Efficient, flexible, reliable and stable
With the popularization of the application of informatized big data, the traditional warehousing and logistics operation methods have been unable to meet the rapidly growing business needs, and it is necessary to accelerate the construction of automation and intelligence of warehousing and logistics. The introduction of intelligent warehousing can efficiently connect production and logistics and improve the production efficiency of enterprises.
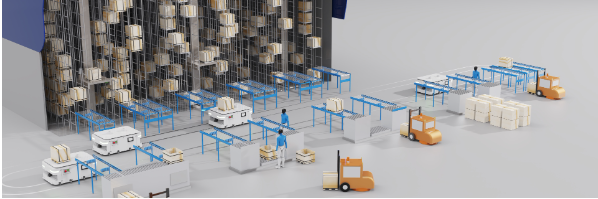
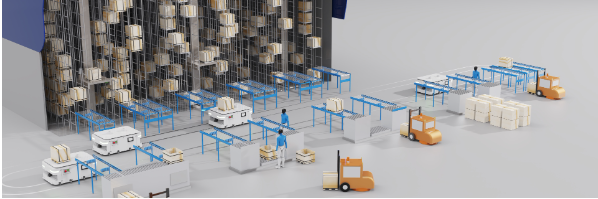
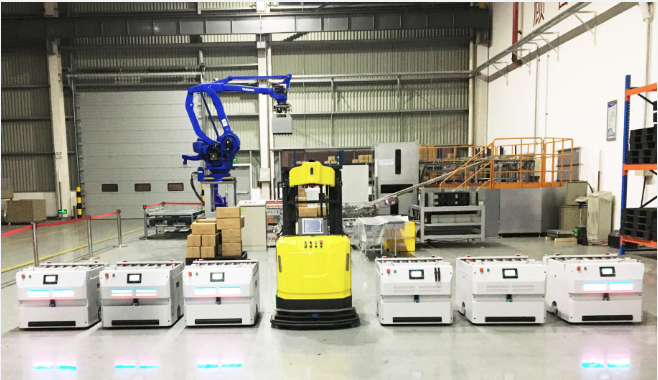
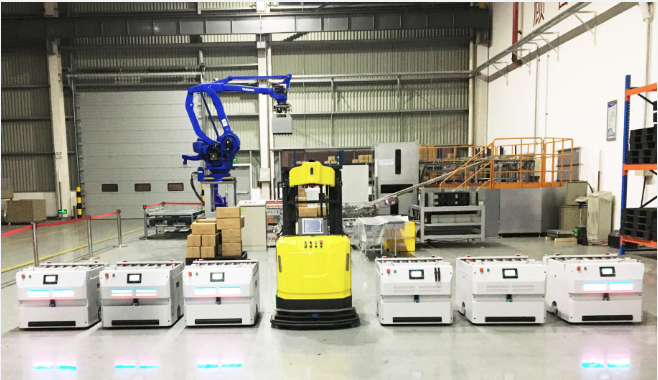
System Introduction
Magnetic stripe navigation differential AGV is mainly for the cargo handling of loads within 1 ton. It can automatically dock with the goods through the jacking-up or roller transfer mechanism. It has the characteristics of fixed task path, high walking accuracy, and stable operation. In application, it greatly improves the work efficiency and has wide applications in the production line handling of the automotive, 3C, and manufacturing industries.
Application scenarios
Load capacity: suitable for handling goods with a load of less than 1 ton
Main application industries: production line handling in the automotive, 3C, and manufacturing industries
Control solution
The control system collects signals such as magnetic navigation sensor, RFID sensor, laser obstacle avoidance, and safety edge touch, and walks according to the set task path trajectory. Through the data of the magnetic guide sensor, the differential control of the driving wheels is carried out to realize the control of correction and steering to ensure that the AGV can walk stably along the magnetic stripe.
When the RFID sensor detects the function tag card arranged on the AGV’s walking path, the AGV begins to perform functions such as fork selection, in-place rotation, and stop to realize the navigation control, function control, and safety protection of the AGV.
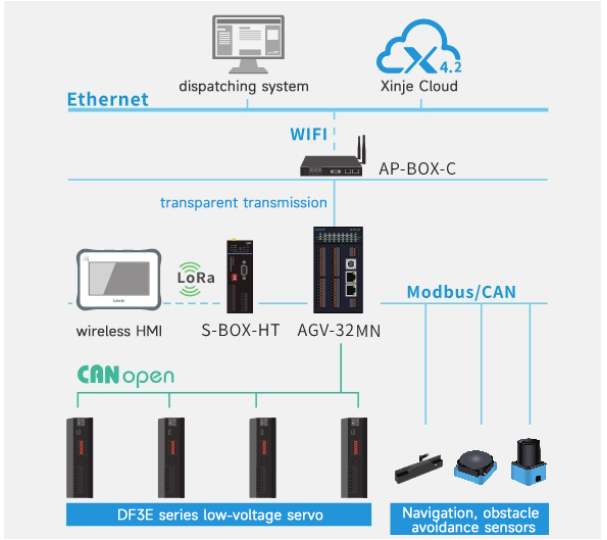
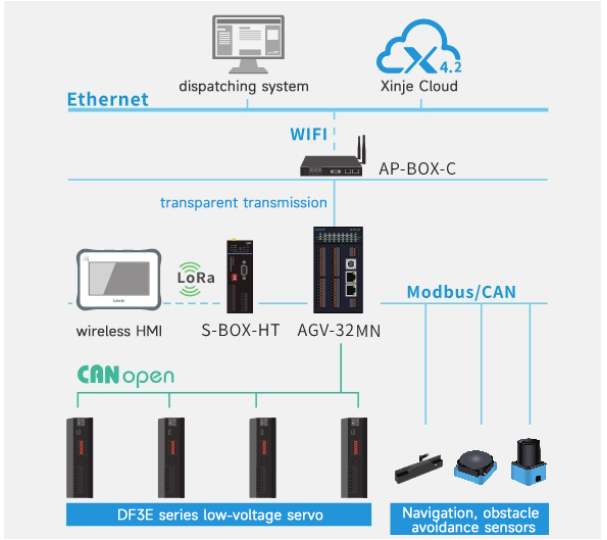