Communication Protocols play an important role in connecting and synchronizing operations between devices in industrial automation systems. From traditional protocols such as Modbus, and Profibus to advanced solutions such as Profinet, they ensure smooth communication and help businesses increase productivity and save costs. Let’s learn about the concept, how it works and the benefits that Communication Protocols bring in the era of Industry 4.0.
What is Communication Protocols?
A communication protocol is a set of rules, standards, and regulations that define how data is transmitted between two or more devices. In the field of automation, a communication protocol ensures that every device in the production line understands and responds correctly to the information being transmitted. This is important in ensuring smooth coordination between sensors, control devices, PLCs, DCSs, SCADAs, and other systems.
For example, when a temperature sensor sends a signal to a PLC, the communication protocol specifies how that data is encoded, sent, received, and decoded. This allows the PLC to receive the correct information to adjust the system.
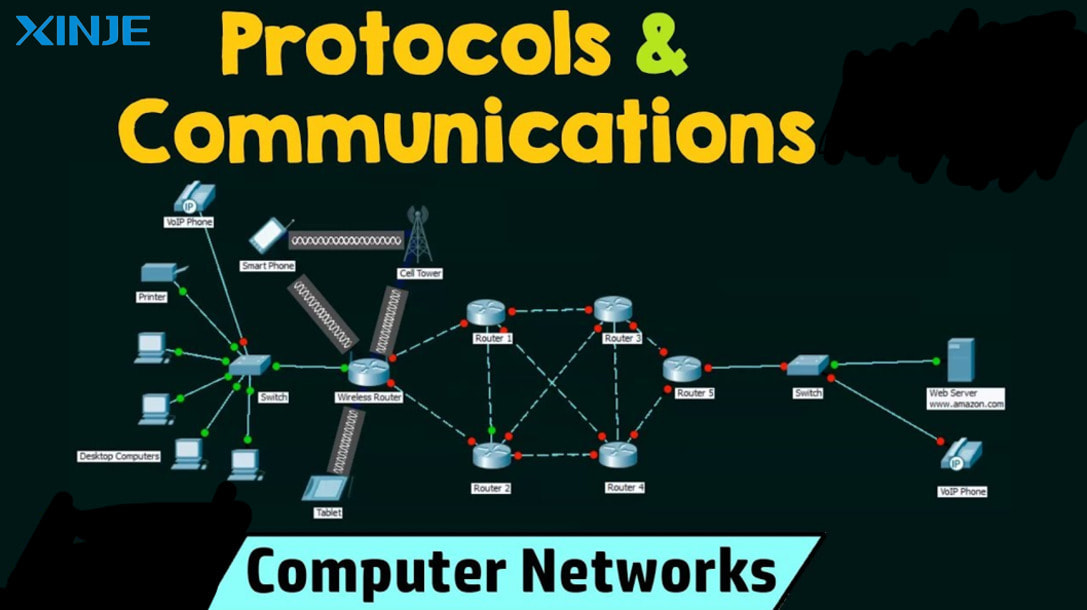
How does the Communication Protocol work?
Step 1: Determine the data structure
- The data to be transmitted is arranged in a specific structure so that both the sending device and the receiving device can process it easily. A packet usually has 3 main parts: (Header) containing source and destination information, (Payload) containing the main content such as sensor parameters, and (Trailer) for error checking. This structure helps the data to be properly formatted for convenient communication.
Step 2: Data transmission
- The packaged data will be sent over communication media such as RS-485 cable, Ethernet, or wireless network. The transmission process can take place in two ways. The first way is synchronous, where the data is sent according to a common clock signal. The second way is asynchronous, where separate start and stop signals are used for each packet.
Step 3: Data processing and decoding
- When the device receives the packet, it will analyze the contents of the packet based on the predetermined structure. This process involves determining the address of the receiving device, checking the command code, and processing the data as required. If the command code is valid, the device will continue to process the data, and then visually deliver the data to the output devices.
Step 4: Error checking and correction
- During the transmission process, data can be corrupted due to noise or hardware failure. The protocol uses methods such as CRC or Checksum to check the integrity of the data. If errors are detected, the device can apply error correction mechanisms such as retransmitting the packet or using automatic error correction code (Forward Error Correction). This ensures that the data transmitted to the receiving device is correct.
Step 5: Terminate the connection
- After the transmission is complete, the connection will be closed to free up network resources. In addition, some protocols also save the communication state to support subsequent sessions.
Thus, this step-by-step process ensures that communication between devices in the automation system is smooth, efficient and accurate. This helps businesses optimize production processes as well as increase work efficiency.
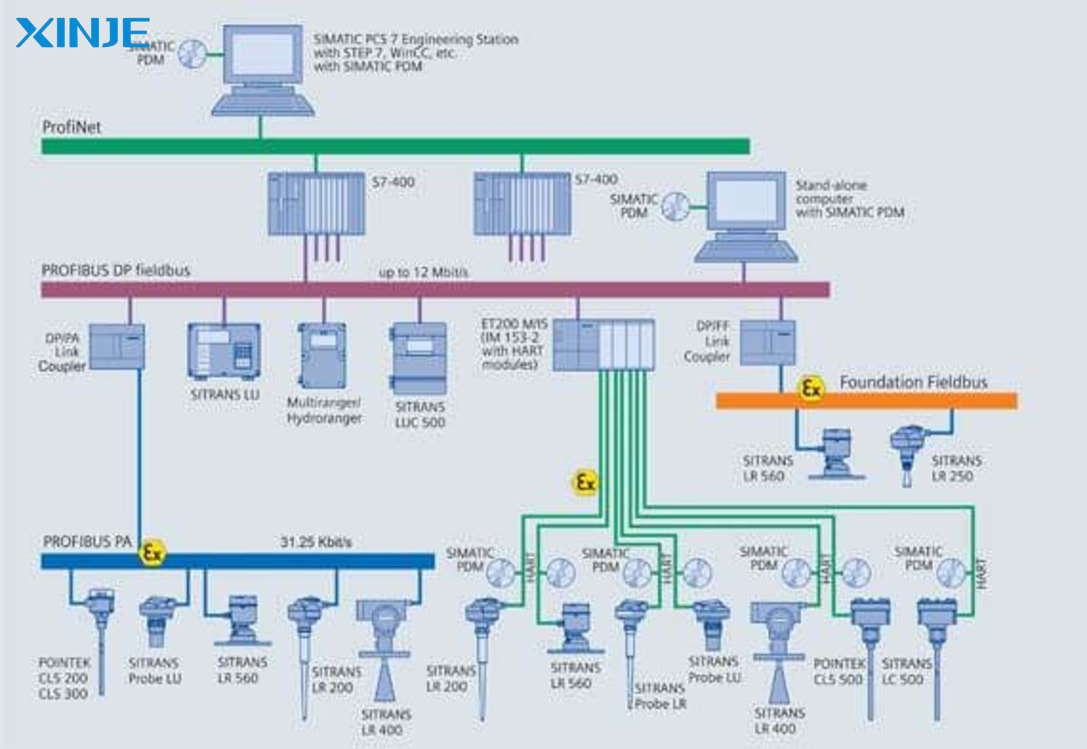
What are the common types of Communication Protocols today?
In industrial automation systems, each communication protocol is designed to meet specific requirements such as speed, transmission distance or scalability. Depending on the actual application, businesses can choose the appropriate protocol types to optimize performance and ensure seamless connection between devices. Below are 4 common types of protocols that are widely used in modern systems.
Serial Communication Protocols
Serial protocols are one of the first types of communication protocols, widely used in automation systems due to their simplicity and efficiency. They transmit data one bit at a time over a single transmission line, often used in point-to-point connections or small networks.
- RS-232: Is a point-to-point protocol, supporting only two devices to communicate directly with each other. Maximum distance: ~15m.
- RS-485: Supports bus networks with up to 32 devices on a transmission line (1 master and many slaves). Maximum distance: ~1200m.
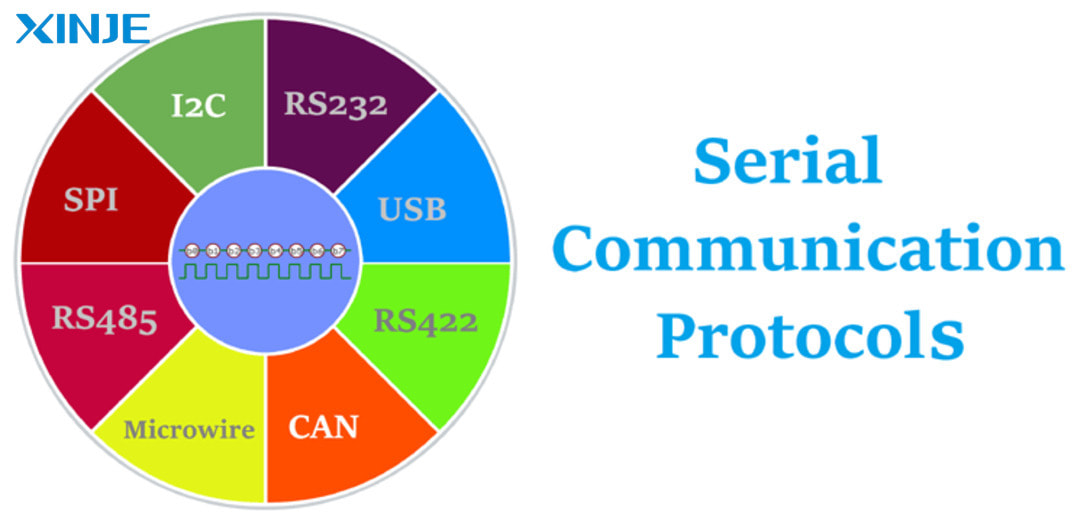
Fieldbus Protocols
Fieldbus is a group of advanced communication protocols, specifically designed to meet the needs of large industrial automation systems.
- Modbus: This is one of the oldest and most popular protocols, this protocol uses a master-slave structure to transmit data.
- Profibus: Profibus uses a bus structure to connect multiple devices (masters and slaves) on the same network. It is widely used in many industries due to its flexibility and high performance.
Industrial Ethernet Protocols
Industrial Ethernet evolved from conventional Ethernet technology, but was improved to meet the demanding needs of the industrial environment. This protocol supports high-speed data transmission and stable operation in harsh conditions.
- EtherNet/IP: Ensures high-speed real-time data transmission. In addition, this protocol is also compatible with a wide range of industrial devices, from sensors, actuators to large systems such as SCADA and MES.
- Profinet: This is a powerful protocol, designed to provide fast and reliable data transmission in complex automation systems.
Wireless Communication Protocols
Wireless protocols are increasingly popular due to their flexibility and ability to reduce wiring costs. They are especially useful in environments that require remote monitoring, frequent device movement, or where traditional cabling is difficult to deploy.
- Zigbee: Ideal for wireless sensor networks or industrial IoT networks.
- Wi-Fi: Used to connect devices that require high bandwidth or operate in industrial wireless LANs.
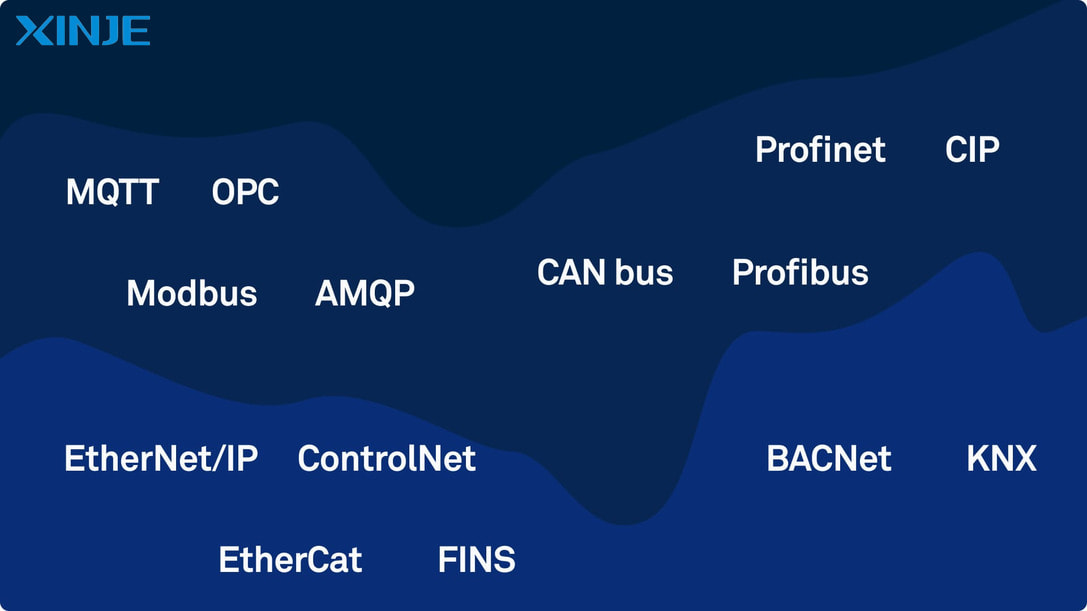
Why use Communication Protocols in manufacturing systems?
- Increased operational efficiency: Communication protocols standardize the way devices exchange data, helping to minimize communication errors and increase processing speed. This helps optimize system performance, reduce downtime, and ensure continuous production lines.
- Flexible integration capabilities: Protocols such as Modbus, Profibus, or EtherNet/IP allow for the connection of devices from different manufacturers. As a result, businesses can easily expand or upgrade their systems without being tied to a specific brand, saving on investment costs.
- Ensure safety: Currently, protocols have built-in security features such as data encryption, device authentication, and anti-unauthorized access. This helps protect the business’s production system from cyber security threats.
- Save costs: Modern protocols allow businesses to automate many production processes, thereby saving on labor costs.
- Support for the deployment of new technologies: Communication Protocols are the foundation for advanced technologies such as the Internet of Things (IoT), Big Data, and Artificial Intelligence (AI). This makes it easy for businesses to apply modern solutions to enhance their competitiveness.
Communication Protocols not only improve operational efficiency but also help businesses save costs, and increase flexibility and safety in operations. This is a key factor for businesses to maintain a competitive advantage in the era of Industry 4.0.
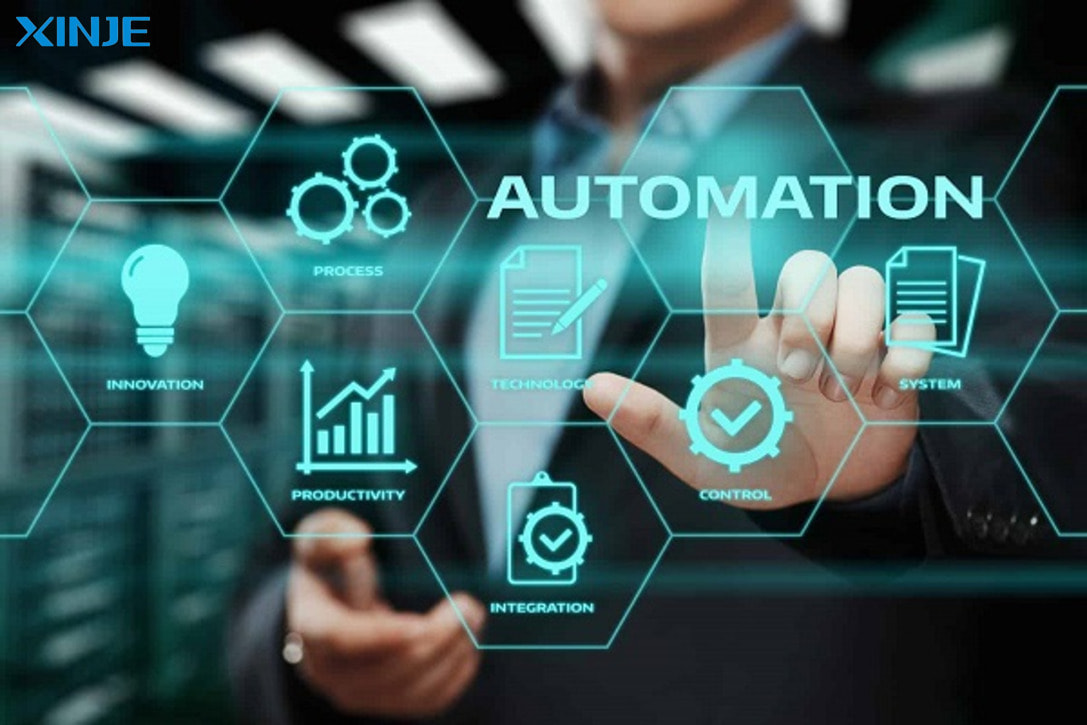
Conclusion
Communication Protocols are the foundation for the development and operation of industrial automation systems. Choosing and implementing the right protocol not only ensures production efficiency but also helps businesses quickly adapt to future technological changes. Understanding and applying communication protocols correctly will bring outstanding competitive advantages in the era of Industry 4.0.