably and safely in the automation network.
- Avoid duplicate IP addresses: Duplicate IP is the most common error that causes connection loss, network conflicts or Communication Timeout. Always check the existing IP range in the system and allocate IP according to the network management scheme.
- Set up static IP or DHCP?: With automation systems, static IP is often preferred to ensure that the HMI always keeps a fixed address, avoiding unwanted changes when restarting. Only use DHCP (dynamic IP) if the system is small and does not require permanent monitoring.
- Check the communication protocol standard: The IP address only works properly when the HMI and PLC are set up with the same communication standard: Ethernet/IP, Modbus TCP, Profinet…. If the IP is set correctly but the wrong protocol is selected, the HMI will still not be able to communicate.
- Secure the internal network: Make sure the HMI IP is not accessed illegally from the outside. Businesses should set up firewalls, manage users and regularly change the administrator password to protect data security.
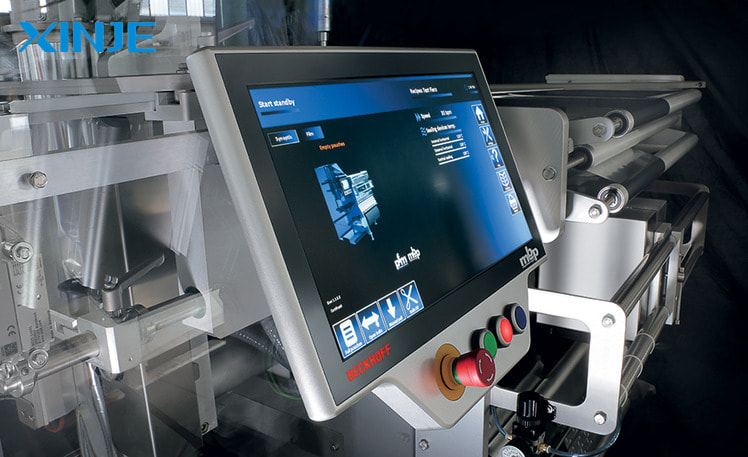
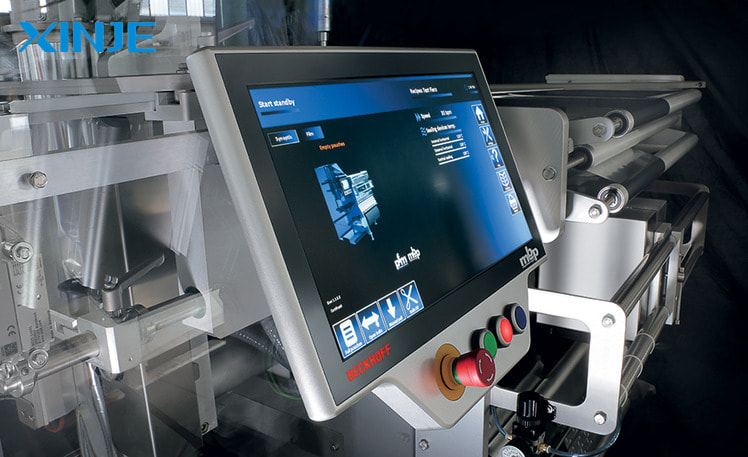
What are the common errors when setting up IP for HMI?
Although the IP setting process for HMI is quite simple, if not careful, errors can easily occur, interrupting the connection with PLC or SCADA. Below are common errors and basic solutions that engineers need to pay attention to.
- HMI does not receive IP: This is a common error when HMI loses power, has a firmware error or has not saved the network configuration after installation. Engineers should check the settings in the System Menu again, make sure the IP has been assigned correctly and saved before restarting.
- Duplicate IP causes conflicts: If 2 devices have the same IP address, the network will not know which device to send data to first. As a result, the HMI reports a connection error or intermittent signal loss. Solution: create an IP address management table and check carefully before assigning a new IP.
- Unable to ping PLC/HMI: Even though the IP is set correctly, the HMI still cannot communicate with the PLC, usually due to: different IP range, wrong Subnet Mask, faulty network cable or inactive PLC network module. Engineers should use the Ping command to check and review the network cable and switch.
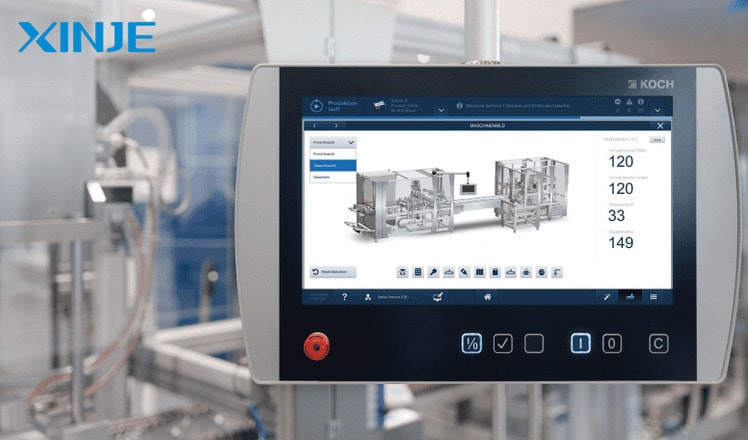
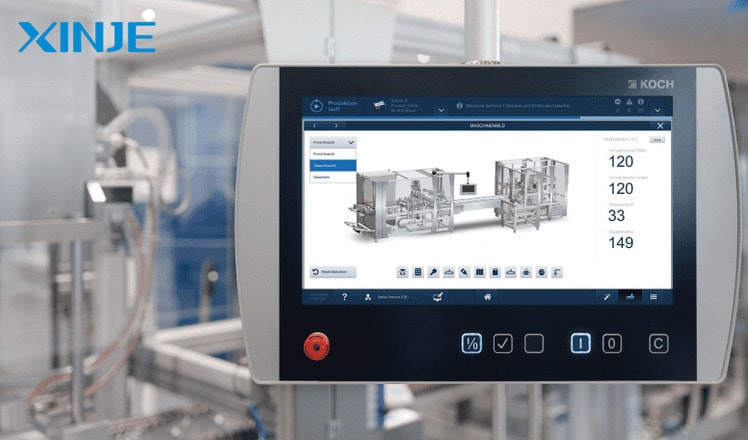
Conclusion
Setting the correct IP address for the HMI plays a key role in the stable operation of the automation system, avoiding interruptions and connection loss errors. Just setting the wrong IP or duplicate IP, the entire production line can stop, causing cost damage.
Therefore, the operating engineer and the IT department need to coordinate closely, build a clear network diagram, allocate logical IP and regularly check to maintain a safe and reliable system.