What is the HMI OPC UA Integration? OPC UA (Open Platform Unified Communications Architecture) is a service-oriented, platform-independent communications protocol designed to ensure interoperability between disparate industrial systems. When integrated with HMIs, OPC UA enables secure, standardized, and real-time data exchange across PLCs, SCADA systems, MES, and cloud platforms.
By integrating OPC UA with HMI systems, manufacturers achieve more connected, intelligent, and responsive operations. This is an important step toward achieving the process automation goals of Industry 4.0.Â
What are the benefits of OPC UA Integration?
Integrating OPC UA with HMI systems and many other systems has brought many technical and operational advantages, such as:
- Vendor Interoperability: OPC UA is vendor-independent. HMIs using OPC UA can communicate with devices from different manufacturers without the need for custom drivers or middleware.
- Secure Data Transmission: Cybersecurity is a growing concern in industrial networks. OPC UA includes built-in security features such as encryption, authentication, and user access control
- Scalability and Flexibility: Whether deploying a single machine interface or a plant-wide SCADA system, OPC UA can easily scale from local HMIs to cloud-connected applications.
- Data modeling for intelligent applications: OPC UA enables sophisticated data modeling, allowing HMIs to interpret complex data structures beyond simple tags and variables.
What types of devices can work with OPC UA?
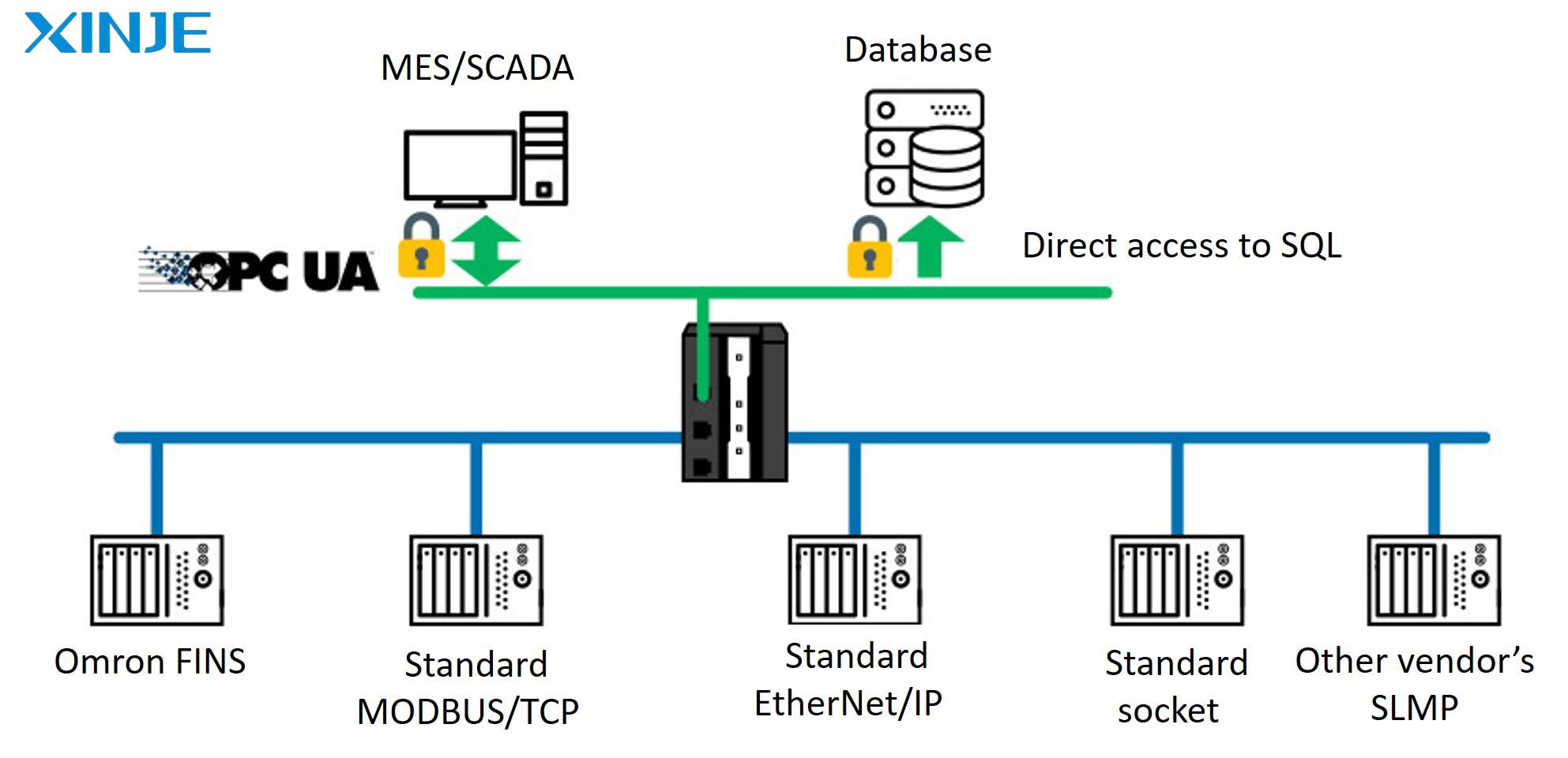
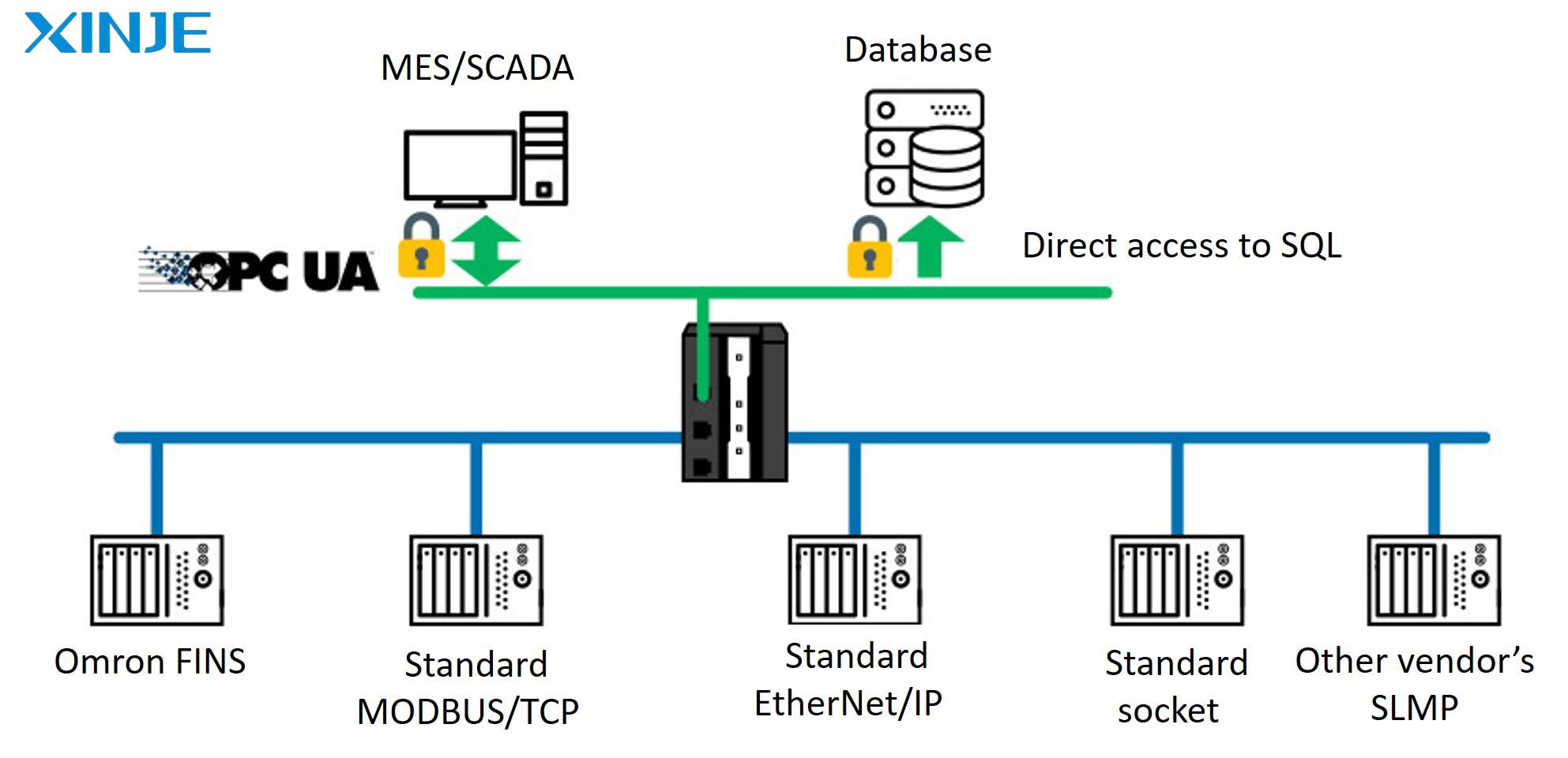
The strength of OPC UA lies in its ability to unify communication between multiple devices. Devices that typically support or integrate well with OPC UA include:
- Programmable Logic Controllers (PLCs): Most modern PLCs from leading brands such as Siemens (S7-1500 series), Allen-Bradley, and Beckhoff have native OPC UA support.
- SCADA and MES Systems: Supervisory Control and Data Acquisition (SCADA) and Manufacturing Execution Systems (MES) use OPC UA to obtain data from HMIs and PLCs for centralized monitoring and control.
- Industrial Computers and Edge Gateways: Industrial computers or edge devices typically act as OPC UA clients or servers to collect, filter, and transmit data to the cloud or higher-level systems.
- Cloud Platforms and IIoT Solutions: Cloud services such as Microsoft Azure IoT, AWS IoT, and Siemens MindSphere offer OPC UA connectivity for remote monitoring, big data analytics, and AI applications.
- Sensors and Actuators: With the advancement of Industry 4.0, today’s smart sensors and actuators increasingly come with embedded OPC UA servers, allowing direct communication with HMIs and controllers.
- Robots and CNC machines: Computer numerically controlled (CNC) machines and robots in modern factories often use OPC UA for real-time diagnostics, coordination, and maintenance monitoring.
The range of devices that can connect to OPC UA is vast and varied, reflecting the breadth of coverage of the protocol and its popularity.
Where is OPC UA integration used?
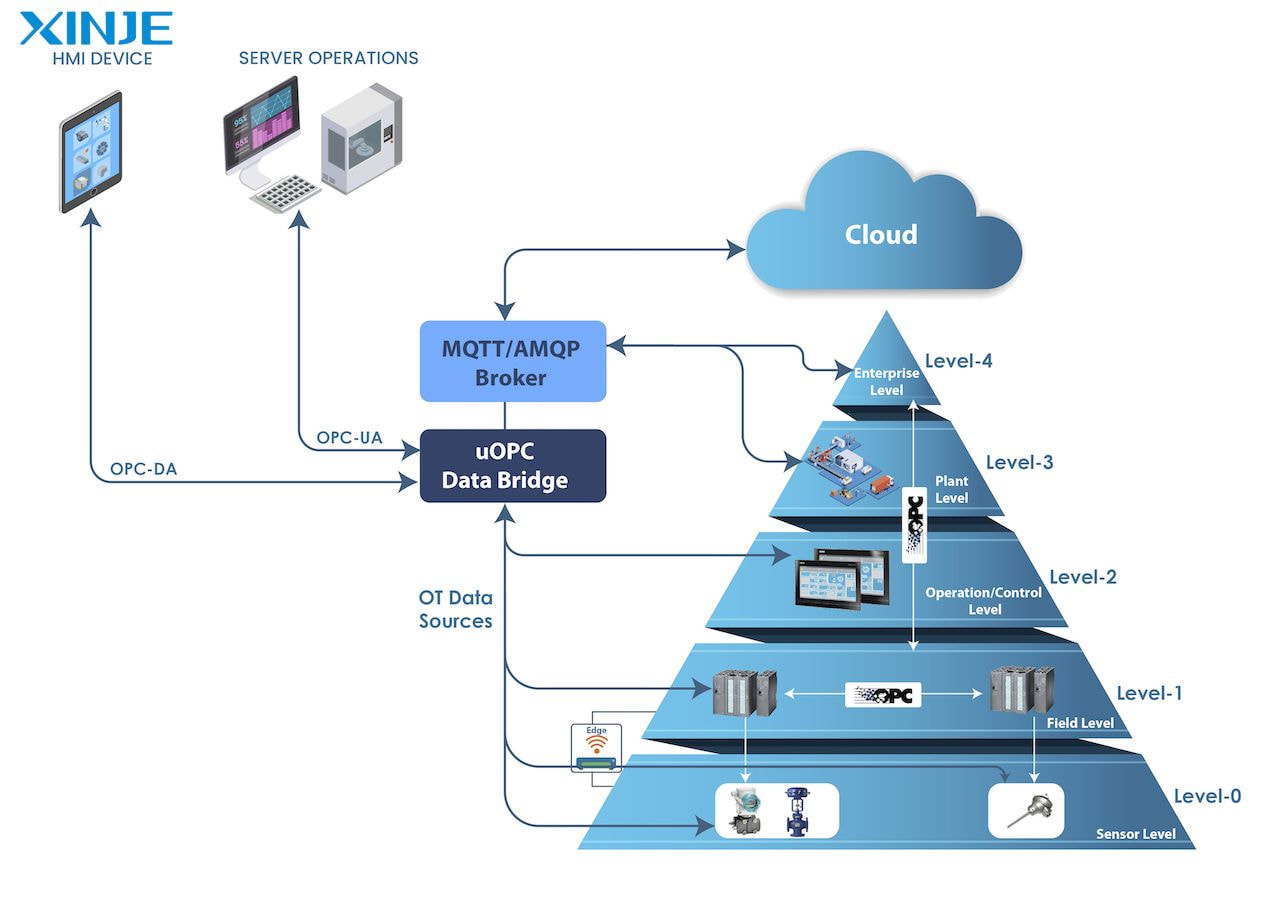
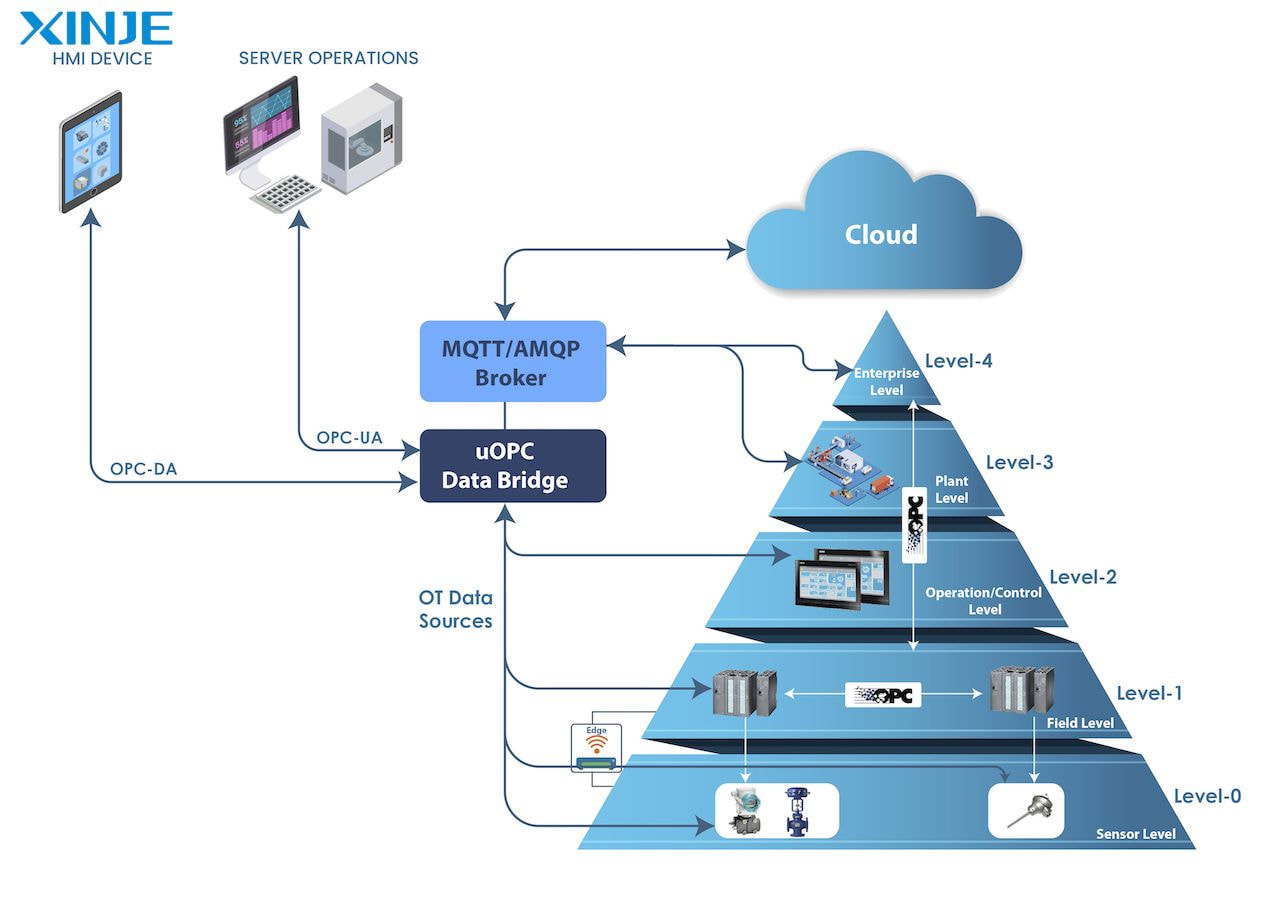
OPC UA integration with HMI systems is widely applied in many industries seeking efficient, standardized, and secure communication. Some notable applications include:
- Automotive manufacturing: In highly automated assembly lines, OPC UA enables synchronization between robots, PLCs, HMIs, and quality systems to ensure error-free production.
- Food and beverage processing: OPC UA provides real-time control, hygiene monitoring, and batch traceability through seamless integration of sensors, mixers, and packaging equipment.
- Pharmaceutical industry: With stringent regulatory requirements, OPC UA ensures accurate and traceable data collection on machines and control systems, supporting GMP and FDA compliance.
- Oil and gas: In remote and hazardous environments, OPC UA supports secure remote monitoring and control via HMI and SCADA systems.
- Water and Wastewater Treatment: OPC UA HMI integration allows cities to monitor tank levels, flow rates, and chemical dosing in real time from centralized control rooms.
- Smart Buildings and Energy Systems: Building Management Systems (BMS) use OPC UA to communicate with HVAC, lighting, and energy meters through user-friendly HMI dashboards.
What is the difference between OPC and OPC UA?
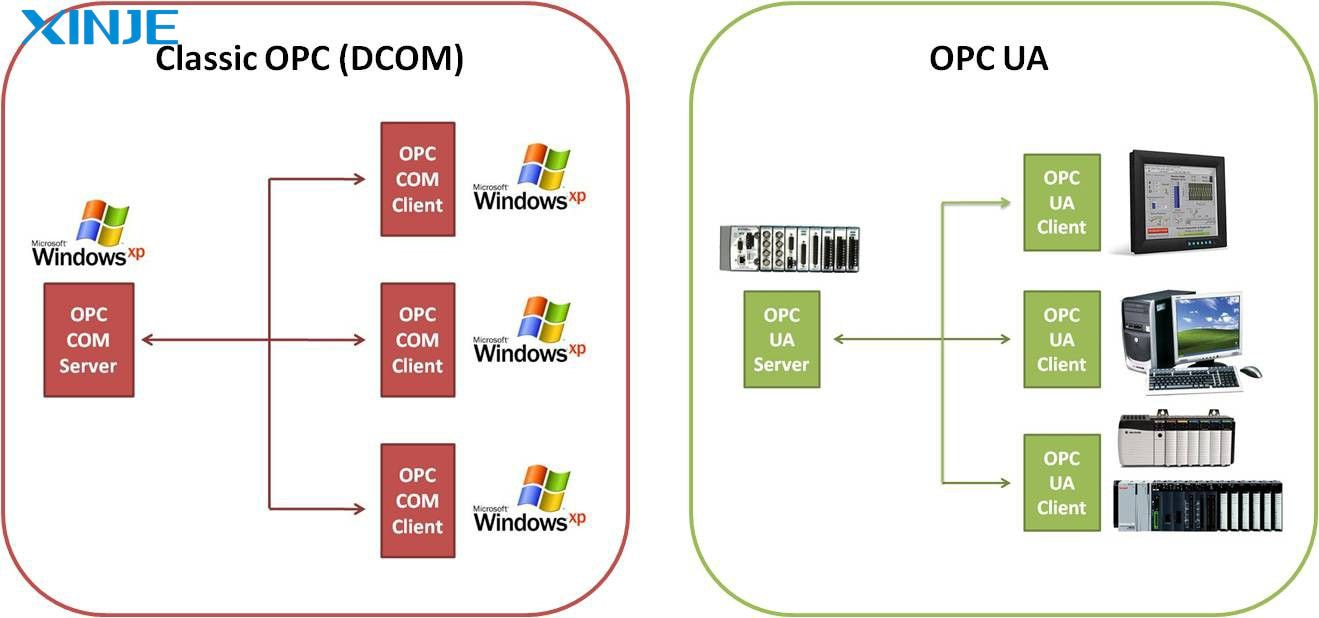
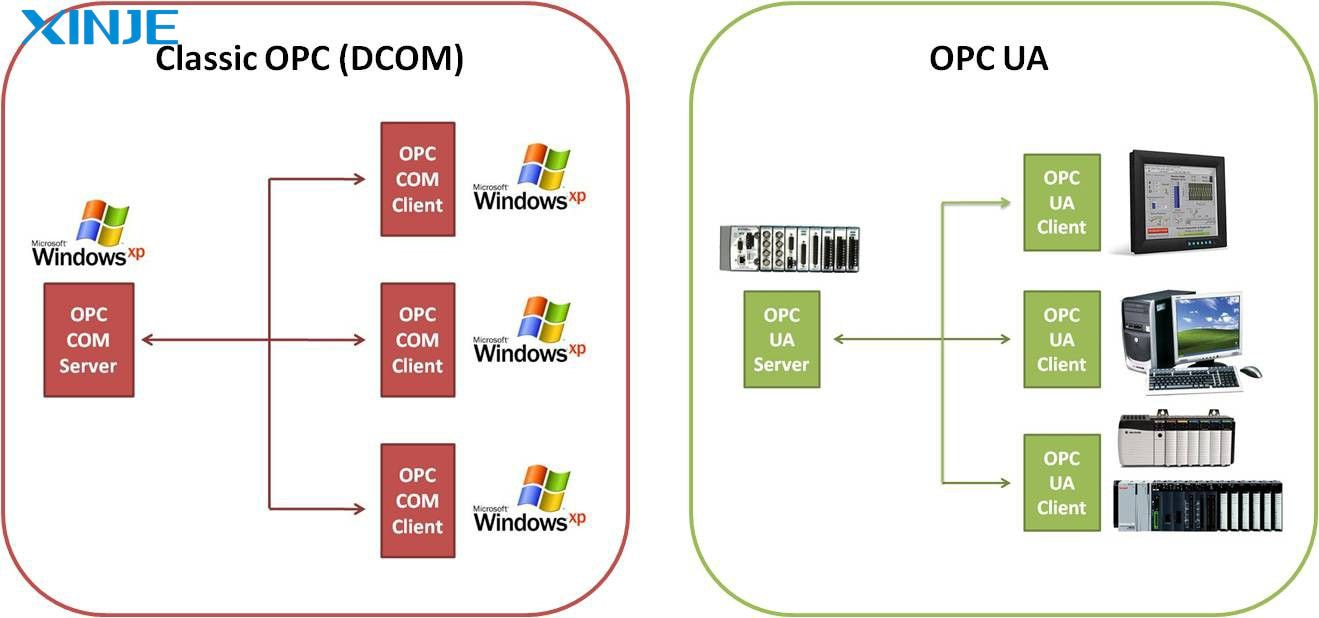
While both OPC and OPC UA have the functionality to enable communication between industrial devices, there are important differences between the two that operators need to understand.
Feature | Classic OPC | OPC UA |
Security | Limited | Built-in encryption, authentication |
Communication Protocol | DCOM | TCP/IP, HTTPS, MQTT… |
Cloud Readiness | Not suitable | Designed for IIoT and the cloud |
Data Modeling | Simple tags | Advanced data structures |
Comparing Classic OPC and OPC UA, OPC UA is still a modern, more capable, and more secure development version of the classic OPC standard, suitable for today’s industrial digital transformation process.
What are the OPC UA protocol trends in 2025?
OPC UA continues to grow in 2025, paving the way for more intelligent, connected, and automated industrial systems. Trends for the protocol that will be widespread include
- Increased integration with AI and Predictive Maintenance: OPC UA enables access to granular machine data, which is being leveraged by AI algorithms to predict equipment failures and optimize operations.
- Expanding OPC UA FX: OPC UA FX is evolving, allowing field-level devices such as sensors and drives to communicate natively using OPC UA, eliminating the need for protocol converters.
- OPC UA and Cloud Integration: Cloud-native platforms increasingly offer built-in OPC UA connectors, allowing data from HMI systems to feed into dashboards, digital twins, and analytics pipelines in real time.
- Implement Security First: As cyber threats increase, organizations are prioritizing secure OPC UA deployments, including certificate management and encrypted sessions as standard practices in new projects.
Conclusion
Integrating OPC UA HMIs is not just a technical upgrade, but a strategic enabler for future-ready industrial systems. By adopting OPC UA, organizations unlock interoperability, improved security, and seamless scalability across their entire automation architecture.
From supporting multiple devices to enhancing cloud connectivity and predictive analytics, OPC UA equips HMI systems to handle the challenges of modern manufacturing. As the 2025 trend moves toward smarter, faster, and safer operations, integrating OPC UA into your HMI systems is a step toward digital transformation success.