A digital servo is a type of servo motor that uses a microprocessor-based controller to regulate its output. Unlike analog servos, which rely on continuous analog signals, digital servos receive high-frequency signals, typically around 300 pulses per second, that are then processed by an internal digital circuit to control the motor’s position, speed, and torque with high precision.
An analog servo, in contrast, operates on traditional Pulse Width Modulation (PWM) signals, typically at a lower refresh rate of around 50 pulses per second. The internal circuit interprets these signals to adjust the servo’s position accordingly. At the same time, simpler in design and often more cost-effective, analog servos may lack the responsiveness and control flexibility of their digital counterparts.
What is the function of a digital servo?
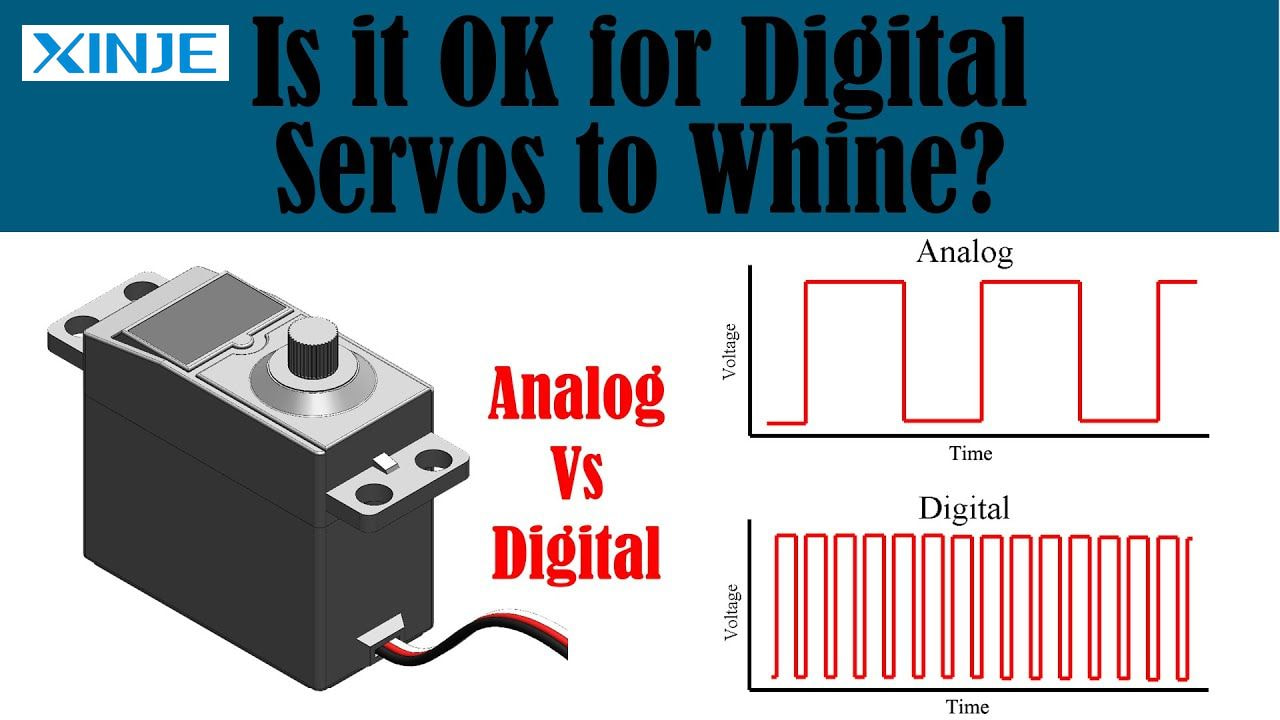
Digital servos offer enhanced functionality thanks to superior processing power and real-time feedback. Here’s how they work in a typical automation setup:
- Precise control: Digital servos process signals at much higher speeds, allowing for smoother, more accurate motion. They are often ideal for applications that require precise positioning and fast response, such as robotic arms, conveyor systems, and pick-and-place machines.
- Programmable settings: Many digital servos can be fine-tuned using a software interface, allowing engineers to adjust parameters such as speed, dead zones, and torque limits. This programmability supports complex automation tasks and helps extend system life through optimized performance.
- More holding torque: Thanks to high-frequency signal inputs, digital servos apply corrections more frequently to maintain position.
- Thermal and voltage protection: Some advanced digital servos have built-in protections against overheating and voltage fluctuations, improving durability and safety in industrial environments.
What is the function of an Analog servo?
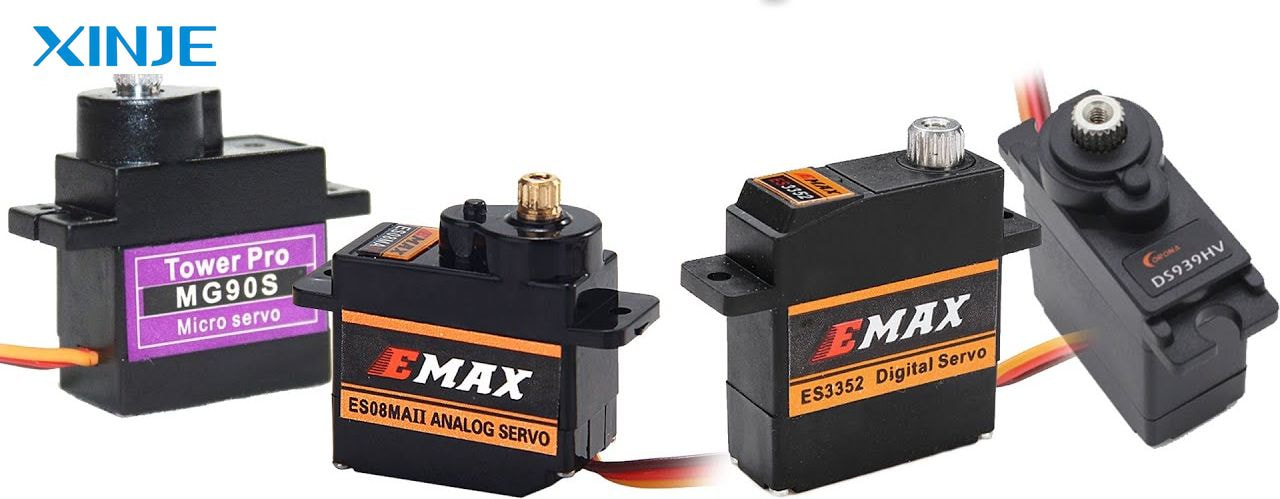
Despite their simplicity, analog servos still play an important role in many automation applications. Their core functions include:
- Basic motion control: Analog servos provide reliable control for simple applications such as controlling valves, flaps, or simple positioning mechanisms. They respond to a PWM signal and rotate the output shaft to the desired angle.
- Energy efficiency: Due to their lower sweep frequency and simpler electronics, analog servos consume less power when idle. This makes them a good choice for battery-powered systems or when energy efficiency is a top priority.
- Smooth motion in low-demand tasks: In non-critical systems where accuracy and speed are not a top priority, analog servos provide stable and predictable performance. They are suitable for systems that operate at slow speeds or involve linear motion.
- Cost-effective solution: In cases where budget constraints are more important than high-end features, analog servos offer an attractive balance between performance and cost.
What is the difference between analog and digital steering?
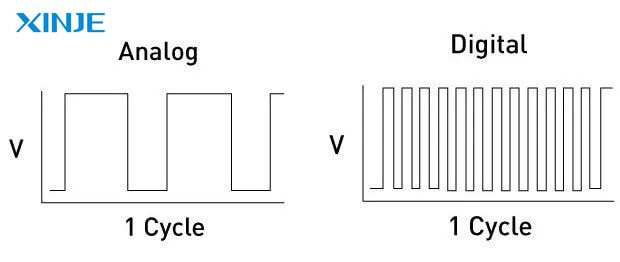
While both digital and analog servos serve the same fundamental purpose, controlling the angular position of a motor shaft, how they achieve this differs substantially, especially in terms of steering responsiveness and control logic.
Feature | Analog Servo | Digital Servo |
Signal Type | Standard PWM (~50 Hz) | High-frequency PWM (~300 Hz) |
Response Time | Slower | Faster |
Programmability | Limited or none | Highly customizable |
Power Consumption | Lower (especially at idle) | Higher (due to active circuitry) |
Application Fit | Basic automation, cost-sensitive jobs | Advanced automation, high-precision jobs |
Conclusion
Choosing between a digital and an analog servo motor depends largely on your application requirements. If your system demands speed, precision, and customization, a digital servo is the optimal solution. On the other hand, if your project is more cost-sensitive or doesn’t require fast responsiveness, an analog servo might be more than adequate.
Understanding these differences not only helps you select the right component but also ensures better system integration, longer lifespan, and more reliable automation.