PWM – short for Pulse Width Modulation – is a pulse width modulation technique widely used in controlling motors, LEDs, industrial fans, etc. This article by XINJE will help you understand the operating principle, role and practical application of PWM in automation systems.
What is Pulse Width Modulation?
PWM (Pulse Width Modulation) – also known as Pulse Width Modulation – is a method of controlling a signal by changing the width of the pulses in a fixed cycle.
Although the supply voltage is still on/off (digital), the average output voltage value can be flexibly adjusted by changing the on-time ratio (duty cycle).
Thanks to this principle, PWM is widely used to control the output load power efficiently and save energy. The most obvious example is adjusting the rotation speed of a DC motor, or changing the brightness of an LED without using a potentiometer.
What is the operating principle of PWM?
PWM operates based on a square pulse signal that is repeated in cycles. In each cycle, the signal is on (ON) for a certain period of time and then off (OFF) for the rest. The on-time ratio in a cycle is called the duty cycle, measured in percentage (%).
For example:
- Duty cycle 25%: on 25% of the time, off 75%
- Duty cycle 50%: on and off are equal
- Duty cycle 75%: on 75%, off 25%
Although the signal is only at two high/low levels, the average output voltage will change corresponding to the duty cycle. This allows the power supplied to the load (such as motor, LED…) to be adjusted smoothly and save energy, without constantly changing the voltage.
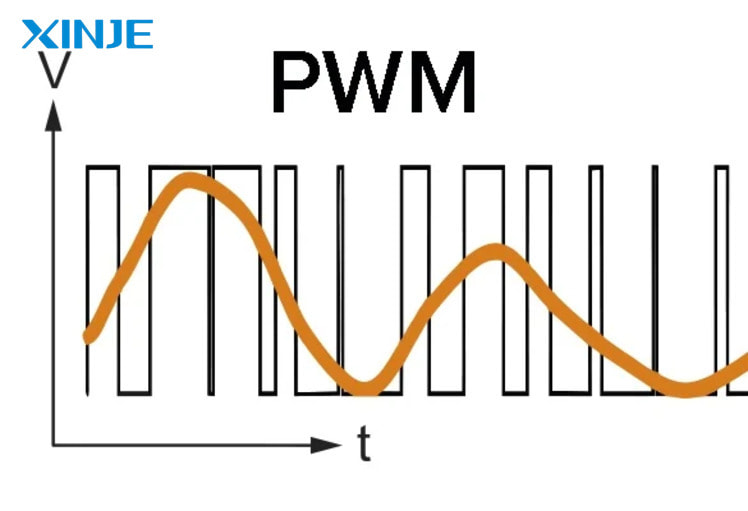
What is PWM and its relationship with the Servo system?
In motion control systems, especially analog servos, PWM is the most important input control signal. A servo operates based on receiving a PWM signal from the controller (such as microcontroller, Arduino, PLC…) to determine the rotation angle or shaft position.
In addition to its position control role, PWM can also regulate speed and torque, especially in closed-loop control systems where the feedback signal from the encoder is continuously compared with the input PWM signal to correct errors.
In short, PWM is the bridge between the controller and the actuator in the servo system – helping the system operate stably, accurately and efficiently.
What benefits does PWM bring to businesses?
PWM is not only a simple control method, but also brings many outstanding advantages in both performance and energy efficiency:
- Energy saving: PWM regulates power without continuously changing voltage, helping to reduce heat loss compared to linear control methods.
- Precise control: PWM allows precise control of speed, brightness or position by changing the pulse width (duty cycle), very suitable for servo and motor systems.
- Easy to integrate with microcontrollers/PLCs: Almost all microcontrollers, Arduino, Raspberry Pi or PLCs can generate or read PWM signals, making implementation simple and flexible.
- Wide range of applications: From controlling DC motors, servos to adjusting LED brightness, speaker volume, or even AC motor control inverters – PWM is present in automation systems.
- Stable signal, good anti-interference: Because the signal has only 2 clear ON/OFF states, it is less affected by electromagnetic interference than linear analog signals.
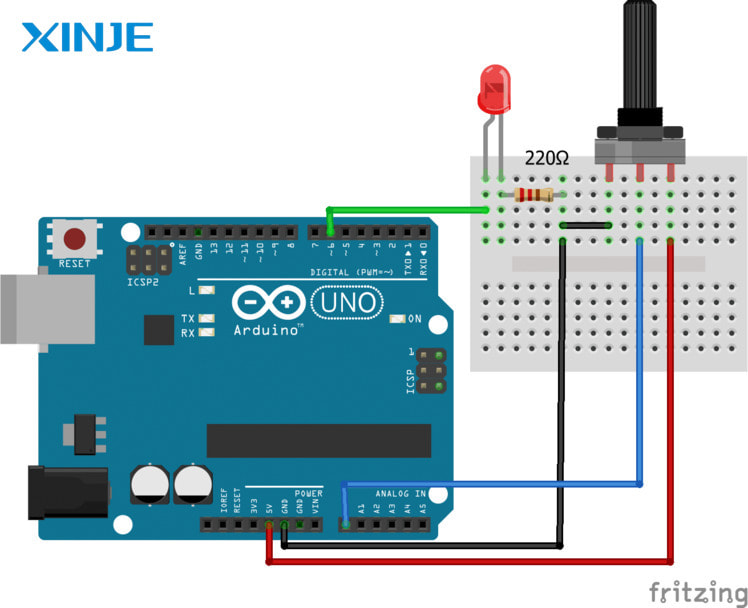
What are the notes when designing a PWM circuit?
Although PWM is a popular and effective control method, designing a PWM circuit requires careful consideration to ensure a stable signal and a durable circuit:
- Choosing the right frequency for the load: The PWM frequency should be selected according to the type of load: With a DC motor 10–20kHz helps reduce noise and improve performance. With LEDs ≥1kHz to avoid flickering. Choosing the wrong frequency can cause vibration, noise or reduce the life of components.
- Handling signal noise in industrial environments: PWM signals are susceptible to electromagnetic interference (EMI), especially when transmitted over long wires or near high-power devices. Solutions include using twisted pair cables or shielded cables, adding filter capacitors, inductors, separating the control signal lines and power sources
- Protect the power circuit when switching on/off quickly: Continuous switching can generate high voltage pulses that damage MOSFETs, IGBTs or loads. It is necessary to attach a flyback diode to the inductive load, use a snubber circuit to suppress the pulse, add a fuse or overcurrent protection circuit.
Pulse Width Modulation is commonly used in which fields?
PWM is a core technology in industrial control systems thanks to its ability to adjust output power efficiently without causing large energy losses. Here are some typical applications:
- Controlling servo motors and DC motors: PWM allows precise adjustment of motor speed, position or torque – an essential element in production lines, industrial robots, packaging machines, etc.
- Adjusting LED brightness and temperature: In industrial lighting systems or heaters, PWM is used to control the brightness of LED lights or the heat dissipation capacity of heating resistors.
- Controlling fans, pumps and HVAC systems: PWM helps adjust the speed of cooling fans, liquid pumps, or air conditioning ventilation systems (HVAC) to optimize performance and save energy.
- Integration with microcontrollers, Arduino, PLC: PWM is an easy-to-implement control method, supported in most popular microcontroller lines such as Arduino, STM32, Raspberry Pi, and expansion modules of industrial PLCs.
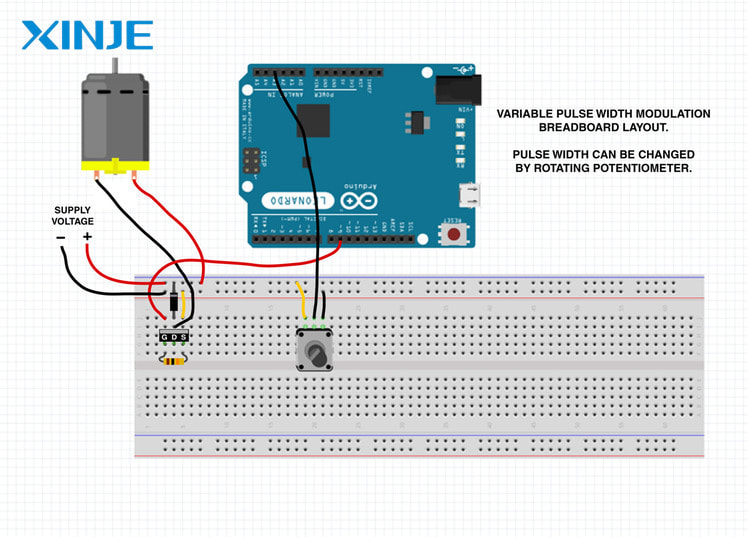
Conclusion
PWM (Pulse Width Modulation) is a simple but extremely effective modulation technique in controlling voltage, power and output control signals. Thanks to its flexible control and energy saving capabilities, PWM has become an indispensable component in automation systems – from controlling motors, LEDs to integrating with PLCs and microcontrollers.
Understanding the operating principles, advantages and disadvantages, and notes when designing PWM circuits will help businesses optimize device performance, extend component life and improve overall system efficiency.