In factory automation systems, timely detection and troubleshooting are key factors to maintain stable operations. This is the reason why Alarm Management – alarm management – is increasingly focused on, especially when integrated with HMI (Human Machine Interface). The following article will help you understand how HMI supports displaying, controlling and optimizing alarms in the production line.
What is Alarm Management?
Alarm Management is the process of designing, operating and improving alarm systems in automation lines.
In factories, this system is responsible for detecting abnormal conditions (eg: temperature exceeding threshold, pressure drop, sensor error…) and sending alarms to operators for timely action.
The goal of Alarm Management is to ensure that each alarm is timely, clear and actionable, helping to maintain safety and efficiency for the entire production process.
How does Alarm Management support HMI?
HMI plays a central role in visualizing and handling alarms from the automation system. An effective Alarm Management system when integrated on HMI will bring many supporting features such as:
- Clear alarm display: HMI uses colors, icons and sounds to distinguish alarm levels such as minor errors, serious errors or emergency stops.
- Alarm classification and prioritization: Alarms are grouped by priority (critical, warning…) to help operators handle serious errors first.
- Alarm confirmation function: HMI allows operators to confirm receipt of alarm information, thereby supporting the tracking and analysis process later.
- Integrated alarm log (alarm history): Save all alarms that have occurred with time, status and confirmer, supporting optimal maintenance and improvement work.
With these features, HMI is not only a display tool, but also a powerful assistant in alarm management and analysis, ensuring safe and seamless operation of the chain.
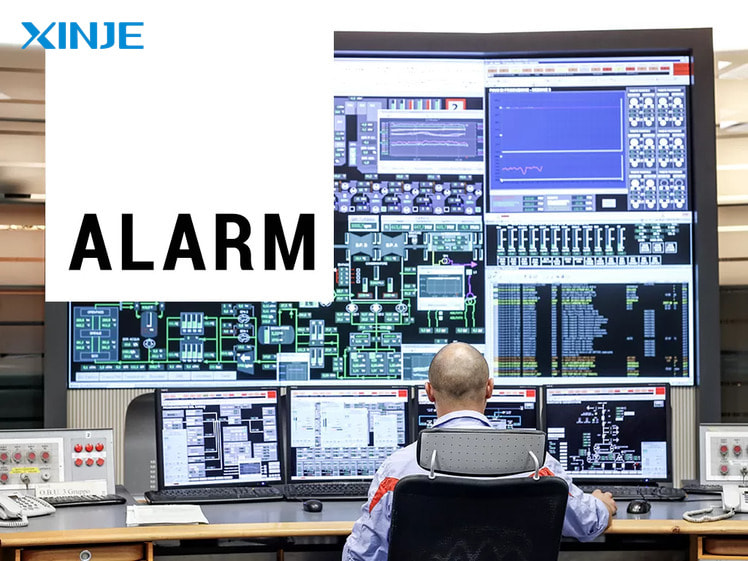
What are the important components in the Alarm Management system?
An effective Alarm Management system not only relies on processing software but also depends on seamless integration with HMI devices. Below are 4 core components that help manage alarms via HMI to become accurate, fast and easy to control:
- Alarm Detection: This is the first step in the alarm system. Devices such as sensors, switches, PLC controllers will continuously monitor technical parameters (temperature, pressure, speed, liquid level, etc.). When detecting a value exceeding the threshold or a system error, a signal will be sent to the HMI.
- Alarm Display: After detection, the HMI will display the alarm information on the user interface. Normally, alarms will be distinguished by color (red, yellow, orange, etc.), icons or sounds for easy recognition by the operator.
- Alarm Acknowledgement: When receiving an alarm, the operator can confirm or turn off the alarm directly on the HMI. This not only makes management easier but also supports the process of monitoring performance and handling responsibility.
- Alarm History: All alarms that have occurred are stored as an alarm log in the HMI or connected server. This data includes: time of occurrence, alarm description, processing time and operator.
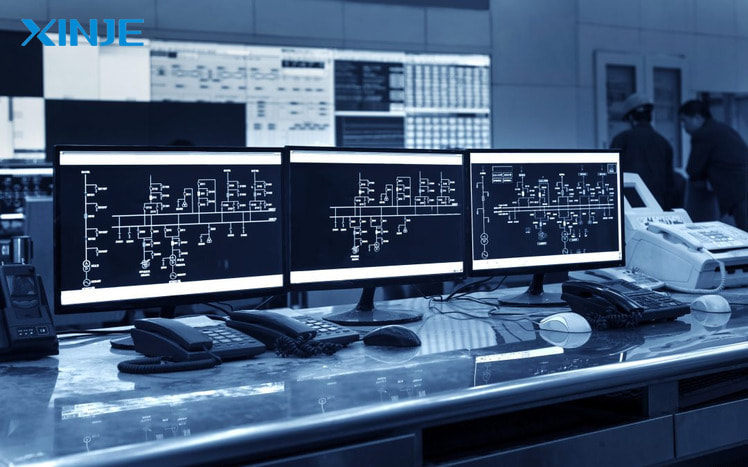
What are the benefits of managing Alarms through HMI in the factory?
When the Alarm Management system is directly integrated with the HMI, businesses not only improve monitoring capabilities but also optimize production operations in many aspects:
- Increase the ability to respond quickly to incidents: The HMI displays real-time warnings to help operators detect problems as soon as they occur and handle them promptly, limiting the spread of machine damage.
- Minimize downtime and losses: Rapid detection and troubleshooting will reduce unnecessary downtime, thereby improving operating efficiency and saving production costs.
- Optimize operating resources: HMI helps visualize warning information, limit operating errors and reduce pressure on operating personnel, especially in environments with many complex devices and lines.
- Easy training and transfer: Thanks to the friendly interface, HMI helps new employees quickly become familiar with the warning process, reducing training time.
- Support process analysis and improvement: Information stored in Alarm History helps technicians trace errors, analyze trends and make technical improvements to improve system reliability.
What is the practical application of Alarm Management in production lines?
In many industries, the application of Alarm Management through HMI has become an important standard in operations:
- Food and beverage industry: HMI system warns of problems with temperature, autoclave pressure, or packaging errors to ensure product quality and food safety.
- Pharmaceutical industry: Strictly monitor production conditions such as humidity, cleanroom temperature, warn of drug mixing or packaging errors to comply with GMP regulations.
- Electronic components manufacturing industry: Alarm through HMI helps detect automatic assembly errors, warn of deviations in the pick-and-place system or circuit board inspection process.
- Precision engineering and automotive industry: In CNC machining, assembly or automatic painting lines, HMI warnings help detect workpiece jams, tool errors, out of supplies, etc. before the problem spreads.
- Packaging and automated packaging industry: HMI alerts of machine jams, material shortages, or sensor failures, helping to ensure consistent and accurate packaging speeds.
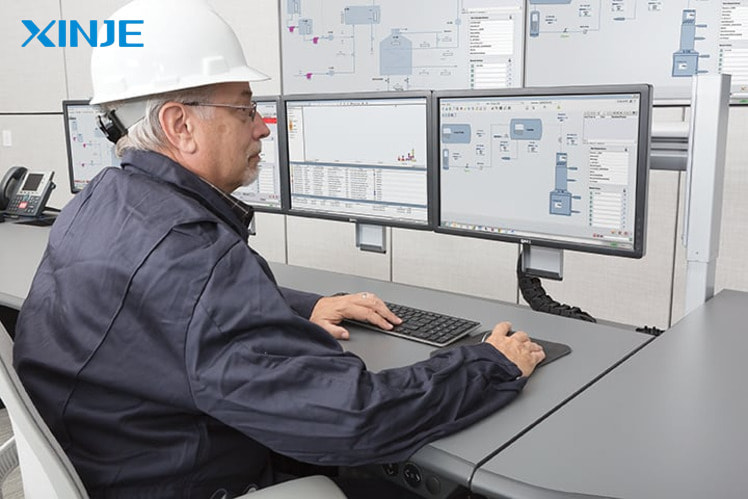
What are the things to consider when designing an Alarm system?
An effective alarm system depends not only on detecting problems, but also on how to design the alarm interface to be intuitive, easy to understand and not overload the operator with information. Here are some important factors to consider when building an Alarm system on HMI:
- Avoid “alarm flooding” – overloading alarms: One of the most common mistakes is to have too many alarms displayed at the same time, causing the operator to be “overwhelmed” and unable to distinguish which alarms are important. This reduces the effectiveness of response and can easily lead to missing serious alarms.
- Group alarms by area or equipment type: Grouping alarms helps operators easily identify where the problem occurs (eg: filling area alarm, packaging area alarm, etc.). This reduces the time spent searching for the cause and speeds up the process.
- Clear alarm hierarchy: Each alarm should be assigned a priority level: low, medium, severe. The use of appropriate colors and sounds helps to quickly communicate the level of urgency.
Investing in alarm interface design on HMI not only helps the system operate more smoothly, but also minimizes risks and enhances professionalism in modern factories.
Conclusion
In the modern manufacturing context, where every moment of downtime can cause great losses, Alarm Management plays a key role in protecting the line and optimizing operational performance.
When integrated directly into the HMI, the alarm system not only becomes intuitive and easy to use, but also enhances the ability to respond quickly and manage incidents intelligently.