Analog servo is a popular choice in basic motion control systems thanks to its low cost and ease of control using PWM signals or analog voltage. This article from XINJE will help you understand the structure, operating principles, and when to use analog servo instead of digital.
What is Analog Servo?
Analog servo is a type of servo motor that operates based on analog control signals, most commonly PWM pulses or voltages from 0–5V. When receiving the signal, the internal control circuit will adjust the corresponding motor shaft position, creating precise movement as required.
This type of servo often integrates a small DC motor, a potentiometer for position feedback and a simple analog control circuit.
Although it does not have the ability to process signals like a digital servo, analog servo still plays an important role in traditional servo systems – where simplicity, instantaneous response and low cost are top priorities.
How many parts does an Analog Servo consist of?
Analog servos usually consist of 3 main parts:
- Mini DC motor: This is the component that creates mechanical movement. The motor is usually small in size, high in speed and is powered according to position requirements.
- Potentiometer: Mounted directly on the motor output shaft. As the motor rotates, the potentiometer changes the resistance value and provides a feedback signal about the current position of the shaft. This is the element that makes up the closed-loop control system of the servo.
- Analog control circuit: This circuit receives the control signal from the central controller (usually PWM or analog voltage). It compares the input signal with the feedback value from the potentiometer and adjusts the amount of power supplied to the motor to achieve the target position.
All of the above components are built into a compact plastic or metal housing, making analog servos easy to install in devices such as RC models, basic robots, mini automatic arms, etc.
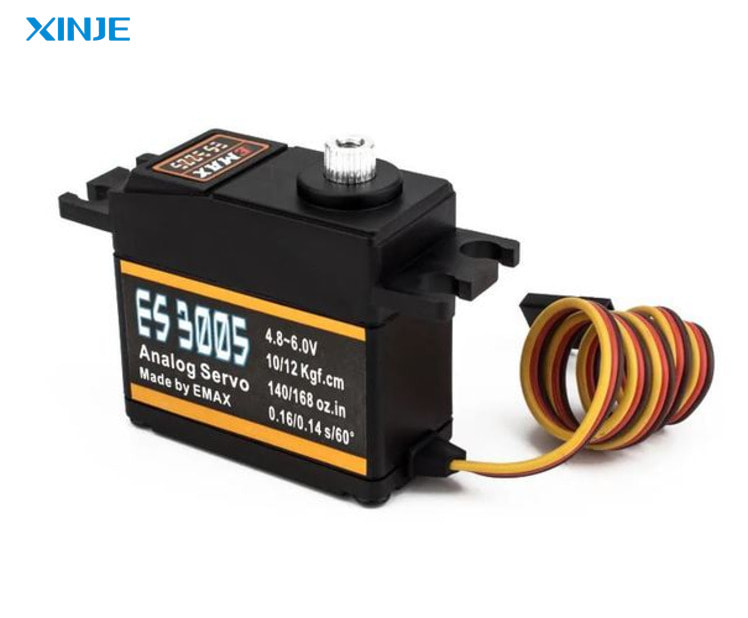
What is the difference between Analog Servo and Digital Servo?
In the motion control system, both analog servo and digital servo play an important role, but are distinctly different in the way they operate and their signal processing capabilities.
Control Signals
- Analog servos use a continuous signal (such as a standard 50Hz PWM)
- Digital servos use an internal microprocessor to analyze and control the signal, allowing for faster response and more precise processing.
Accuracy & Response
- Analog servos have a slower response and are susceptible to signal noise.
- Digital servos excel in accuracy, torque, and position holding.
Programmability & Cost
- Analog servos are simple in structure, inexpensive, and easy to use – suitable for less demanding applications.
- Digital servos can customize parameters (rotation angle, speed, force feedback) through software, but are typically more expensive.
Choose analog servos if you need an economical, easy-to-assemble solution for DIY projects, educational robots, or simple systems.
Choose digital servo if the application requires high precision, fast response, large torque and detailed programming capabilities (industrial robots, automatic arms, gimbals, etc.).
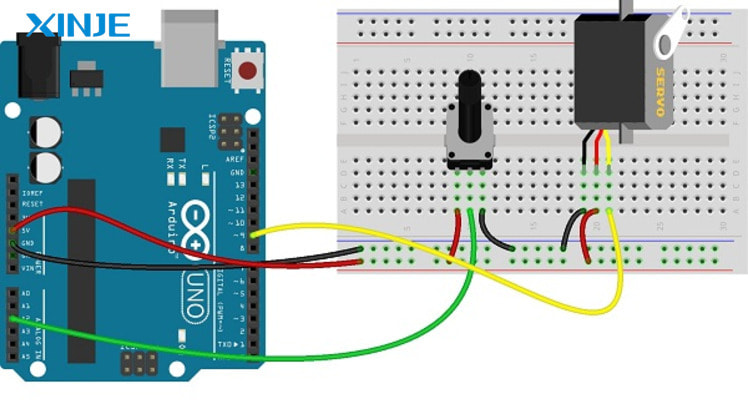
What are the advantages of Analog Servo?
With a simple structure and the ability to operate stably in many basic situations, analog servo is especially suitable for applications that do not require too high performance. Some outstanding advantages include:
- Low cost, easy to access: Analog servo is much cheaper than digital servo, thanks to its simple structure and does not use an internal microprocessor. This is an ideal choice for students, beginners in automatic control or projects that need to be implemented on a budget.
- Easy to use with basic control circuits: With common control signals (such as PWM 50Hz), analog servo can be directly connected to microcontrollers such as Arduino, Raspberry Pi, or PLCs with analog outputs without complicated configuration.
- Smooth response at low speeds: In simple movements with few sudden changes, analog servos provide smooth and stable control without the need for an intermediate processor.
- Popularity and ease of replacement: Because they are widely used in educational robots, RC models, digital toys, etc., analog servos are readily available on the market with a variety of power levels, sizes, and pin standards.
What are the disadvantages of Analog Servos?
Although analog servos have many advantages in terms of cost and simplicity, when considering performance in modern control systems – especially in industrial environments – they still have certain limitations.
Understanding these weaknesses will help you make more appropriate choices when designing or upgrading your system.
- Low accuracy: Because they do not use an internal microprocessor, analog servos respond to control signals linearly and continuously, so their ability to hold position or respond quickly to command changes is often worse than digital servos.
- Susceptible to signal interference: Due to the dependence on PWM signals or analog voltage, the system is susceptible to electromagnetic interference or line interference, leading to position deviation or slight vibration during operation.
- Weak torque and response: In tasks requiring strong force, large loads or fast response (such as industrial robots, specialized gimbals), analog servos often do not meet the requirements – easily hot, noisy or unstable operation.
- No support for advanced programming: Unlike digital servos, analog servos do not allow for customization of parameters such as delay, maximum speed, rotation angle limit
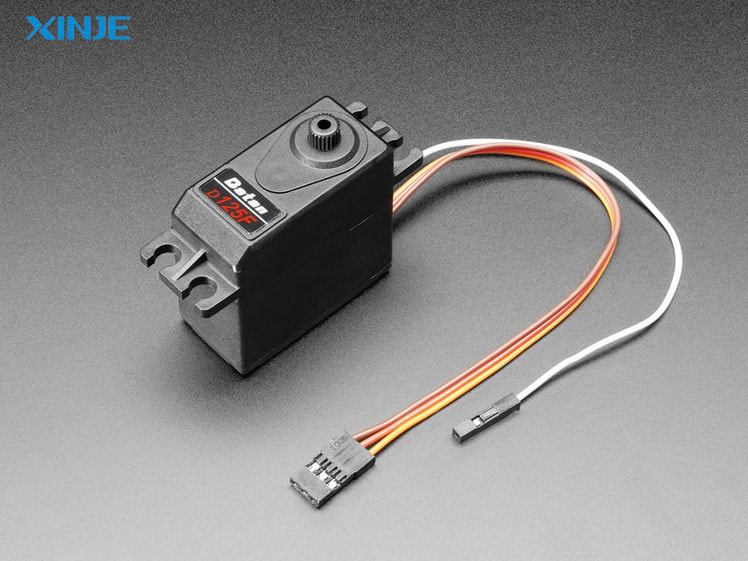
What are the considerations when choosing Analog Servo for businesses?
The choice of analog servo should be based on the technical specifications of the application and the specific usage environment. Here are some basic criteria to consider:
- Torque: Ensure enough force to pull, lift or rotate the part as required. The higher the torque, the stronger the servo.
- Rotation angle and response speed: Choose the type with the appropriate rotation angle (180° or 360°), fast response time if flexible operation is required.
- Control signal compatibility: Check the type of signal that the servo supports (analog PWM, 0–5V voltage, etc.) to be compatible with control circuits such as Arduino, analog PLC.
- Power supply voltage: Choose a servo with a suitable operating voltage level (usually 5V or 6–7.4V).
- Operating environment: Used for educational purposes, DIY at home or semi-industrial systems will require different durability and material structures.
Conclusion
Analog servos are still a worthy choice for basic motion control applications due to their ease of use, low cost, and popularity.
Although they cannot match digital servos in terms of accuracy or responsiveness, analog servos do a good job in educational environments, RC models, or simple automation systems.
Understanding the characteristics, advantages, disadvantages, and how to choose will help you effectively exploit this type of servo in each specific engineering problem — from a mini robot arm to a semi-automatic opening and closing system. Contact XINJE now for advice on choosing the Analog Servo that best suits your current system.