What is a Touchscreen unresponsive? An unresponsive touchscreen occurs when the display does not receive a signal from the finger or stylus, preventing the user from navigating menus, receiving alerts, or entering data. This issue can arise from various hardware or software errors and must be resolved promptly to prevent operational bottlenecks.
In this article, we will dive into common causes of unresponsive touchscreens, proven troubleshooting methods, and practical steps to prevent these issues in your HMI system.
What Causes an Unresponsive Touchscreen?
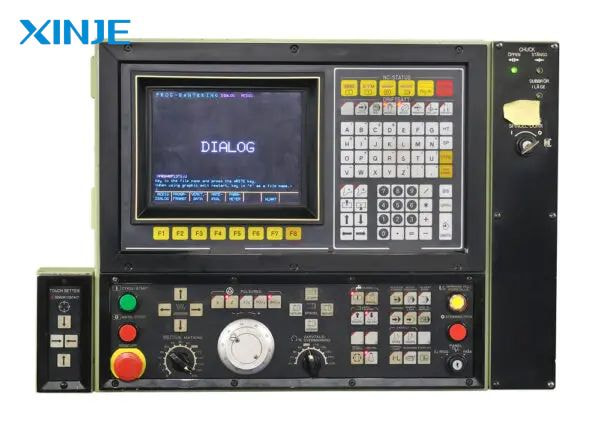
Many factors can lead to unresponsive touchscreens on industrial HMIs. Determining the root cause is essential to properly applying the fix. Some of the most common causes:
- Physical damage: HMI touchscreens operate in harsh industrial environments, often subjected to vibration, shock, or accidental impact. Over time, these external impacts can cause conditions such as cracked or broken screens, disconnected internal components, and unrecognized touch dead zones. These failures cannot be repaired and may require replacement.
- Failure of the touch sensor: Capacitive and resistive touch sensors are commonly used in HMIs. If the sensor itself fails due to age, manufacturing defects, or electrostatic discharge (ESD), the touchscreen may stop responding altogether.
- Software or firmware errors: Sometimes, corrupted firmware, incompatible updates, or faulty drivers can cause the touchscreen to freeze or become unstable. This can also happen if the HMI is overloaded with tasks beyond its capacity to handle.
- Environmental Conditions: Touchscreens are very sensitive to environmental changes, especially in industrial environments. Factors such as dust, humidity, temperature, or debris can all degrade the performance of the touchscreen.
- Loose or faulty connections: This can be caused by a loose ribbon cable or connector between the touchscreen panel and the controller board. Frequent vibrations and thermal expansion can cause connectors to loosen over time.
How to Fix an Unresponsive Touchscreen?
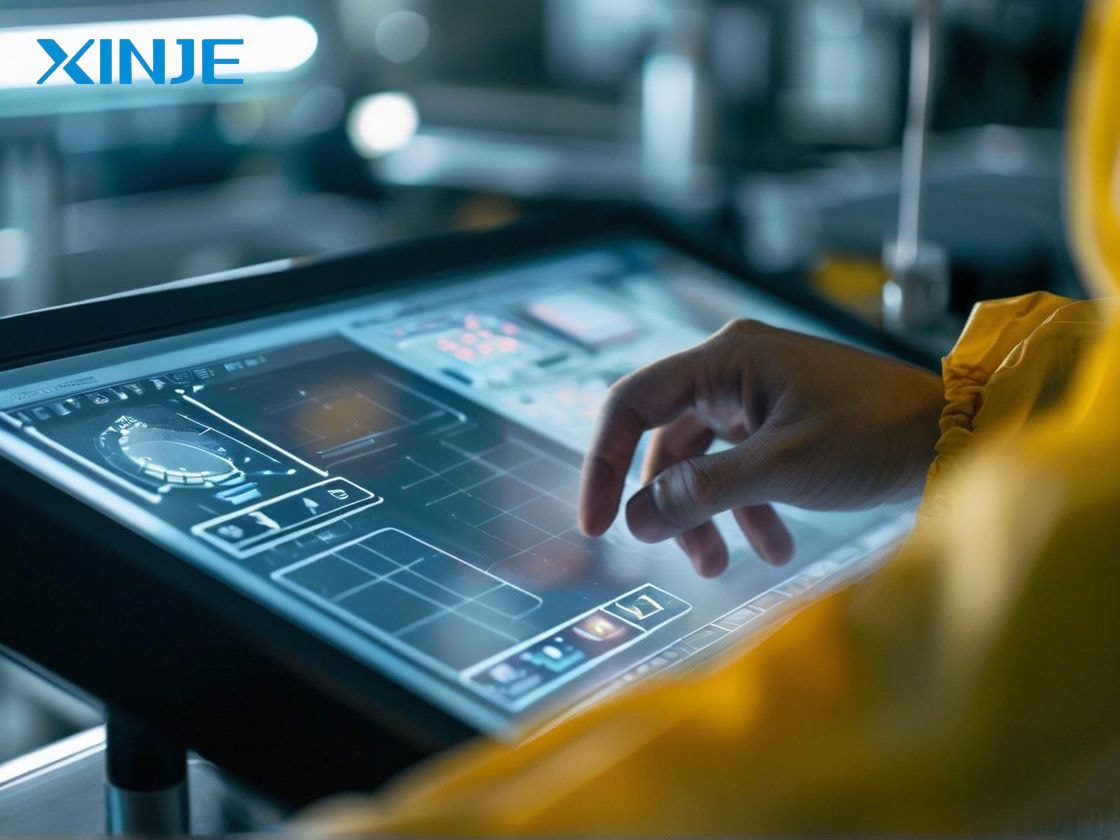
Once the likely cause has been diagnosed, the next step is to implement an effective solution. Here are structured troubleshooting and repair strategies based on the source of the problem:
- Restart the HMI System: Like other computer systems, the HMI can experience temporary glitches. A complete reboot often clears memory errors or stuck processes that may be affecting the touchscreen.
- Update or Reinstall the Firmware: If the problem is software or firmware related, download the latest version from the manufacturer’s website and install it.
- Check environmental factors: If you are operating in a humid or dusty environment, consider using an IP65/IP67 rated enclosure or installing a touchscreen heater or air conditioner enclosure for extreme temperatures.
- Touch Panel Replacement: If a hardware failure is confirmed and cleaning or calibration is ineffective, you may need to replace the touch panel with a new one.
What should you do to prevent an Unresponsive Touchscreen?
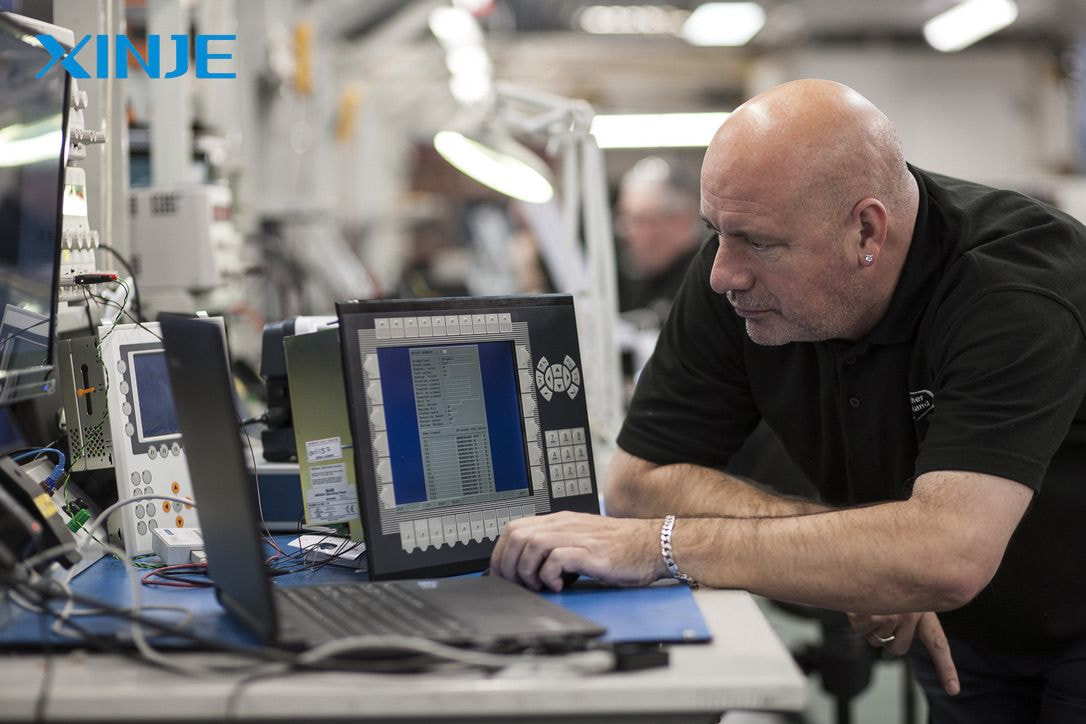
Touchscreens can fail for various reasons, including hardware failures and software errors. However, there are a few things you can do to minimize the chances of your touchscreen becoming unresponsive.
- Regular cleaning and maintenance include wiping the screen regularly with a soft, lint-free cloth to remove dust, grease, and debris. Avoid using harsh chemicals that may damage the touch surface or coating.
- Use a screen protector or protective case: Install an industry-standard screen protector to protect against scratches and minor impacts. For harsh environments (dust, water, chemicals), use an IP-rated case (e.g., IP65 or IP67).
- Avoid excessive force: Instruct operators not to press too hard on the screen and to use a stylus when necessary, especially for resistive touch screens.
- Monitor Environmental Conditions: Control the temperature and humidity around the HMI panel. Use a heater or air conditioner if the system must operate in a harsh environment.
- Check and protect connections: Periodically inspect the cables and connectors inside the HMI panel. Make sure there are no loose or corroded connections that could affect signal transmission.
- Use high-quality equipment: Choose HMIs from reputable manufacturers with rugged designs that are suitable for industrial conditions.
Conclusion
Unresponsive touchscreen issues in HMI systems can be frustrating and costly, but understanding the causes and implementing a systematic troubleshooting process can minimize disruption. From physical damage to software errors to environmental conditions, knowing how to detect and fix these issues is critical for engineers, technicians, and plant managers.
To prevent future problems, operators need to implement a regular preventive maintenance schedule. Enhance employee training to recognize the early signs of touchscreen degradation. and keep firmware up to date and use high-quality, industry-standard HMIs specifically designed for your environment. Don’t wait until your system breaks down, proactive care is the key to sustainable productivity and efficiency.