In the rapidly evolving industrial automation landscape, the ability to facilitate seamless communication between devices is essential. Human Machine Interface (HMI) systems rely heavily on robust communication protocols to provide real-time monitoring, control, and diagnostics. Among the most widely used industrial protocols, today are Modbus, Ethernet, and Profibus. Each of these protocols has its strengths, challenges, and suitable applications.
This article will explore the core concepts, benefits, and limitations of Modbus, Ethernet, and Profibus, along with a comparative analysis to help engineers and system integrators select the most suitable solution for their automation infrastructure.
Modbus
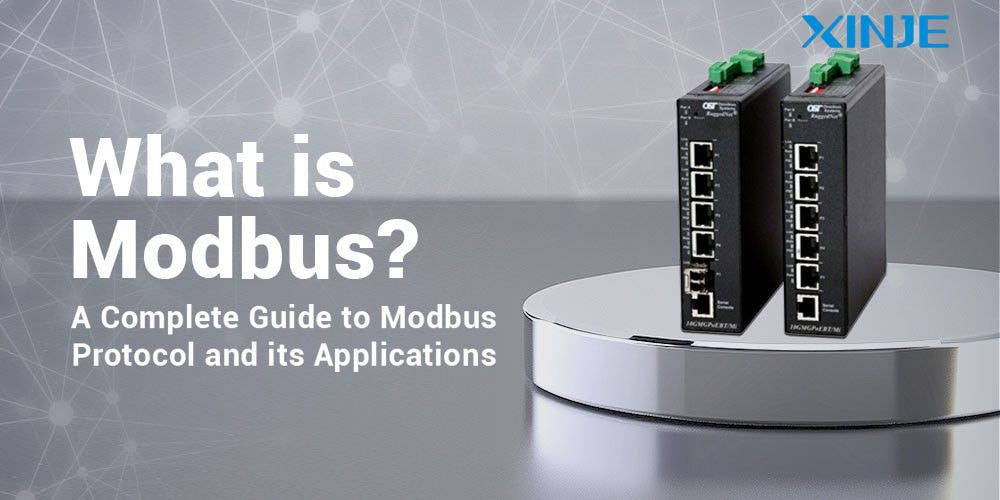
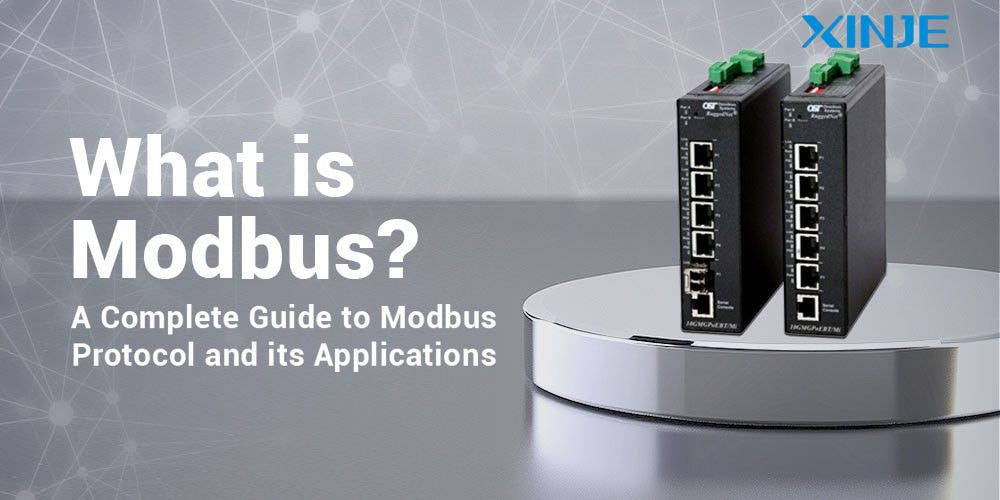
Modbus is one of the oldest and most established communications protocols in industrial automation. Modbus was designed to allow communication between programmable logic controllers (PLCs) and other devices over serial lines such as RS-232 or RS-485. Over time, it has evolved to support communication over TCP/IP (Modbus TCP), allowing for wider application in modern networking environments.
What are the advantages of Modbus?
- Simplicity and Openness: Modbus is easy to implement and requires minimal resources. Its open standard allows any manufacturer to integrate the protocol without licensing fees.
- Widespread Adoption: Due to its age and simplicity, Modbus is widely supported across a range of devices, from PLCs to sensors and HMIs.
- Low Hardware Requirements: It performs well even with basic hardware, making it a cost-effective choice for many small to medium-sized applications.
- Scalability: Modbus is scalable across different topologies, master/slave, peer-to-peer, and multi-master in some extensions like Modbus TCP.
What are the limitations of Modbus?
- Limited Speed: Traditional serial Modbus is relatively slow compared to modern protocols. Even Modbus TCP, while faster, still lacks some advanced features.
- No Data Security: Modbus has no built-in encryption or authentication, posing a risk in sensitive or remote applications.
- Lack of Real-Time Capabilities: Modbus cannot guarantee real-time data transfer, making it less ideal for high-speed or time-critical processes.
- Limited Device Count: There’s a limitation on the number of devices connected to a single bus, especially in Modbus RTU.
Ethernet
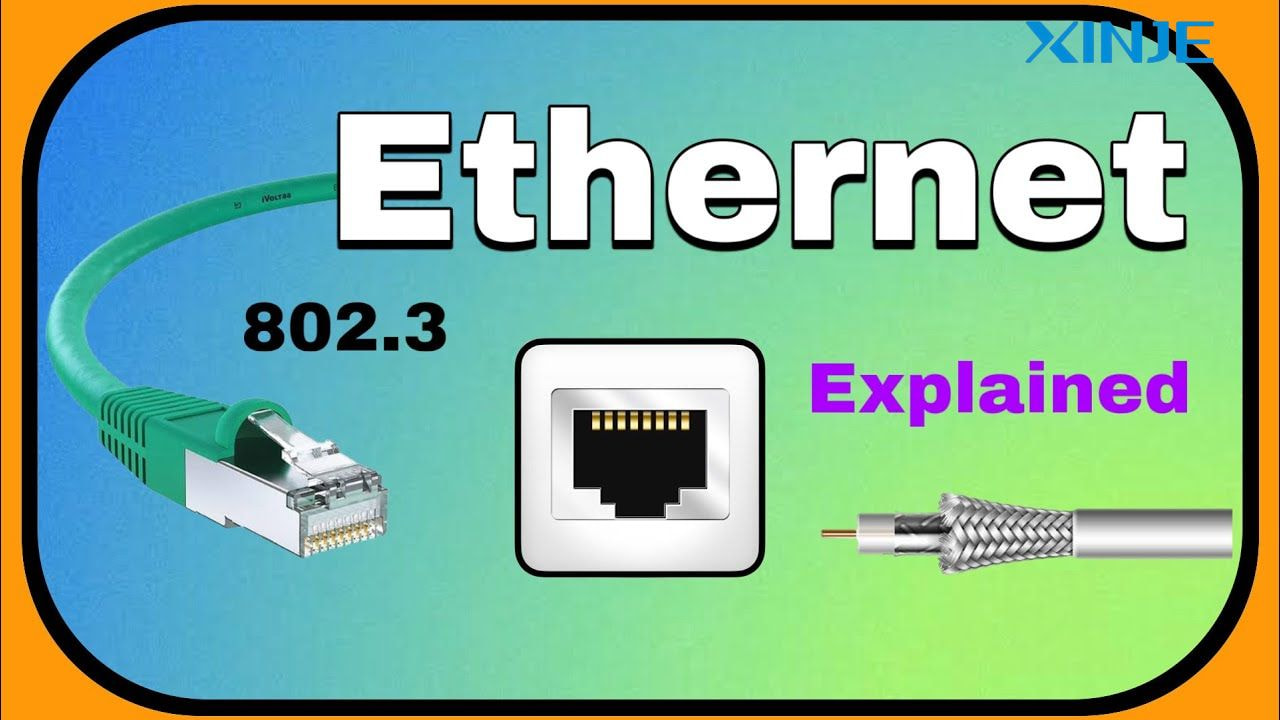
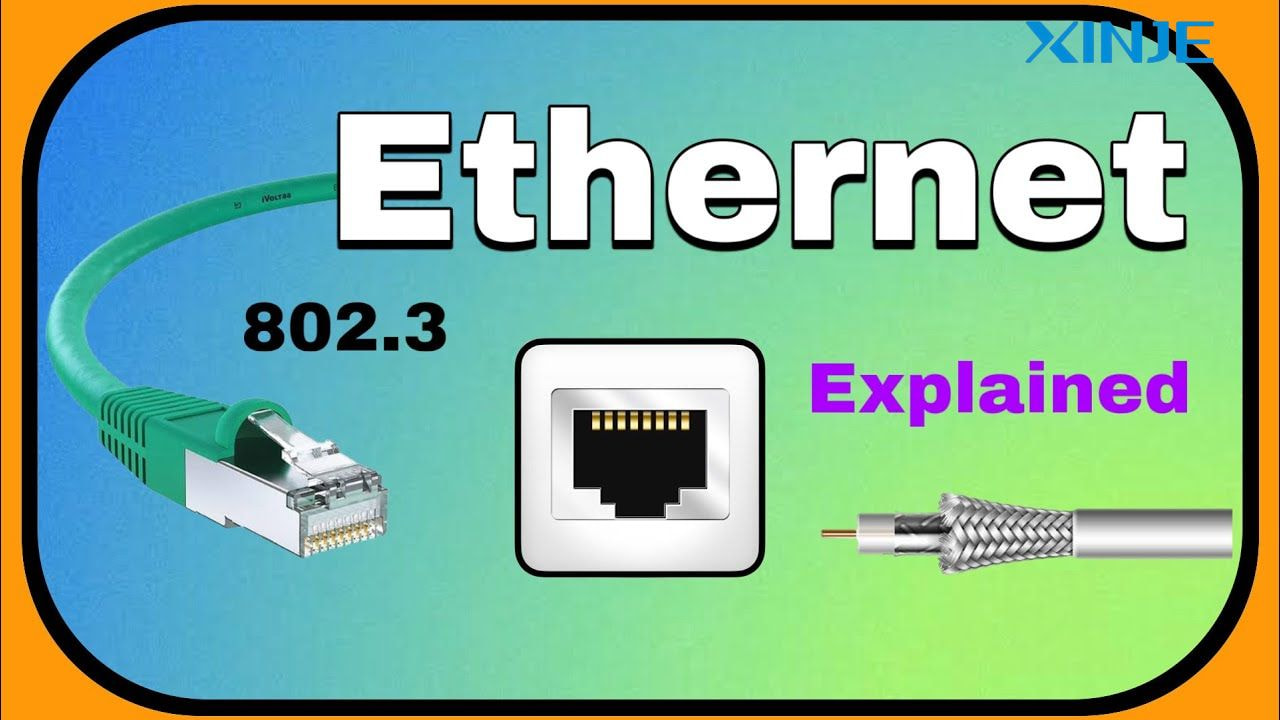
Ethernet is not a communication protocol per se, but rather a networking standard that supports various protocols, including Modbus TCP, Ethernet/IP, and PROFINET. It utilizes TCP/IP to communicate over physical media such as twisted-pair cables, fiber-optic cables, or wireless networks.
Ethernet is increasingly used in industrial environments due to its high speed, flexibility, and interoperability with enterprise networks.
What are the benefits of using Ethernet?
- High-Speed Data Transfer: Ethernet offers fast communication, suitable for complex automation systems with high data throughput.
- Standardization: Ethernet is universally recognized and can be integrated easily with the IT infrastructure.
- Multiple Protocol Support: It supports multiple industrial protocols like Modbus TCP, Ethernet/IP, and PROFINET on the same network.
- Scalability and Flexibility: Ethernet allows large-scale network expansion, remote monitoring, and easy device additions or reconfiguration.
- Enhanced Diagnostics: Modern Ethernet-based protocols offer robust diagnostic and monitoring features, which are critical for predictive maintenance and system reliability.
What challenges come with Ethernet use?
- Complexity: Ethernet networks require configuration of IP addresses, switches, and firewalls, adding complexity compared to simpler fieldbuses.
- Higher Cost: While hardware is standard, industrial-grade Ethernet components (cables, switches, connectors) are often more expensive.
- Security Risks: Since Ethernet connects to broader networks, it’s more exposed to cybersecurity threats if not adequately protected.
Profibus
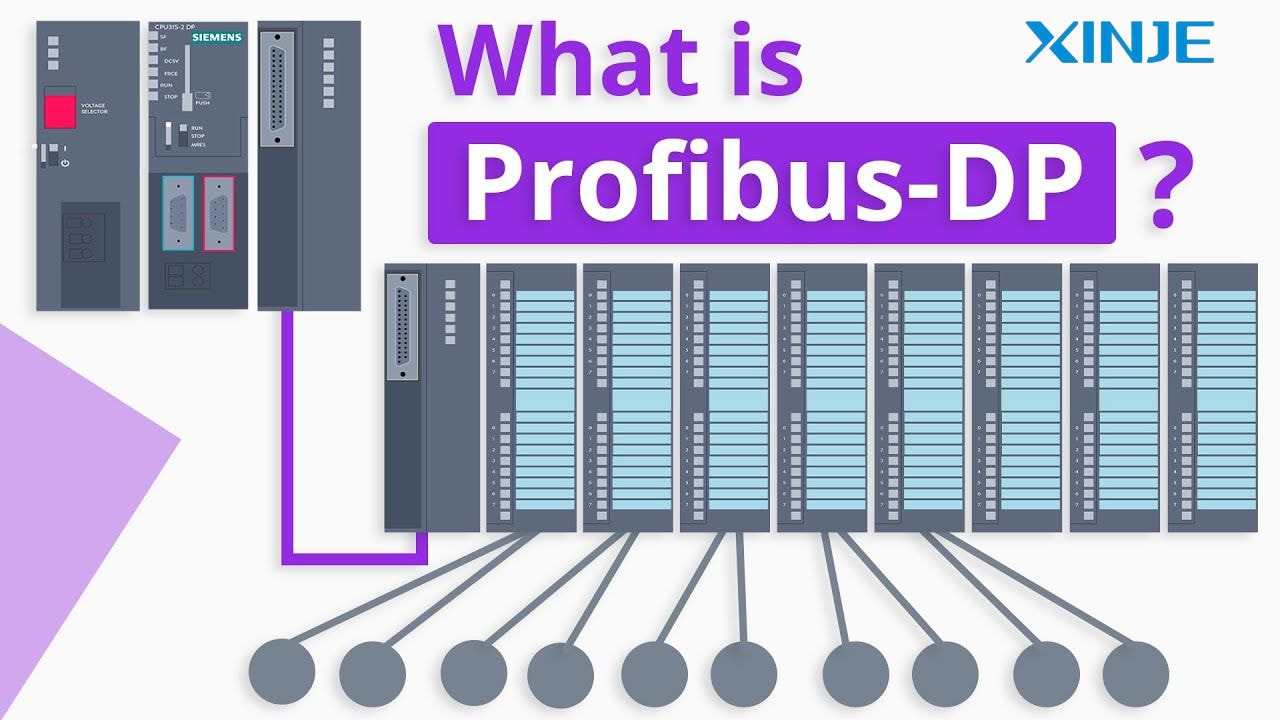
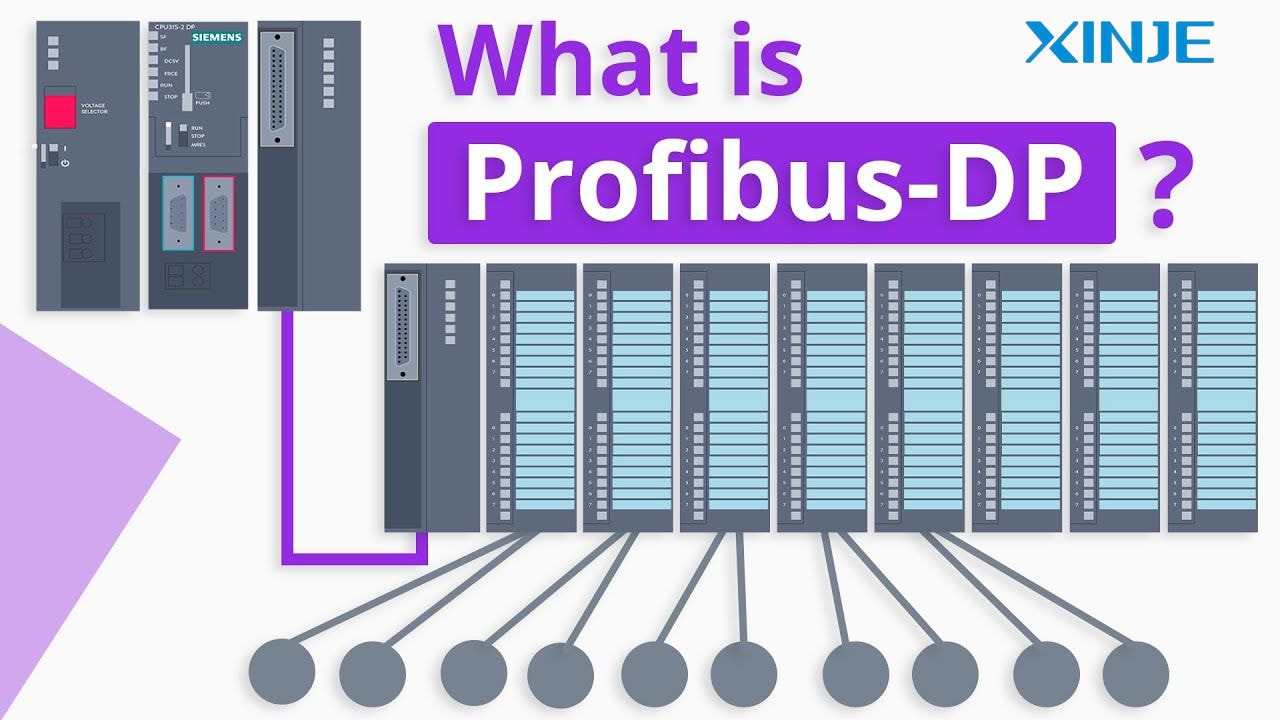
Profibus is a standardized fieldbus protocol widely adopted in European and global markets. Managed by PROFIBUS & PROFINET International (PI), Profibus supports two main variants: Profibus DP (Decentralized Peripheral Devices) for factory automation and Profibus PA (Process Automation) for process industries.
Why is Profibus a preferred choice in networking?
- Deterministic Communication: Profibus provides real-time communication, which is crucial for time-sensitive applications like motion control.
- Wide Device Compatibility: Profibus supports a large ecosystem of certified devices from numerous manufacturers.
- Reliable Operation: It performs reliably in harsh industrial environments with electromagnetic noise and long cable runs.
- Broad Deployment: Profibus is extensively used in automotive, chemical, and process industries, ensuring strong technical support and documentation.
What are the disadvantages of Profibus?
- Complex Setup: Compared to Modbus, setting up Profibus involves more sophisticated configuration tools and an understanding of GSD files.
- Limited Bandwidth: Profibus operates at slower speeds (up to 12 Mbps) compared to Ethernet-based protocols.
- Vendor-Specific Implementations: Some manufacturers implement Profibus features differently, leading to integration challenges.
What is the difference between Modbus and Profibus?
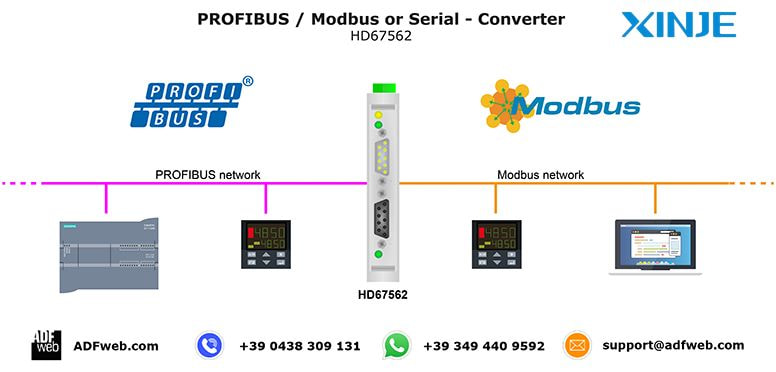
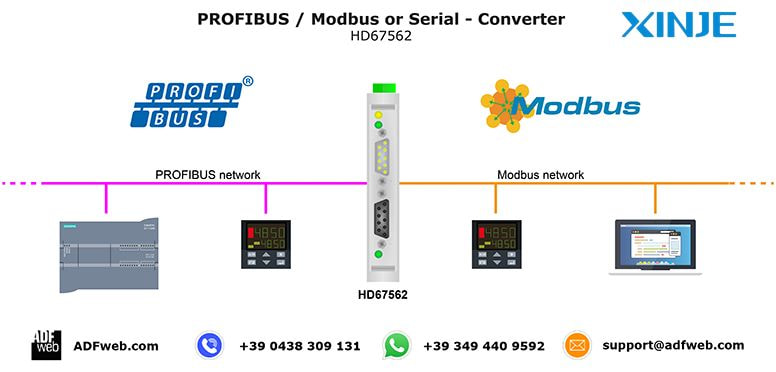
Both Modbus and Profibus serve similar purposes, facilitating device communication in industrial environments, but they differ significantly in terms of design, performance, and application scope.
Feature | Modbus | Profibus |
Protocol Type | Master/Slave (Modbus RTU) | Master/Slave, Cyclic |
Speed | Up to 115 kbps (RTU), higher with TCP | Up to 12 Mbps |
Media | RS-232, RS-485, Ethernet | RS-485 |
Real-Time Capability | Limited | Strong real-time capabilities |
Openness | Fully open and royalty-free | Standardized but more complex |
Diagnostics | Basic | Advanced diagnostics supported |
In summary, Modbus is ideal for simple applications where cost and ease of use are priorities. Profibus excels in complex and time-critical industrial environments. The choice between them depends on system requirements, existing infrastructure, and performance expectations.
Conclusion
The choice of communication protocol in HMI and industrial automation systems is critical for ensuring reliable, real-time, and secure data exchange. Each protocol comes with trade-offs, and no single solution fits every application. Therefore, understanding the operational context, performance requirements, and long-term support is key to selecting the right technology.
For industrial integrators and automation engineers, being well-versed in Modbus, Ethernet, and Profibus helps future-proof your systems, optimize communication efficiency, and ensure seamless interoperability across machines and networks.